Creating dark materials that prevent reflections has become hot competition recently, with Guinness World Records having to keep revising the darkest substance yet created. But depending on who’s asking, the best black may not be the blackest black, as Jon Cartwright discovers
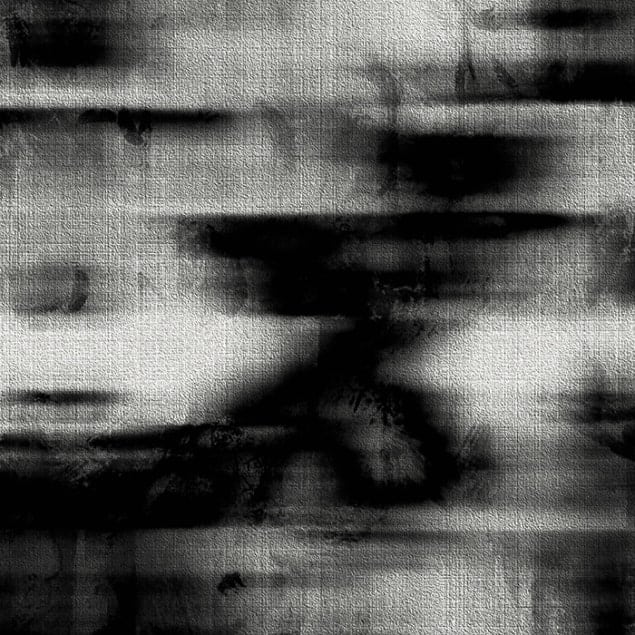
For domestic use, options abound. Pitch black, jack black, lamp black, fine black, velour black, onyx black, blackboard black, black fossil, charcoal, soot, smoke, sinner, black stillness, off black, little black dress, penny black, deep black and – should you want to be left in no doubt – black black.
There are probably 50 shades of black, if not more. But sometimes, and especially where physicists are concerned, even the blackest black isn’t black enough.
For many years, NASA has used a black paint manufactured by the international aerospace corporation Lord that has a reflectivity of just 3.5%. That’s several per cent lower than conventional black pigments. Dubbed Z306, it was applied to the Hubble Space Telescope, as well as other NASA instruments, to reduce stray light from the Sun, Moon, Earth and indeed the telescope’s own housing. Without it, all those images of distant galaxies and novae might not have appeared quite so spectacular.
Black is important in the design of the best telescopes, but it is also key in other scientific equipment, including infrared detectors, black-body calibrating materials, radiators and solar panels. The military, too, requires very black materials for sensitive infrared seekers used in ballistic missile defence and satellite surveillance, because the blacker the surface, the more sensitive it is to light. With such high-stakes applications, it is no wonder that the fashion for black is being eagerly updated. After all, Z306 is so last season. Enter the new black: super black.
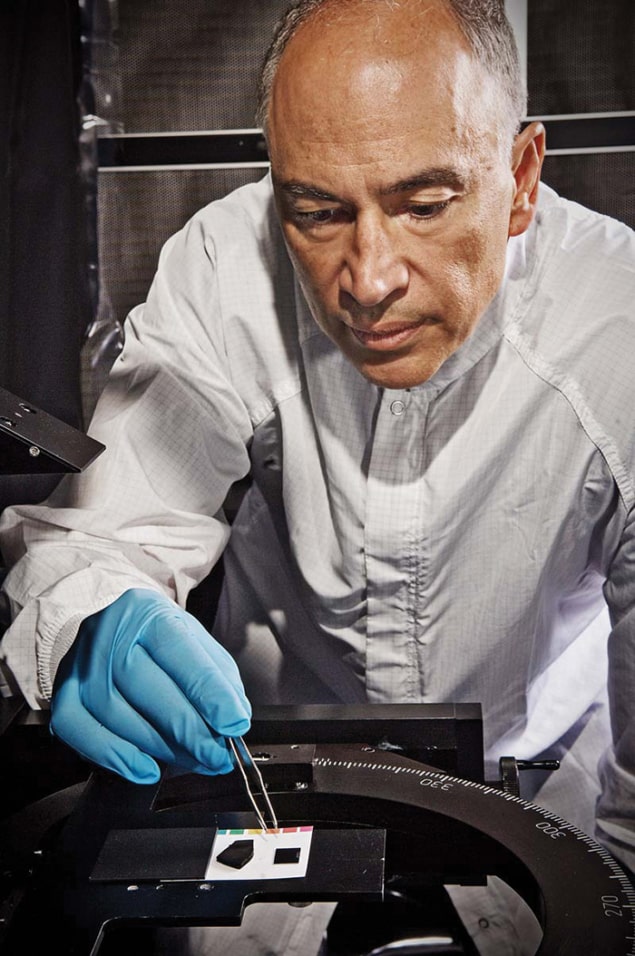
As it happens, NASA has been working on a super black for some time. In 2007 physicist John Hagopian from the agency’s Goddard Space Flight Center in Maryland, US, began experimenting with the growth of carbon nanotubes. These materials share the same hexagonal “chicken wire” structure of the layers in graphite, but are rolled up into tiny hollow cylinders with diameters ranging from fractions of a nanometre to hundreds of nanometres. Carbon nanotubes are typically grown on a substrate inside a furnace, into which a carbon-containing gas is fed. What Hagopian did was to coat a silicon substrate with iron, which acted as a catalyst, encouraging the nanotubes to grow vertically, like a forest.
