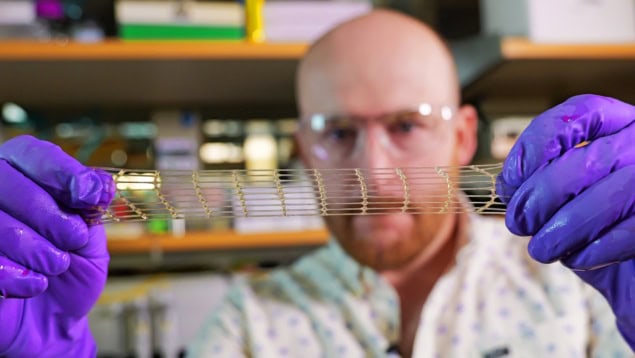
A new method for 3D printing, described in Science, makes inroads into hydrogel-based adhesives for use in medicine.
3D printers, which deposit individual layers of a variety of materials, enable researchers to create complex shapes and structures. Medical applications often require strong and stretchable biomaterials that also stick to moving tissues, such as the beating human heart or tough cartilage covering the surfaces of bones at a joint.
Many researchers are pursuing 3D printed tissues, organs and implants created using biomaterials called hydrogels, which are made from networks of crosslinked polymer chains. While significant progress has been made in the field of fabricated hydrogels, traditional 3D printed hydrogels may break when stretched or crack under pressure. Others are too stiff to sculpt around deformable tissues.
Researchers at the University of Colorado Boulder, in collaboration with the University of Pennsylvania and the National Institutes of Standards and Technology (NIST), realized that they could incorporate intertwined chains of molecules to make 3D printed hydrogels stronger and more elastic – and possibly even allow them to stick to wet tissue. The method, known as CLEAR, sets an object’s shape using spatial light illumination (photopolymerization) while a complementary redox reaction (dark polymerization) gradually yields a high concentration of entangled polymer chains.
To their knowledge, the researchers say, this is the first time that light and dark polymerization have been combined simultaneously to enhance the properties of biomaterials fabricated using digital light processing methods. No special equipment is needed – CLEAR relies on conventional fabrication methods, with some tweaks in processing.
“This was developed by a graduate student in my group, Abhishek Dhand, and research associate Matt Davidson, who were looking at the literature on entangled polymer networks. In most of these cases, the entangled networks that form hydrogels with high levels of certain material properties…are made with very slow reactions,” explains Jason Burdick from CU-Boulder’s BioFrontiers Institute. “This is not compatible with [digital light processing], where each layer is reacted through short periods of light. The combination of the traditional [digital light processing] with light and the slow redox dark polymerization overcomes this.”
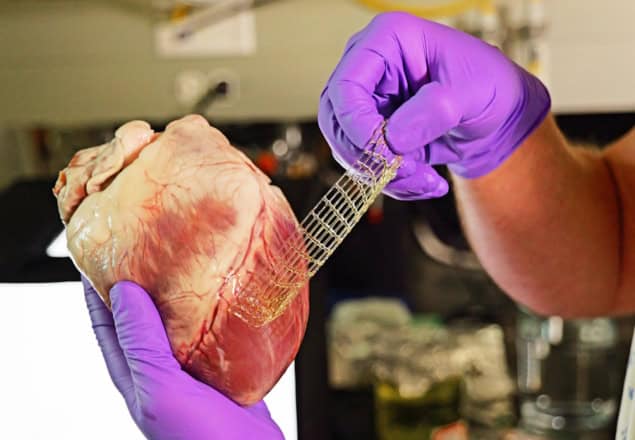
Experiments confirmed that hydrogels produced with CLEAR were fourfold to sevenfold tougher than hydrogels produced with conventional digital light processing methods for 3D printing. The CLEAR-fabricated hydrogels also conformed and stuck to animal tissues and organs.
“We illustrated in the paper the application of hydrogels printed with CLEAR as tissue adhesives, as others had previously defined material toughness as an important material property in adhesives. Through CLEAR, we can then process these adhesives into any structures, such as porous lattices or introduce spatial adhesion that may be of interest for biomedical applications,” Burdick says. “What is also interesting is that CLEAR can be used with other types of materials, such as elastomers, and we believe that it can be used across broad manufacturing methods.”
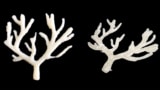
Ultrasound-activated sono-inks could print 3D structures inside the human body
CLEAR could also have environmentally friendly implications for manufacturing and research, the researchers suggest, by eliminating the need for additional light or heat energy to harden parts. The researchers have filed for a provisional patent and will be conducting additional studies to better understand how tissues react to the printed hydrogels.
“Our work so far was mainly proof-of-concept of the method and showing a range of applications,” says Burdick. “The next step is to identify those applications where CLEAR can make an impact and then further explore those topics, whether this is specific to biomedicine or more broadly beyond this.”