Delegates at a recent Big Science Summit in Malmö, Sweden, discussed how best to boost the economic impact of Europe’s research facilities. Joe McEntee reports
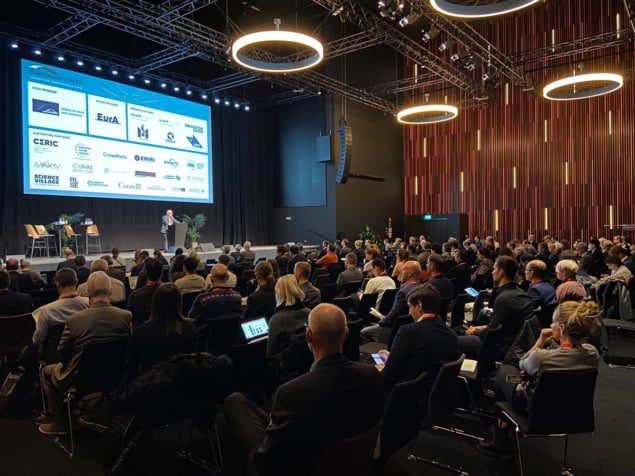
How can Europe’s large-scale research facilities better engage with the industrial R&D community? That was the central question preoccupying delegates attending the Big Science Summit held in Malmö, Sweden, in November 2021, which featured talks and workshops within the broader TechConnect Europe Innovation Conference and Expo. The summit brought together applied scientists and engineers working on emerging technologies with industry experts from Europe’s top-tier laboratories such as the European Spallation Source (ESS) in Lund, Sweden, the Institut Laue-Langevin (ILL) in Grenoble, France, and DESY in Hamburg, Germany.
One of the headline themes addressed at the meeting was how to lower the barriers so that small and medium-sized businesses, as well as established technology companies, see Europe’s large-scale research facilities as a natural extension of their own R&D and innovation efforts. “There’s work to do on both sides,” Dalia Yablon, senior adviser and technical programme chair of the TechConnect conference, told Physics World. “The big science labs, for their part, need to reduce obstacles to access in terms of bureaucracy, cost and the current low success rate for proposals received from industry.”
Yablon believes that a phased approach to collaboration makes sense, where an industry customer might be able to start with a “quickie proof-of-concept” – minimal contracts and expense – followed by deeper levels of engagement as confidence builds between the two partners. “Equally,” she adds, “the big labs must be willing to do some ‘hand-holding’ along the way, especially with smaller companies that are likely to need their in-house expertise when carrying out one-off measurements on a specialist beamline or scientific instrument.”
Yablon also highlights the importance of an “outreach mindset” to enable Europe’s big science labs to build bridges with applied researchers and engineers in industry. “It’s hard to know about these exotic techniques or get access to them unless you are ‘in the network’ of X-ray and neutron scientists – either through your graduate research or via colleagues,” says Yablon. “That network needs to be expanded as a matter of priority.”
So-called “mediator companies” are crucial in this regard, helping to plan, execute and deliver high-end materials characterization services for industrial problem-solving. One such firm is Finden, which is based at the Harwell Innovation Campus in Oxfordshire, UK, and is part of a specialist network of analytical service providers called Mediators Connecting Industry to X-rays and Neutrons (MiXN). Finden and its MiXN peers help customers in a range of industries – pharmaceuticals, energy, catalysis and automotive, among others – to access Europe’s synchrotron and neutron research laboratories. “As a regular user of large-scale science facilities, we enable our industry customers to fast-track R&D projects through unique measurement capabilities tailored to their needs,” says Simon Jacques, managing director of Finden.
The industry perspective
While many speakers pushed for an “enhanced and shared understanding” between big science and industry, others noted that significant progress is already being made. The Danish advanced materials company CTS Ceramics, for example, offered a case study in what’s called “upstream innovation”. Since 2014 it has been collaborating with the CERN particle-physics laboratory near Geneva to co-develop a custom line of piezoelectric actuators. “As a result of this innovation partnership, CTS is now a preferred supplier and selling its technology solution to CERN,” notes Nikolaj Zangenberg, work package leader for the European Network for Research Infrastructures and Industry for Collaboration (ENRIITC) and innovation manager at the Danish Technological Institute.
Since its formation in January 2020, ENRIITC has emerged as something of an engine-room for collaboration between large-scale science facilities and industry. With nearly 400 network members – including more than 80 industry experts from Europe’s big science labs and the university research sector – ENRIITC’s goal is to accelerate the societal and economic impact of federal and pan-European research programmes. “Our members work together to map industry as a supplier and a user of Europe’s large-scale research infrastructures,” adds Anne-Charlotte Joubert, ENRIITC project co-ordinator and a grants officer at the ESS.
Zangenberg and Joubert showcased a notable example of “downstream innovation” involving French green-tech start-up Carbios, which is aiming to improve recycling treatments for poly(ethylene terephthalate) (PET) – the most abundant polyester plastic with almost 70 million tonnes manufactured annually worldwide for use in bottles, textiles and food containers. The Carbios R&D team used beamlines at several synchrotrons in Europe to resolve and screen the structures of hundreds of protein crystals. This group was able to zero in on a novel enzyme that biologically depolymerizes PET plastic waste by increasing the degradation yield to 90% in 10 hours – a significant enhancement versus the previous best-case yield of 1% after several weeks.
Clearing hurdles
Whether it’s upstream or downstream innovation, the key to closing the gap between big science and industry is an appreciation of the unique constraints faced by scientists and engineers operating in the commercial sector. “Walk a mile in your customer’s shoes and you will better understand how to reach out and engage with them,” says Jimmy Binderup Andersen, an ESS senior strategy officer. Time, or more precisely the lack of it, is probably the single biggest issue facing industry customers thinking about accessing a large-scale research facility. If a company is experiencing problems with an early-stage technology, for example, a solution might be needed in days or a couple of weeks, as opposed to the multi-year timeframes that academic scientists are accustomed to for their research projects.
The key to closing the gap between big science and industry is an appreciation of the unique constraints faced by scientists and engineers operating in the commercial sector
Management buy-in is another hurdle for industry scientists, not least when budget holders, often with little technical background, are confronted with a significant one-off spend plus non-trivial contract paperwork. Again, a very different environment to university and government research, where the approval process is less onerous and often managed by staff who are close to the science. “The low success rate for beamline proposals from industry sources is another barrier just now,” explains Yablon. “After all, if you get management buy-in and your proposal is rejected, you will probably not get buy-in to try a second time.” The rise and rise of ‘new big science’
A simple three-point plan can help large-scale facilities better engage with industry, argues Caroline Boudou, an industry contact officer at the ILL. “There’s a need for a dedicated selection path,” she adds, “with appropriate criteria to give industry streamlined access and to grow collaborative industrial R&D activity.” Improved tracking – and subsequent promotion – of outcomes is another priority, with impact evaluated not just on a financial basis, but acknowledging other metrics such as savings versus energy and raw materials. “Finally,” she says, “we need dedicated industry support staff and beamtime for our scientific instruments, along with closer connections to the ‘intermediary’ companies.”
- The TechConnect World Innovation Conference and Expo will be held in Washington, DC on 13–15 June 2022