Hagopian’s nanotube forests had a refractive index close to one – that of air – which meant that light striking the surface didn’t “see” a barrier. Rather than reflect, the light was absorbed by the nanotubes’ hollow interiors, and ultimately turned into heat. The material had a reflectivity of just 0.5%, making it seven times blacker than Z306.
That is very black. Look around and you will probably see several black surfaces – on computers, smartphones and televisions. Black is the designer’s go-to chic colour when it comes to consumer technologies. But this familiar black, it turns out, is hardly black at all compared with the carbon-nanotube variety. Hagopian’s coating was so black in fact that it attracted interest from a Belgian artist, Frederik De Wilde, who quickly persuaded the NASA group to allow him to use it on some of his projects. One of them, the 2010 work Hostage, is a square nanotube forest on a conventionally black background. It looks like a mysterious void: no reflections, no features to speak of.
Dark rivalry
A coating that absorbs all but 0.5% of light is surely black enough, you might say. But even while Hagopian’s group was writing up a paper on its super-black nanotube forests in 2008, another group, based at the Rensselaer Polytechnic Institute (RPI) in New York, US, announced that it had made “the darkest material ever made by man”. That material, too, was a carbon-nanotube forest, albeit with a density even better tuned to minimize reflectance. “This is the kind of field where everyone feeds off everyone else,” says Hagopian. “There’s a lot of history, a huge number of papers.”
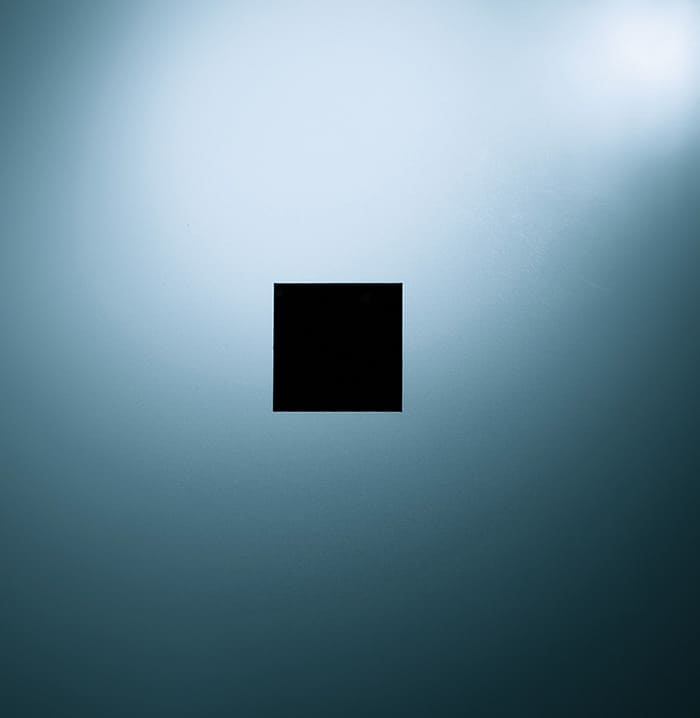
The RPI group, led by physicist Shawn-Yu Lin, claimed a visible-light reflectance for its nanotube forest of 0.045%, making the material more than 10 times blacker than Hagopian’s, and nearly 80 times blacker than Z306 (Nano Lett. 8 446). The material swiftly became the blackest black, as recognized by the book Guinness World Records.
