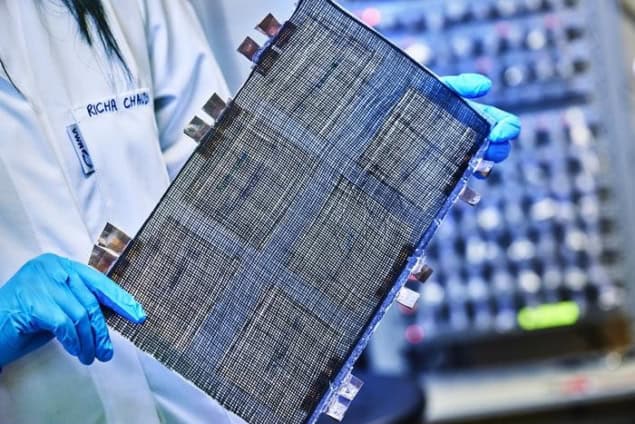
A prototype described as the world’s strongest functional structural battery has been unveiled by researchers in Sweden. The device has an elastic modulus that is much higher than any previous design and was developed by Leif Asp and his colleagues at Chalmers University of Technology. The battery could be an important step towards lighter and more space-efficient electric vehicles (EVs).
Structural batteries are an emerging technology that store electrical energy while also bearing mechanical loads. They could be especially useful in EVs, where the extra weight and volume associated with batteries could be minimized by incorporating the batteries into a vehicle’s structural components.
In 2018, Asp’s team made a promising step towards practical structural batteries – and was rewarded with a mention in Physics World‘s Top ten breakthroughs of 2018. That year, the team showed how a trade-off could be reached between the mechanical strength of highly ordered carbon fibres and the desired electrochemical properties of less-ordered structures.
Building on this, Asp and colleagues unveiled their first-generation structural battery in 2021. “Here, we used carbon fibres as the negative electrode but a commercial lithium iron phosphate (LFP) on an aluminium foil as a positive electrode, and impregnated it with the resin by hand,” Asp recalls.
Solid–liquid electrolyte
This involved using a biphasic solid–liquid electrolyte, with the liquid phase transporting ions between the electrodes and the solid phase providing mechanical structure through its stiffness. The battery offered a gravimetric energy density of 24 Wh/kg. This much lower than the conventional batteries currently used in EVs – which deliver about 250 Wh/kg.
By 2023, Asp’s team had improved on this approach with a second-generation structural battery that used the same constituents, but employed an improved manufacturing method. This time, the team used an infusion technique to ensure the resin was distributed more evenly throughout the carbon fibre network.
In this incarnation, the team enhanced the battery’s negative electrode by using ultra-thin spread tow carbon fibre, where the fibres are spread into thin sheets. This approach improved both the mechanical strength and the electrical conductivity of the battery. At that stage, however, the mechanical strength of the battery was still limited by the LFP positive electrode.
Now, the team has addressed this challenge by using a carbon fibre-based positive electrode. Asp says, “This is the third generation, and is the first all-fibre structural battery, as has always been desired. Using carbon fibres in both electrodes, we could boost the battery’s elastic modulus, without suffering from reduced energy density.”
To achieve this, the researchers coated the surface of the carbon fibres with a layer of LFP using electrophoretic deposition. This is a technique whereby charged particles suspended in a liquid are deposited onto substrates using electric fields. Additionally, the team used a thin cellulose separator to further enhance the battery’s energy density.
All of these components were then embedded in the battery’s structural electrolyte and cured in resin, using the same infusion technique developed for the second-generation battery.
Stronger and denser
The latest improvements delivered a battery with an energy density of 30 Wh/kg and an elastic modulus greater than 76 GPa when tested in a direction parallel to the carbon fibres. This makes it by far the strongest structural battery reported to date, exceeding the team’s previous record of 25 GPa and making the battery stiffer than aluminium. Alongside its good mechanical performance, the battery also demonstrated nearly 100% efficiency in storing and releasing charge, even after 1000 cycles of charging and discharging.

Lithium-ion batteries break energy density record
Building on this success, the team now aims to further enhance the battery’s performance. “We are now working on small modifications to the current design,” Asp says. “We expect to be able to make structural battery cells with an elastic modulus exceeding 100 GPa and an energy density exceeding 50 Wh/kg.”
This ongoing work could pave the way for even stronger and more efficient structural batteries, which could have a transformative impact on the design and performance of EVs in the not-too-distant future. It could also help reduce the weight of laptop computers, aeroplanes and ships.
The research is described in Advanced Materials.