Nanomachines will depend on our knowledge of friction, heat transfer and energy dissipation at the atomic level for their very survival.
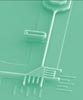
In the scramble to revolutionize the world with nanotechnology we must not ignore friction. Nano-scale devices based on moving molecular components have the potential to radically alter technologies such as energy storage, drug delivery, computing, communications and chemical manufacture. But getting these devices from the laboratory to the marketplace is far from guaranteed.
It is simply not clear if nano-scale structures can be made mechanically and chemically resistant enough to withstand the extreme conditions that can exist inside the human body, or in any of the other hostile environments where nanomachines might be expected to operate. The shearing-off or melting of even a single layer of atoms can easily spell death for a nanomachine, and this is before commercial issues such as energy efficiency or profitability are addressed (see “The future of nanotechnology” Physics World August 2004 pp25-29).
The chemical and mechanical stability of moving nanostructures underlie the field of nanotribology – the study of friction and wear at atomic length and time scales. Last year turned out to be a banner year for this field, with an impressive upsurge in both experimental and theoretical work. This included substantial progress in our understanding of how mechanical instabilities contribute towards overall friction levels, and pioneering experimental techniques for bridging the gap between nano-scale and macroscopic phenomena.
Centuries-old friction
Historically the study of friction has been driven by economic considerations. For example, by paying more attention to what is already known about friction and wear, developed countries could save up to 1.6% of their gross national product. The loss – which is estimated to be as much as $100 billion per year in the US alone – arises because entire mechanical systems are routinely discarded whenever only a few of their parts are badly worn. And the energy consumed in the manufacture of a car, for example, is equivalent to that consumed in 100,000 miles of operation.
Given how little actually is known about friction, the potential impact on the economy and society associated with an improved knowledge of tribology is nothing less than mind-boggling! But progress in this field has been slow, and the interest of physicists in tribology has waxed and waned over the centuries.
Modern tribology began some 500 years ago, when Leonardo da Vinci deduced the laws governing the motion of a rectangular block sliding over a planar surface. Hundreds of years later, in 1699, the French physicist Guillaume Amontons published the first formal account of the classical, macroscopic friction laws. He found that the frictional force that resists the sliding motion between two interfaces is directly proportional to the perpendicular force that squeezes the surfaces together. Moreover, the frictional force is independent of the apparent area of contact. A brick standing on its end, for example, experiences the same friction as when it is laid flat. Charles Augustin de Coulomb later proposed a third law of macroscopic friction, which states that at ordinary sliding speeds the frictional force is independent of velocity.
These classical laws of friction hold for a remarkably wide range of materials, but they are equally remarkable in terms of how difficult it is to derive them from fundamental atomic or molecular principles. It is reminiscent of the situation in thermodynamics before statistical mechanics came to the rescue. The roughness of a surface was ruled out as a possible mechanism for most types of friction by the 1970s, and was replaced by the notion that the atoms in two materials may bond together and resist sliding as the materials are pressed into contact. Unfortunately, this “adhesive bonding” view of friction, which was promoted by Philip Bowden and David Tabor of Cambridge University in the 1960s, does not make any predictions about the magnitude of the frictional force or the mechanism of energy dissipation that gives rise to it.
Tabor ultimately became convinced that friction in the absence of wear – the tearing off of fragments along the sliding interface – must be due to the build up of strains between the interfaces that were then released in the form of atomic vibrations called phonons. Phonons, which were first suggested as a mechanism for friction by G A Tomlinson in 1929, are produced when the mechanical energy required to slide one surface over another is converted to sound, which is eventually transformed into heat (figure 1). Tabor was aware of no experimental evidence that such phononic friction existed, but he was soon to be vindicated by a growing community of surface scientists.
Today, there are perhaps 100 physicists and other scientists worldwide who lead work on nanotribology (figure 2). This situation has come about largely due to the availability of new experimental and theoretical techniques in the 1970s and 1980s, which gave rise to a renaissance in experiments exploring the microscopic origins of friction. Devices such as the quartz crystal microbalance and the lateral force microscope, for example, can measure the friction due to a single contacting interface. This scenario is vastly simpler to study than that of macroscopic objects, where friction reflects the collective behaviour of a multitude of contacts.
In 1991 the present author and colleagues, then at Northeastern University in Boston, used a quartz crystal microbalance – a device that is so sensitive that phonons modify its vibrational properties – to measure the friction of krypton monolayers that were sliding on a gold surface. Our results ultimately proved the existence of phononic mechanisms of friction, whereby phonons are excited in the adsorbed layers. Indeed, to the best of my knowledge, the term “nanotribology” first appeared in print in the title of the paper announcing these results (see Krim et al. in further reading).