For a few years the RPI record seemed unbreakable. During this time, however, Ben Jensen and others at Surrey NanoSystems, a company in Newhaven, UK, had been experimenting with the growth of carbon nanotubes at relatively low temperatures to make highly conductive electrical contacts. The problem is that carbon nanotubes do not normally grow below a temperature of about 700 °C, which is above the melting temperature of aluminium, one of the most widely used metals in aerospace. To make the two materials compatible, Jensen’s group realized that it could keep the bottom of an aluminium substrate cool while locally heating the top surface with a high-powered lamp. That way, the nanotubes could grow without any disruption to the bulk metal.
In 2012 the idea caught the attention of Theo Theocharous at the National Physical Laboratory (NPL) in Teddington, UK, who immediately realized its potential for creating super-black surfaces for space applications. The result, after two years’ collaboration between NPL and Surrey NanoSystems, was “Vantablack” – the “vanta” prefix being an acronym of “vertically aligned nanotube arrays” (Opt. Express 22 7290). Although the paper emphasized the importance of the aluminium substrate, the firm’s press releases stressed Vantablack’s claimed minimum reflectivity in the visible spectrum of 0.04%, later revised to 0.035%. The improvement over the RPI material may have been slight, but in due course Guinness World Records made it official: Vantablack was the new black.
Here is where the rivalry for the blackest black has shown its dark side. After Surrey NanoSystems’ 2014 announcement, lawyers acting on behalf of De Wilde reportedly contacted Dazed, a UK fashion and culture magazine, to contradict its description of Vantablack as “the world’s blackest material”. “Nobody likes to be left out and disrespected,” the artist said in a subsequent interview with the same magazine. “Unfortunately I cannot talk in detail yet about my relationship with Surrey NanoSystems…The only thing I can say is that Surrey NanoSystems contacted me and we exchanged information.”
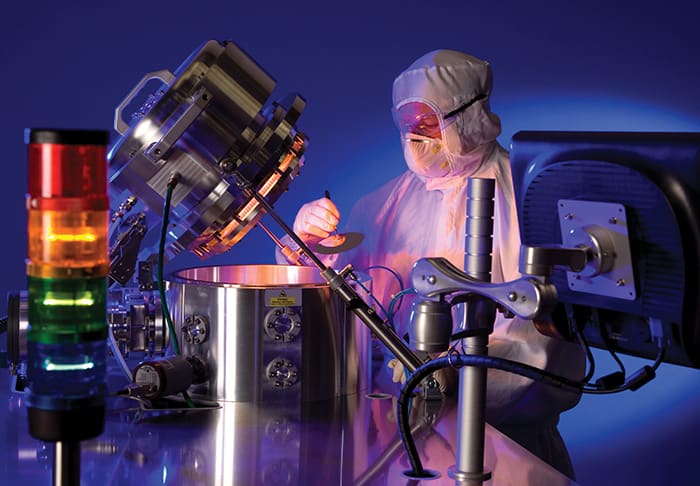
De Wilde did not respond to questions from Physics World about the reasons behind his contention. Jensen from Surrey NanoSystems, however, says that the artist had approached his firm with a proposal of artistic collaboration, but it had to refuse because it had already signed a separate exclusive agreement with the British-Indian Turner Prize-winning sculptor Anish Kapoor. In any case, Jensen adds, De Wilde’s claim is plain wrong: Vantablack was, and still is, the blackest black. “It’s just bad cheese because we refused to work with him,” he says.
Back at NASA, Hagopian tries to distance himself from the claims of his artist collaborator. “There’s a little battle going on – who can be the darkest,” he says. “We’re kind of foregoing that, and working on practical applications.” Still, Hagopian does not bow out of the competition altogether. “You know, the difference between RPI and Surrey NanoSystems – what is that, about 0.01%? It’s not that great. I’m sure we could do better, it’s just not what we’re trying to optimize.” In recent tests, he claims, the visible-light reflectivity of his nanotube forests has dropped below 0.1%.
