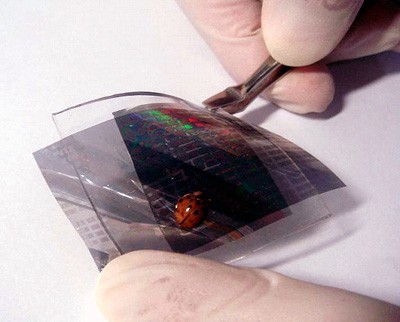
A team of South Korean researchers has produced a simple, highly sensitive and flexible sensor based on the intermolecular forces between “nanohairs”. The device was fabricated as a synthetic equivalent to human skin. It is capable of distinguishing and measuring pressure, as well as shear stress and torsional forces, and can be easily and economically manufactured.
Reproducing the qualities of skin in a suitable synthetic sensor has proved a challenge because there are severe design constraints on such sensors that make them highly complex to fabricate. Most significantly, the devices need to be thin and flexible enough to wrap around areas of high curvature such as fingers and toes without being damaged. This is problematic because most of the materials used in electronics, such as silicon and germanium, are, in their bulk state, hard and brittle.
Epidermal electronics
Various research groups have made progress in “epidermal electronics” using a variety of methods. John Rogers’ group at the University of Illinois at Urbana-Champaign, for example, has used a transfer-printing method to cut individual silicon chiplets to micrometre size and attach them to a flexible substrate, allowing the researchers to create wireless heart-rate monitors that stick to the skin like temporary tattoos using just Van der Waals forces. Other groups have created flexible electric circuits using carbon nanotubes or graphene. But doubts remain about whether such approaches can realistically be used to produce an affordable sensor able to measure and distinguish between different types of forces on a large area of “skin”, as the circuitry would become increasingly complex and the engineering demands ever greater.
Instead, researchers at Seoul National University (SNU), together with a colleague from Rogers’ group in Illinois, have created a simpler sensor based on piezoresistance – where changes in the electrical conductivity of a semiconductor are caused by applied mechanical stress. Their design uses two slightly separated thin layers of a flexible polymer – polymethylsiloxane (PDMS) – each covered with a very thin layer of platinum to make them conduct electricity. The team then covered the inner surface of both layers of polymer with a dense carpet of platinum-covered “nanohairs”. Van der Waals forces between the intertwined hairs cause the two layers of polymer to be drawn together like a kind of molecular Velcro. However, the hairs’ resistance to bending simultaneously acts to push them apart. The two forces balance at an equilibrium distance.
Platinum tips
As the hairs are covered with platinum, they provide an electrical connection between the otherwise separate layers of polymer. Any pressure on the sensor at a particular point brings the two layers closer together, thus increasing the amount of contact between the hairs and reducing the electrical resistance. When the pressure is removed, the two layers return to their equilibrium separation and the resistance returns to normal. Shear and torsion forces also affect the membrane double layer, albeit in more complex ways. Using established engineering technology, the researchers were able to collect resistance measurements from a closely spaced 2D array of points on the sensor and use them to distinguish and measure pressure, shear and torsion.
The researchers have shown their device’s sensitivity via several demonstrations. They measured a small water droplet bouncing on a hydrophobic surface and also measured the change in the speed and intensity of a volunteer’s heartbeat after vigorous exercise using a sensor attached to the artery at their wrist. They also demonstrated the sensor’s ability to measure the spatial distribution of pressure by using an interconnected sensor network of 64 pixels and placing two ladybird beetles at separate locations on its surface, mapping their pressure displacement as the insects walked over the sensor.
Principal investigator Kahp-Yang Suh explains that the techniques used in the manufacture of the sensor are easily reproducible and are economical. “It’s very easy to replicate this hairy structure using a standard soft-lithography process,” he says, “You can easily replicate from a single silicon master by a process called replica moulding, which is well established in our field.”
John Rogers is impressed by the researchers’ design. “It represents a clever way to combine materials, mechanics and structure layouts for a class of tactile sensor technology that has exceptional performance and the ability to integrate naturally with the surface of the skin,” he says. He is sceptical, however, about the researchers’ claim to have removed the need for complex electronic circuitry. “If one is interested in real, multifunctional artificial skin, then you need a lot more and different stuff, such as different sensors, electronic amplifiers and multiplexers. The need for and benefits of active electronics do not go away,” he adds.
The research is published in Nature Materials.