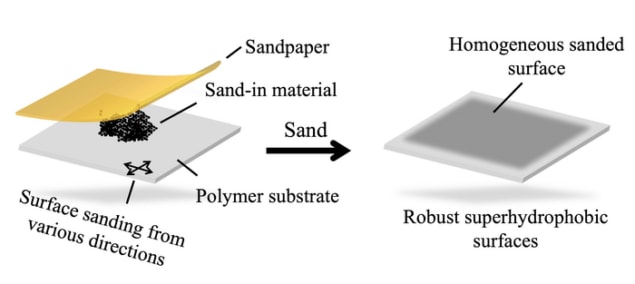
A new solvent-free technique could simplify the manufacture of superhydrophobic and anti-icing materials. The technique, which can be employed to make almost any surface extremely water-repellent, has numerous potential applications, including – but not limited to – aeroplane wings, biomedical devices, drag reduction systems, battery electrodes and catalyst surfaces.
Superhydrophobic materials are defined as those that repel water droplets with a contact angle (the angle at which the surface of the water meets the surface of the material) of more than 150°. These materials also have a low surface energy as well as a rough surface at the micron scale.
Current techniques to make such materials, however, are complex and often involve using harsh chemicals. A team of researchers led by James Tour and C Fred Higgs III of Rice University in the US has now developed a one-step, solvent-free sanding method that can create superhydrophobic surfaces with a contact angle of nearly 164°.
The researchers used commercial sandpaper to introduce selected powder additives, such as graphene, molybdenum disulphide, Teflon and boron nitride, into the surfaces of materials including Teflon, polypropylene, polystyrene, polyvinyl chloride and polydimethylsiloxane. The sandpaper was made from aluminium oxide with grits of between 180 and 2000.
Tribofilm formation
“During the sand-in process, the introduction of powder between the rubbing surfaces facilitates the formation of a tribofilm,” explains Tour. “A tribofilm forms in a chemical reaction on surfaces sliding against each other and functionalizes the surface to repel water even more.”
“The sanding also induces structural changes and mass and electron transfer to lower the surface energy of the substrates,” adds Higgs.
A wide range of surfaces can be made superhydrophobic in minutes, Tour tells Physics World. This highlights the broad range of potential applications of the sanded surfaces.
“Aeroplane manufacturers do not want ice forming on their wings, ship captains do not want drag from attached ocean microbes slowing them down and biomedical devices need to avoid biofouling, where bacteria build up on wet surfaces,” says Higgs. “Robust, long-lasting superhydrophobic surfaces produced from this one-step, sand-in method can alleviate many of these problems.”
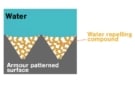
Superhydrophobic surfaces toughen up
Higgs notes that other techniques used to generate hydrophobic surfaces cannot scale up to large surface areas, such as those on planes and ships. “Simple application techniques like the one developed here should be scalable,” he says.
Robust superhydrophobicity
The superhydrophobic materials are extremely robust. Indeed, they remained water-repellent even after 100 sticky tape peeling tests and after being exposed to 130°C in air for 24 hr. Leaving them out in the hot Texan sun for 18 months did not affect their properties either. And when the materials do begin to fail, they can be easily refreshed by simply sanding them again with the same powder additives.
The Rice researchers are now looking to apply their sand-in technique to another type of substrate altogether – the metal surfaces used to make rechargeable batteries. Indeed, they recently reported tests on lithium and sodium foils. “The role of the tribofilm here was to regulate the incoming ion flow in the battery electrolyte to improve the metal deposition/stripping behaviour during the battery cycling,” explains Tour.
The researchers describe their work in ACS Applied Materials.