To stick or to slip
One of the most common types of friction at the macroscopic scale, and also one of the most frustrating, is static friction. This is the force that is needed to get an object to move in the first place, and it is almost always larger than the force that is needed to keep the object moving. Among other factors, static friction can depend on how long the two surfaces have been in contact with one another.
A closely associated phenomenon is that of “stick-slip” friction, whereby the transition from static to sliding friction leads to repetitive sticking and slipping at certain speeds. This is the mechanism responsible for the familiar screeching noises associated with car brakes.
For monolayers sliding along atomically uniform substrates, however, there is essentially no static friction. Indeed, the friction in these systems can be up to 105 times less than that for macroscopic lubricants such as graphite. This raises questions about the fundamental dissipation mechanisms that are at work in systems at different scales. For example, do these mechanisms play a substantive role in wear-free friction at the macroscopic scale, or do they dominate only in simple geometries? Is a lack of a stick-slip phenomenon always associated with exceptionally low friction levels, and, if so, can the results be applied to meso- (intermediate) and macro-scale systems? A series of new experiments is now under way to unravel these mysteries.
In 2004 Ernst Meyer and co-workers at the University of Basel used a lateral force microscope to observe the transition between stick-slip and continuous sliding for the first time. This instrument, which is common in nanotribology research, is a modification of an atomic force microscope and consists of a sharp tip mounted on a flexible cantilever. As the tip is dragged over the surface of a sample, the cantilever is deflected by an amount that depends on the friction between the tip and the substrate.
Meyer and colleagues monitored silicon-tipped cantilevers as they slid along atomically uniform crystals of sodium chloride. By varying the normal load on the cantilever tip, the system could be made to enter (and return from) a state of ultralow dissipation with no mechanical instabilities or stick-slip behaviour. These data were modelled successfully using a Tomlinson model, in which friction is the result of mechanical instabilities that give rise to phonons. While the results support the idea that vibrational mechanisms can cause energy dissipation in a variety of geometries, they do not completely rule out other mechanical models.
For example, Alexander Filippov of the Donetsk Institute for Physics and Engineering in the Ukraine and colleagues at Tel Aviv University in Israel have developed a mechanical model of friction at the micro-scale that is based on two rigid plates separated by elastic springs. The springs can spontaneously break and reform upon contact to represent the collective behaviour of the constituent molecules. An external “drive” force is then applied to the system, and the rate of bond rupture and formation with respect to the sliding speed determines the macroscopic response. Filippov and co-workers found that stick-slip behaviour is present in cases where there is a co-operative rupture of bonds, and the presence of static friction depends on experimental conditions and timescales.
Their model therefore establishes a relationship between macroscopic observables and the dynamics of microscopic bonds at the sliding interface. Force measurements alone do not allow one to establish a microscopic picture of friction, but it will be essential to understand the links between macroscopic response and microscopic dynamics if we are eventually going to unravel the origins of friction.
Superlubricity has stuck
The relative structure of two surfaces that are in sliding contact with each other also has a profound influence on the phononic contributions to friction. For instance, friction is especially great when the surface atoms are equally spaced and aligned with the counterface atoms against which they are sliding. Although the vast majority of sliding interfaces do not meet these conditions, friction in such “commensurate” systems can be more than 1010 times greater than the friction between “incommensurate” surfaces.
The possibility that phononic friction can be exceptionally small between two atomically incommensurate surfaces has been referred to as superlubricity by some researchers. This is unfortunate, since the “resistance” does not drop to zero, as in the case of superconductivity or superfluidity, but instead simply arises from low levels of phononic friction associated with the structural incompatibility of the sliding surfaces. Even if phononic friction was to drop to zero, a very small amount of frictional energy would still be dissipated due to electronic and/or photonic excitations.
In March last year, Martin Dienwiebel and co-workers at Leiden University in the Netherlands found evidence for “superlubricity” in graphite using a purpose-built force microscope that could measure forces as low as 15 pN (15 x 10-12 N). The Leiden team captured a graphite flake on the end of a tungsten tip and measured the friction as it was slid along a crystalline graphite substrate (the contact area of the flake was estimated to be a mere 96 atoms). The researchers then brought the flake in and out of perfect commensurability with the graphite surface by rotating it into positions where the atoms were no longer aligned. As expected, high levels of friction were present in the commensurate positions and extremely low friction was found when the surfaces were incommensurate.
