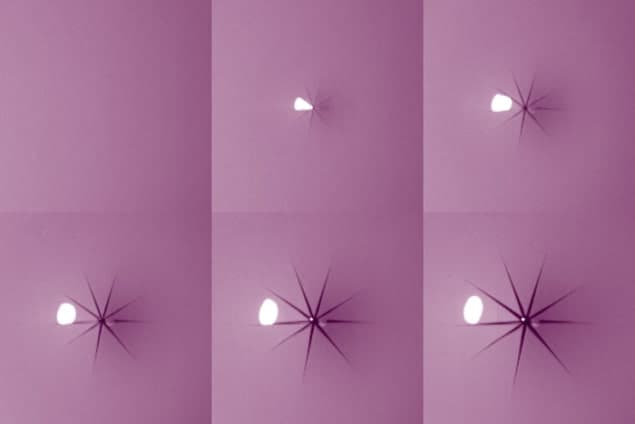
They are the bane of car owners worldwide: star-shaped cracks that spread out from a tiny chip until they cover the entire windscreen. So, to find out more about how these common but little-understood cracks grow, a group of physicists in France has carried out a series of simple experiments using brittle plates of both plastic and glass. The researchers found a scaling law that describes the cracking process in terms of several fundamental parameters – a finding that could have a wide range of applications from forensics to planetary science.
The impact experiments were done by Nicolas Vandenberghe, Romain Vermorel and Emmanuel Villermaux from Aix-Marseille University, who used an airgun to fire steel and ceramic projectiles at plates of either glass or poly(methyl methacrylate) – better known as PMMA, Plexiglas or Perspex – that were no more than 3 mm thick. The resulting cracking process was monitored using a high-speed camera for about half a second, which is the time it takes the initial shock wave to reach the edges of the plates. After the wave reaches the plate edge it reflects back to the centre and complicates the cracking process.
Counting cracks
Each individual experiment involved firing a projectile at a speed of between 5 m s–1 and 100 m s–1 at a plate and counting the number of cracks that emanate from the point of impact. Vandenberghe and colleagues found that, for both materials, the number of cracks increased in proportion to the square-root of a dimensionless impact velocity that is based on the material properties of the glass or the PMMA. This relationship was true for glass that was just 0.15 mm thick as well as PMMA plates varying in thickness from 0.5–3.0 mm.
The existence of a universal law, which was successfully able to describe all the data collected in the study, was based on calculations that express the number of radial cracks in terms of the velocity of the projectile and the thickness of the plate. Also considered were the material’s speed of sound, its Young’s modulus (stiffness) and fracture energy – the latter being the minimum energy required for a crack to form in a material.
The team also examined what happens when the projectiles are fired so fast that they travel at speeds beyond the point where just simple star-shaped cracks are seen. The researchers found that, as the velocity increases, circular cracks surrounding the point of impact also appear. For a given PMMA plate thickness, the radius of the first circular crack was found not to vary with projectile speed, but the velocity at which the first such crack appeared obeyed a scaling law that involved the thickness of the plate. The team was also able to calculate this relationship from the material properties of the plates.
Archaeology and meteorites
Vandenberghe told physicsworld.com that the main goal of the study was to get a better understanding of the fragmentation that occurs when an object strikes a thin material. This is crucial in forensics and archaeology, where shattered glass and other materials can provide important clues about past events. Further afield, it could also help planetary scientists gain better insights into the composition of planetary and lunar surfaces by studying how these materials crack when struck by meteorites.
In particular, Jupiter’s moon Europa is covered in cracks – leading scientists to believe that its surface is a thin layer of ice floating on a liquid sea. So far, Vandenberghe and colleagues have not had much success relating Europa’s cracks to the material properties of its surface. However, the researchers are now planning to do experiments on the cracking of plates floating on liquid to see if they can gain further insights.
The study is described in Physical Review Letters.