Space, shock waves and solar power
Rather than creating blackness for blackness’ sake, much of Hagopian’s work has had the practical focus of applying the nanotube forests to substrates suited to aerospace. By using a patented aluminium-oxide buffer layer, his group has managed to grow nanotubes on stainless steel, titanium, copper, silicon and silicon nitride. He admits that the ability to deposit Vantablack on aluminium is interesting, but doubts how much it would be used in practice. “I think their systems are quite expensive, half a million dollars or so, versus a tube furnace that costs maybe ten thousand,” he says. “We didn’t really find it to be cost effective for what we’re doing. Titanium, the stainless steels – they’re just as good as aluminium.”
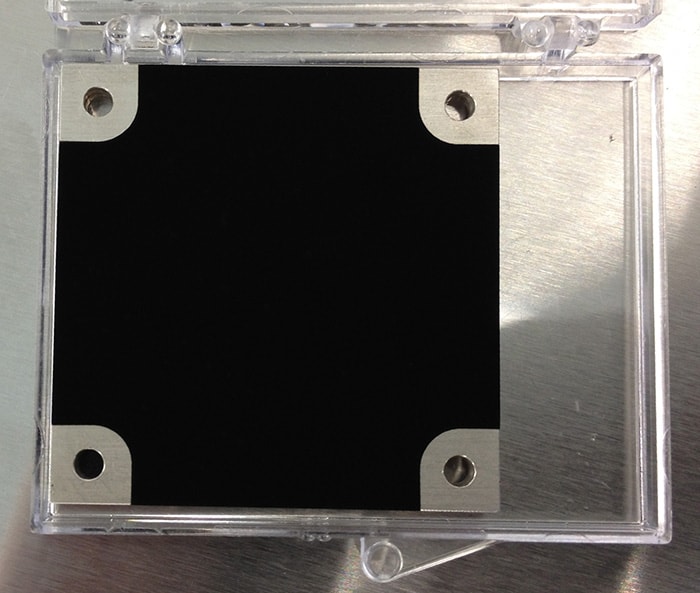
Most scientists seem to agree that when it comes to space applications, a super black’s minimum reflectivity in the visible spectrum is somewhat incidental: low reflectivity across the entire infrared, visible and ultraviolet spectrum is more important. Even then, there are other concerns, such as the material’s mass and its tolerance to extreme conditions. Hagopian points out, though, that his nanotube forests have already been tested for durability aboard the International Space Station, being exposed to the harsh radiation of outer space. Elsewhere they are being used to boost the signal-to-noise ratio of an airborne laser fluorescence experiment, tracking gases used to monitor atmospheric currents. His group has also applied its super black to an occulter used to block out starlight in exoplanet hunting, as well as to diffraction baffles for the upcoming LISA gravitational-wave experiment.
Not that the main destination for super blacks is necessarily space. In 2012 Jay Guo, an engineer at the University of Michigan in Ann Arbor, US, and colleagues reported that nanotubes could be coated with polymers onto a concave lens. When irradiated with a laser, the coating quickly transformed the light to heat, generating ultrasonic shock waves that could destroy materials placed in the lens’s focal zone (Sci. Rep. 2 989). The lens, says Guo, could become an “invisible scalpel” for use in surgery.
Working with researchers at Zhejiang University in China, Guo’s group is also planning to report on an entirely new way to make a super black. Although he cannot yet give details, Guo claims that simple evaporation of materials can produce a multi-layered structure that has a reflectivity of 1% from the visible to near-infrared. This is not nearly as low as other super blacks, but he reckons that the technique can be scaled more easily to large areas.
Guo isn’t the only one to highlight scalability as another important factor. Renkun Chen – an engineer at the University of California in San Diego, US – is interested in applying super blacks to the sunlight-absorbing tubes used in concentrated solar power plants. In these plants, a field of mirrors concentrates sunlight onto a central tower containing tubes, which heat up gas to drive turbines. A super-black material made from a carbon-nanotube forest – and especially the painstaking method needed to create one – would simply not be up to this task, he says. “For a solar tower you need hundreds of tubes,” he explains. “Each tube is about 20 m long. Think about it.”
