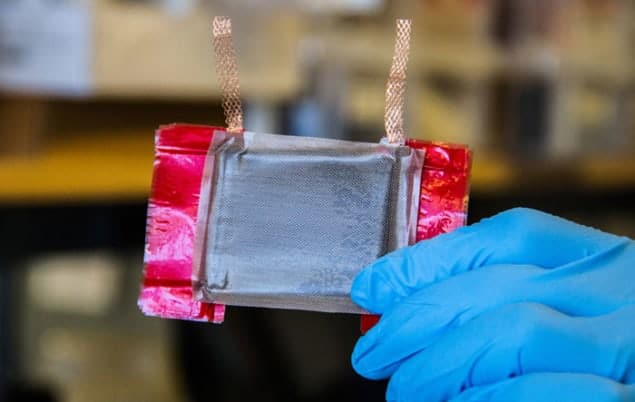
A paper-thin carbon-nanotube film that can heat and solidify the composite materials used in aircraft wings and fuselages, without the need for massive industrial ovens, has been developed by a team of researchers in the US. The film can be rolled onto industrial components to deliver uniform, controllable and efficient heating via conduction. When connected to an electrical power source, the heated film stimulates the polymer to solidify. The technique should provide a more direct, energy-saving method for manufacturing virtually any industrial composite, according to the researchers.
Large industrial components such as aircraft wings are often made of composite materials that have layers that must be bonded together. Bonding typically involves curing the composite materials at high temperatures in expensive, immobile ovens known as autoclaves. Heating metre-sized components to temperatures of several hundred degrees in autoclaves – large industrial vessels that treat materials using elevated pressure and temperature – is an energy-inefficient process: the ovens waste significant amounts of energy as they themselves must be heated before the thermal energy is carried to the components by convection.
Beyond the oven
The inspiration to use carbon nanotubes (CNTs) as conductive microheaters was based on previous studies, explains Seth Kessler, president of Metis Design Corporation in Boston, a spin-out company from the Massachusetts Institute of Technology (MIT). Together with researchers at MIT’s department of aeronautics and astronautics, the team developed a CNT-based microheater that can effectively be rolled over an arbitrary surface to provide direct heating. “We had been using carbon-nanotube-based resistive heating for de-icing applications and had then considered the possibility of using the same principle for curing,” he says.
The team’s “out-of-oven” approach avoids the use of autoclaves entirely, thereby allowing composite materials to be efficiently cured regardless of their size or shape, and irrespective of the availability of a nearby autoclave. Similar microheaters are already commercially available, but the researchers caution that “it’s not as simple as just buying material and pushing it on the surface”. Rather, significant engineering is required for each curing project to determine the appropriate resistivity and current-flow paths.
A thin sandwich
The researchers, led by Brian Wardle of MIT, first created a mesh of aligned CNTs, where each nanotube was approximately 400 microns long. Aligning the nanotubes ensured better electrical stability, which was critical since current needs to pass through the mesh to provide resistive heating. The group then added a copper mesh to create electrical contacts, and a composite surfacing film to ensure electrical insulation. Wardle and his team tested a roughly postage-stamp-sized sample of the film on a commercial, laminated composite commonly used in aerospace manufacturing. They attached a 30 V power supply directly to the two electrodes of the microheater and manually adjusted the input voltage to modulate the film’s temperature to yield a complete cure.
“We found about a 1000-fold difference in energy used for curing, resulting in a 50% cost reduction in the final production part,” says Kessler. Even though the group only tested a small piece of the mesh, the researchers envision that scaling up the size of the mesh to cover an entire aircraft wing will not present a challenge. “The larger the part, the more opportunity the current has to achieve a uniform front,” Kessler notes. “As long as the current flow is intelligently designed, the scale of the part is irrelevant.”
Furthermore, the extremely low surface density of the films (5–10 g/m2) means that they can be simply left on the material after curing without worrying about the extra weight. Kessler told physicsworld.com that by leaving the films in situ, other multifunctional capabilities may be realized, such as damage-detection based on resistance changes.
As different composites require different temperatures in order to fuse, the researchers also tested how hot the CNT film could actually get before it failed. The team found that the film’s failure point was at more than 537 °C. In comparison, some of the highest temperature aerospace polymers require temperatures up to 399 °C in order to solidify. “We can process at those temperatures, which means there’s no composite we can’t process,” Wardle says. “This really opens up all polymeric materials to this technology.” The researchers are now working with industrial partners to find ways to scale up the technology to manufacture composites large enough to make airplane fuselages and wings.
The research is described in Applied Materials and Interfaces.