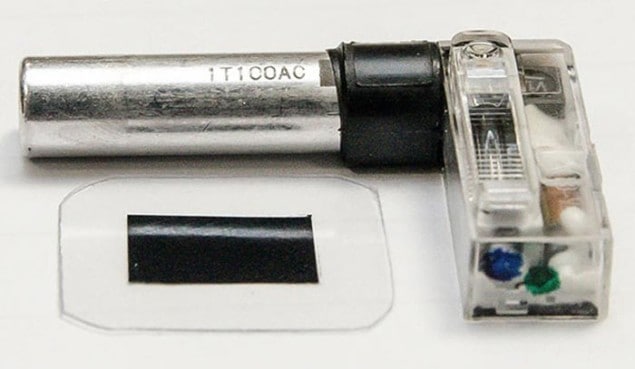
Researchers in Singapore have developed a prototype polymer capacitor that can store much more energy per unit volume than capacitors currently used to power camera flashes. The team claims that the technology could boost the performance of mobile-phone cameras, which often suffer from dim flashes. The group has already teamed up with a flash manufacturer with the aim of creating commercial products based on the technology.
For perfect pictures in low light, a camera flash must deliver a sudden, extremely bright pulse of full-spectrum light. Most flashes do this by creating an electrical discharge through xenon gas, which requires a relatively large capacitor. This makes it difficult to integrate xenon flashes in mobile phones, which tend to be smaller than dedicated cameras and packed with more components.
Ionized gas
A xenon flash consists of a glass tube filled with xenon gas with electrodes at either end. The gas has an extremely high resistance in its normal state, but when the potential difference across the electrodes becomes high enough, it ionizes. The resistance then suddenly drops, allowing the capacitor to discharge and creating sudden heating of the gas and a short pulse of intense light.
To fire a xenon flash, hundreds of volts must be applied across the electrodes in a very short time. This is done using electrical energy that is stored within a capacitor by charging conducting plates separated by a dielectric medium. However, just like the xenon gas, the dielectric medium has a finite breakdown field. To store more energy without exceeding the breakdown field, more dielectric – usually aluminium oxide – is needed and this increases the size and weight of the capacitor. As a result, many mobile phone manufacturers use LED flashes, which do not require unwieldy capacitors but are not as bright as xenon devices.
Higher breakdown field
Now Lee Pooi See from Nanyang Technological University (NTU) in Singapore and colleagues have developed a new multilayer polymer dielectric with a much higher breakdown field than the materials used in traditional camera capacitors. This means the same amount of energy can be stored in a much smaller volume. Polymer capacitors are not a new invention, and are often used in high-end electronics because they are more stable than conventional capacitors and can discharge more quickly. But previous polymers used in capacitors have had a lower maximum-energy density than conventional designs.
Lee explains the secret of the new material, which her group has applied for a patent on. “It’s a very stable polymer – not just chemically but thermally and electrically as well,” she says. “Often when the breakdown field is low for other polymers it’s due to defects or instability of the chemical structure, but our polymer isn’t prone to defects or moisture issues.” A capacitor four times smaller can store the energy required to power the same xenon flash. As well as camera flashes, the capacitor should have uses in other consumer electronics where miniaturization and high speed are important.
Commercial ambitions
The invention has caught the eye of Singapore-based Xenon Technologies, the world’s largest manufacturer of xenon flashes. The company has entered a commercial partnership with Lee’s team at NTU to turn the laboratory prototype into a viable commercial product.
The collaboration is hoping to produce a working commercial prototype by September, after which how to produce it industrially will become important. “If we want to have mass production, we cannot just rely on the lab-based instruments we are currently using,” says Lee, “I would foresee that some investment from industry is required if it’s really attractive to push forward towards a product.”
Jack Tuen, chief executive of Xenon Technologies, is upbeat about the partnership: “This project will yield a breakthrough solution for the digital-imaging industry, which will be the world’s smallest xenon flash.”