The Leiden experiment provides further evidence that Tomlinson-type mechanical vibrations are a fundamental source of macroscopic friction, and Dienwiebel and co-workers claim that such vibrations could account for the lubricity of graphite at the macroscopic scale. However, this is not the first time that nanotribologists have linked nano-scale lubricity to macroscopic friction, the tacit assumption being that extremely low friction coefficients and/or extremely high interfacial slip levels at the atomic level are in some way linked to macroscopic lubriciousness. The trouble is that the coefficients of friction measured in nanotribological experiments and in macroscopic “tribotests” routinely differ by orders of magnitude.
To test this microscopic hypothesis, our group recently used a quartz crystal microbalance to monitor the nano-dynamical motion of molecules in organophosphate film samples in which the macroscopic friction coefficients are well known. We were astonished to discover that molecules that could flex or slide even just a little in response to the oscillatory motion of the microbalance were linked to low friction levels at the macro-scale. Put another way, exceptionally low friction at the atomic scale was not a prerequisite for the substantial reduction in macroscopic friction.
Last year Martin Muser of Johannes Gutenberg Universitat in Mainz, Germany, explored theoretically what happens when two chemically inert materials slide with respect to one another. Muser allowed the interactions between the two materials to vary, which had a great impact on overall friction levels. For example, whenever elasticity dominates at all length scales, the two solids move essentially as rigid blocks. In the absence of wear this would result in exceptionally low friction levels, which suggests that 3D crystals that form a perfectly flat 2D interface should exhibit super-low friction levels. Muser points out, however, that this “structural lubricity” is very likely to be lost in its entirety for the vast majority of everyday surfaces. The applicability of nanotribological results for meso and macro applications thus remains open to debate.
The meso-scale regime
Microelectromechanical systems (MEMS), which integrate mechanical and electronic components, are currently fuelling a billion-dollar industry. But tribological issues are holding back the development of a myriad of MEMS devices – such as rotary gears, microturbines and relay switches – that could form the building blocks for more sophisticated “on-chip” systems. Indeed, there are no commercially available MEMS devices that contain surfaces that are in sliding contact simply because MEMS are exceptionally susceptible to friction and wear. And you cannot simply add traditional lubricants such as oil because these microfabricated structures succumb rapidly to capillary forces in the presence of liquids (figure 3).
Michael Dugger and co-workers at Sandia National Laboratories in the US have recently developed on-chip MEMS friction testers capable of detecting friction forces as small as 5 μN. A MEMS friction tester typically consists of tens of contact regions, while nanotribological techniques typically involve only one. The devices therefore help to bridge the gap between nano- and macro-scale phenomena. Although this approach only works for simplified contact geometries, the surface structure and chemistry of the devices duplicate those found in more complicated systems that have been targeted for certain applications. The testers are also proving to be useful in fundamental studies of friction.
Maarten de Boer and colleagues, also at Sandia, have recently developed an on-chip MEMS “nanotractor” that is dedicated entirely to fundamental studies of friction. This instrument, which is able to creep along a surface in nanometre steps, was designed specifically to study the validity of Amontons’ law – which states that the frictional force is proportional to the weight of the moving object – at the micro- to meso-scale (figure 4).
The nanotractor can measure both static and sliding friction coefficients, and is capable of progressive movements that mimic decreasing “weight”. Boer’s group, in collaboration with Bob Ashurst at the University of California at Berkeley, found that Amontons’ law holds for normal forces ranging from 50 μN to more than 1 mN. For forces less than 50 μN, the researchers found deviations from Amontons’ law indicative of the increased significance of molecular forces for very low external loads.
In addition, the Sandia team has discovered a “gross slip” phenomenon that happens before the static-friction limit had been reached. The gross sliding, which is about 100 times larger than theoretically expected, is very important in MEMS design, especially in cases where an object must be positioned with nanometre accuracy for optical applications. Work is now in progress to cast the experimental observations onto a firm theoretical footing.
The future for friction
The potential for nanotechnology to transform civilization as we know it is breathtaking, and the nanomechanical systems of the future will all require new atomic lubrication schemes to overcome the debilitating effects of friction. But in order for this impending revolution to be fully realized, we need a fundamental understanding of friction at the atomic to meso-scale.
Moreover, the tribological considerations of these systems will be an integral aspect of the system design, rather than the “after the fact” application of lubricants that is so common at the macro-scale. Finally, the dreams of a nanotechnological revolution will only be realized by training both existing and future scientists and engineers in nano-scale phenomena – an area that is largely absent, for instance, in the present curriculum. The time to start is now.