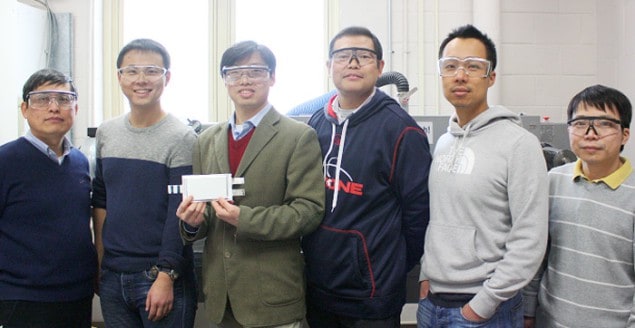
Batteries have long attracted environmentalists as an ideal energy-storage solution, but their dramatic power loss at below-freezing temperatures has prevented their use in practical outdoor applications such as electric cars. Researchers in the US have now shown that simply integrating a metal foil into lithium-ion batteries allows them to maintain optimum operating temperatures through resistive heating.
Chao-Yang Wang at Pennsylvannia State University has spent 20 years working on batteries and fuel cells, and says that low performance at sub-zero temperatures has been a long-standing problem for batteries – lithium-ion batteries included. He adds that they “tried many different ideas, but in the end we were very surprised that just a thin metal film was the solution”.
Warm currents
Indeed, the team’s solution requires nothing more than a thin metal foil integrated into the lithium-ion cell with a switch. When switched on, current will run through the foil, causing resistive heating to raise the temperature above freezing, at which point it can be switched off so that current no longer flows through the foil.
The added heating component works within 20–30 s. While adding just 1.5% to the weight and 0.04% to the cost of the battery, it provides a six-fold power boost at –30 °C.
Other attempts to incorporate features that get around the low-temperature power loss in lithium batteries have resorted to external heaters. These can be expensive, and use up a lot of energy because they raise the temperature of the battery case before heating the functioning components inside.
Direct heating
“For a battery to produce high power, you only need to heat the electrochemical interface,” explains Wang. “And for the interface – it’s low mass and low thermal budget.” By heating the electrolyte directly, the “all-climate battery” keeps activation times and the energy consumption of the heating component to a minimum. Wang sees the potential to further improve the efficiency of their all-climate battery because there is still some heat that is wasted raising the temperature of the bulk material. He envisages diminishing the capacity consumption on heating from 3–5% in the current demonstration to less than 1%, by refining the heat distribution.
The fast road to market
So how long before these all-climate batteries make it into commercial electric cars? Wang suggests that the simplicity of the solution may ease the technological aspects of commercializing the batteries. In addition, EC Power, a company that he founded at Pennsylvannia State University in 2011, made all of the batteries used for the current study and is ready to take orders. That said, the shortest path to large-scale uptake may be through a partnership.
“The main challenge for commercialization is on the business side, not the tech side – this is a rare example in this respect,” says Wang. “But the investment capital needed is huge, and requires high volume. Probably the fastest way is to team up with other larger companies and combine their large-scale manufacturing infrastructure with the technology from the start-up [EC Power].”
The research is published in Nature.
- A version of this article first appeared on nanotechweb.org