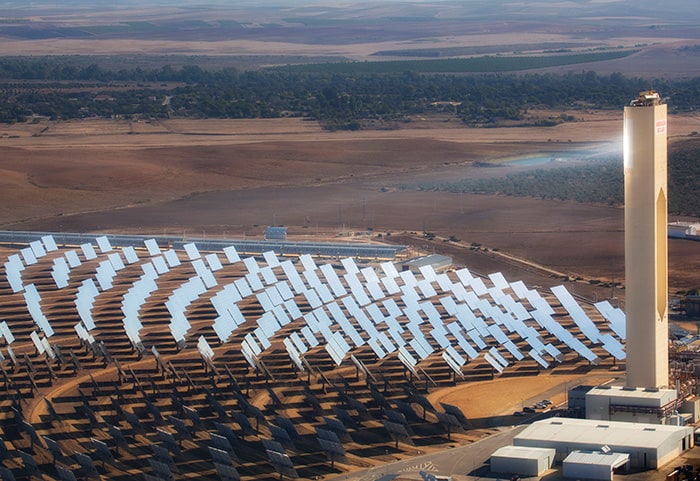
Even if super blacks made from nanotubes were coated onto such tubes, says Chen, they would burn up in the heat of a solar tower. Current solar towers can reach temperatures of about 600 °C, but engineers want to push them even higher to improve efficiency and to make the technology competitive with solar photovoltaics. To meet this challenge, Chen and his colleagues are now developing a super black consisting of cobalt-oxide nanoparticles that can be sprayed onto the absorber tubes. Stable up to 750 °C, the nanoparticles create a rough surface that absorbs light in much the same way as a nanotube forest, although the reflectivity reaches a minimum of only 2% (Sol. Energ. Mat. Sol. Cells. 134 417).
With this development, the hunt for super blacks has gone full circle. Chen’s super black is, in essence, a spray paint. But that is not to say that growing carbon nanotubes, or depositing materials by evaporation, is the wrong approach. It only means that there are other criteria to consider. Depending on who’s asking, the best black may not be the blackest black.
Hiding in the shadows
The search for super blacks could, in time, turn up ideas that bear fruit in other areas. In one 2011 experiment, Guo found that if he coated a micron-scale 3D etching of a military tank with a nanotube forest, the tank became perfectly camouflaged against its surroundings: it appeared as flat and as black as the surface it was etched upon (Appl. Phys. Lett. 99 211103). The military applications were obvious. But the result also got him thinking: what if objects in outer space were hidden in this way? In principle, he concluded, a super-black coating could hide an arbitrarily large object from the ultraviolet through the infrared and into the terahertz part of the electromagnetic spectrum.
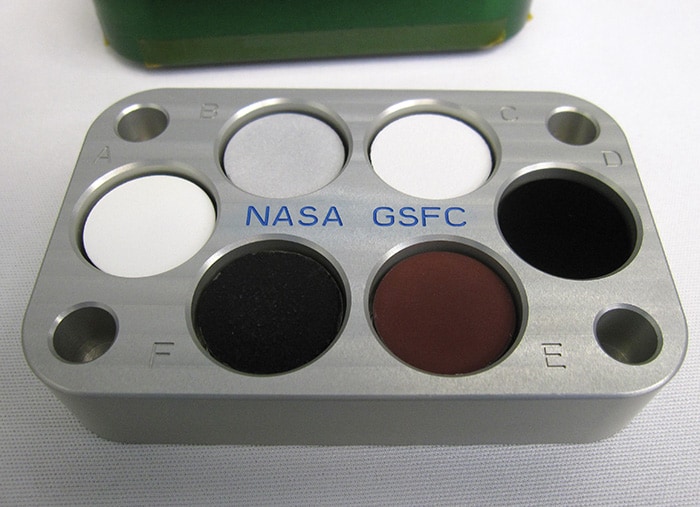
“It is interesting to note that deep space itself is a perfect background without reflecting any radiations,” he wrote in his paper. “It would only take a ‘magic veil’ consisting of low density and broadband absorbing particles to render matters and objects totally invisible to our instruments based on the detection of electromagnetic waves.”
Perhaps, then, the allure of super blacks is rather more primitive than many scientists let on. It is that ultimate uncertainty, the one that has tormented every human who has ever stared into the void. Is there something there, or not?