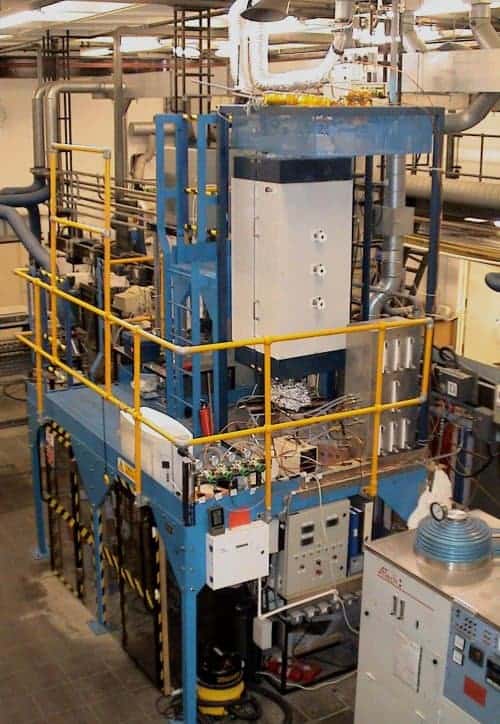
Physicists in the UK are the first to make fibres from carbon nanotubes in a simple one-step process that could be adapted for commercial production. The fibres, which are just a few micrometres across, are claimed to be stronger than any known material and consist of hundreds of thousands of nanotubes bound together. According to its inventors at the University of Cambridge, the new material could find use in a host of applications from bullet-proof vests to flat-panel displays.
Despite having walls only a few atoms thick, carbon nanotubes are remarkably strong yet lightweight strands that could someday be made into fibres that could be woven into extremely durable fabrics. While several techniques have been developed to spin nanotubes into larger fibres, these are all multistep processes that are not viable on an industrial scale.
Now, Cambridge’s Krzysztof Koziol and colleagues have come up with a much simpler one-step process to make nanotube fibres (Sciencexpress 1147635). The team start with a hydrocarbon feedstock, such as ethanol, hexane, methane or diesel. Next, they inject this feedstock into a furnace along with a small amount of iron-based catalyst called ferrocene. The feedstock breaks down into hydrogen and carbon and the carbon is then restructured on particles of iron catalysts as long, thin-walled nanotubes.
Aerogel-like structure
The nanotubes grow very quickly in the furnace and form an aerogel-like structure. As the furnace is open at one end, the aerogel can be pulled out with a metal rod, which stretches the fibre into a fine thread that can be wound continuously. Winding is done at a rate of up to 50 metres per minute and several kilometres of the fibres can be made in a day.
“At gauge lengths below 2 mm, some of our fibres have strengths greater than any material known to mankind,” Koziol told physicsworld.com. “The average strength is similar to Kevlar — the material that most body armour is made of.”
Apart from good mechanical properties, strength and toughness, the materials also have high electrical and thermal conductivities. They retain their mechanical properties at temperatures of up to 300°C in air too, which is impossible for other such fibres. “Moreover, knots on these fibres do not influence mechanical performance either — something that is a huge issue with other high-performance carbon and polymeric fibres,” explains Koziol.
“One of main applications for this new material is in super-strong bullet-proof vests,” says team leader Alan Windle, also at Cambridge. “Related applications include strong containment surrounds for the fan blades of jet engines: if the blade becomes detached, the fibres would prevent it from flying out of the engine and damaging the aircraft.”
The fibres could also find use in bomb-proof bins and in blast protection for tank engines and other armoured vehicles. “Hi-tech smart fabrics may be on the agenda too,” adds Koziol. “There is also a great potential to provide an alternative to copper or aluminium conductors for electric power transmission.” The nanotubes might even be collected as transparent conductive films for use in flat-panel displays and solar cells.
The team, which includes researchers from the US Army, is now busy exploring how to achieve super-high strength in longer lengths of fibre. “We’re going to develop the fibre’s chemistry, try to get rid of any defects and work on the manufacturing process,” says Windle. “To make commercial use of this material, we now need to upgrade the process to an industrial level.”