For quantum technologies to fulfil their promise, the systems that support them need to shrink. Laurence Coles explains how advances in additive manufacturing are bringing miniaturization within reach and heralding a wider revolution in vacuum system design
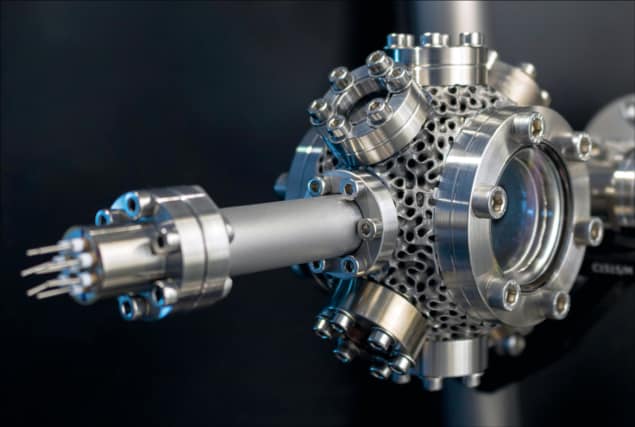
If quantum technologies came with instruction manuals, the first few pages would describe how to cool and trap a sample of atoms. Clouds of cold, trapped atoms lie at the heart of present-day quantum devices such as atomic clocks. They’re also integral to several possible future ones, such as the “quantum positioning systems” that may one day replace satellite-based GPS. The reason is simple: it is only by isolating atoms from their environment and cooling them down, sometimes to temperatures as low as a fraction of a degree above absolute zero, that their quantum characteristics come to the fore. Properties such as the atoms’ acceleration and rotation, the timing and frequency of transitions between energy levels, and even their response to disturbances in electric, magnetic and gravitational fields can and will be exploited as part of the next generation of quantum technologies.
Forming and sustaining clouds of cold atoms is, however, anything but simple. Among other requirements, the clouds must be kept in an ultrahigh-vacuum (UHV) environment, at pressures below 10–7 pascals (10–9 mbar). This ensures that atoms cooled to microkelvin temperatures are not lost from the trap due to collisions with warmer particles in the atmosphere. UHV assemblies are therefore critical sub-systems for high-precision quantum applications, and to date, they have typically consisted of multiple bulky, standardized stainless-steel components. The large number of vacuum connectors and joints between components increases the risk of leaks, especially when the joints are subjected to temperature changes and mechanical stress. As a result, UHV sub-systems are widely viewed as the limiting factor in getting quantum technologies out of the lab.
Additive manufacturing (AM) has the potential to turn this situation on its head. Unlike traditional manufacturing, in which parts are made subtractively from larger billets of material, additive techniques build components layer-by-layer. One method, known as laser powder bed fusion, works by laying down thin layers of powdered material and subjecting them to an energy source such as a laser, which fuses the layers together. The energy source is then scanned in a pattern determined by the geometry of the component being manufactured. Using this additive technique, it is possible to create complex features such as internal channels and lightweight lattices and then cover them with subsequent layers. AM also makes it possible to consolidate several components into single parts while retaining all the features that would have traditionally required a multi-part assembly.
Additively manufactured vacuum assemblies offer several benefits for quantum technologies applications. As well as replacing bulky off-the-shelf components with UHV sub-systems tailored to the user’s needs, AM also makes it possible to consolidate assemblies, remove vacuum joints, add integrated functionality and reduce the size, weight and power (SWAP) parameters of the whole system. Indeed, in the longer term, AM has the potential to drive a revolution in vacuum system design, introducing new capabilities and integrated features that are only achievable thanks to the freedom of design that AM can offer over traditional manufacturing.
Until recently, the idea of using AM to produce UHV system components was quickly dismissed within the vacuum industry due to fundamental concerns over the porosity and mechanical strength of additively manufactured materials. However, recent developments in the field of AM have pushed process capabilities forward to the point where the densities and mechanical performance of AM materials are now comparable to those of the original bulk materials. Thanks to these advances, it has become feasible to construct metal UHV components via laser powder bed fusion, and therefore to challenge common misconceptions about the place of AM methods within the vacuum industry.
Inspired by various success stories demonstrating that it is possible to use AM components within a UHV environment, my colleagues and I at Added Scientific asked ourselves whether we could produce an additively manufactured vacuum chamber – one that could hold a UHV and deliver the performance required for trapping clouds of cold atoms. Beginning in 2017, our team at Added Scientific collaborated with members of the quantum technologies research groups at the University of Nottingham and the University of Sussex in the UK, harnessing our multidisciplinary expertise to test this idea in a project funded by Innovate UK.
The application of these innovative methodologies, within a seemingly stagnant field, is critical to accelerating the evolution and miniaturization of emerging quantum technologies
As a feasibility study, we decided to construct an AM vacuum chamber for the standard “workhorse” of cold-atom experiments: the magneto-optical trap, or MOT, in which atoms are cooled and held in place with a combination of laser beams and magnetic fields. We designed the prototype chamber to meet all the functional requirements of a MOT, including optical access for three orthogonal pairs of laser beams; space for magnetic coils; a UHV environment; and the ability to connect to standard components such as vacuum pumps. To keep the chamber as lightweight as possible, we refined the geometry of its ports, minimizing the space between them and adding a thin internal skin to complete the walls of the chamber and enable it to hold the UHV. We also maintained the symmetry of the chamber design, ensuring that the ports remain perpendicular to the optical paths of the laser beams, which helps to minimize optical transmission losses.
To add a layer of robustness and increased stiffness to the chamber design, we combined a symmetric internal chamber core with a lightweight structure known in the AM world as a variable density triply periodic minimal surface lattice. The lattice structure took the form of a mathematically defined matrix-based gyroid surface, thickened to form a 3D geometry (see image below). The inclusion of these variable-density lattices allowed us to balance the competing demands of keeping the chamber mechanically stiff and minimizing its mass. The lattice structure also increases the chamber’s external surface area-to-volume ratio, which helps to radiate heat away. The final chamber design consists of multiple ports (2 × CF40 ports and 8 × CF16), making it compatible with standard UHV equipment. Alongside the chamber, we also developed a magnetic coil forming insert with built-in water-cooling channels, to explore the additional benefits AM can offer.
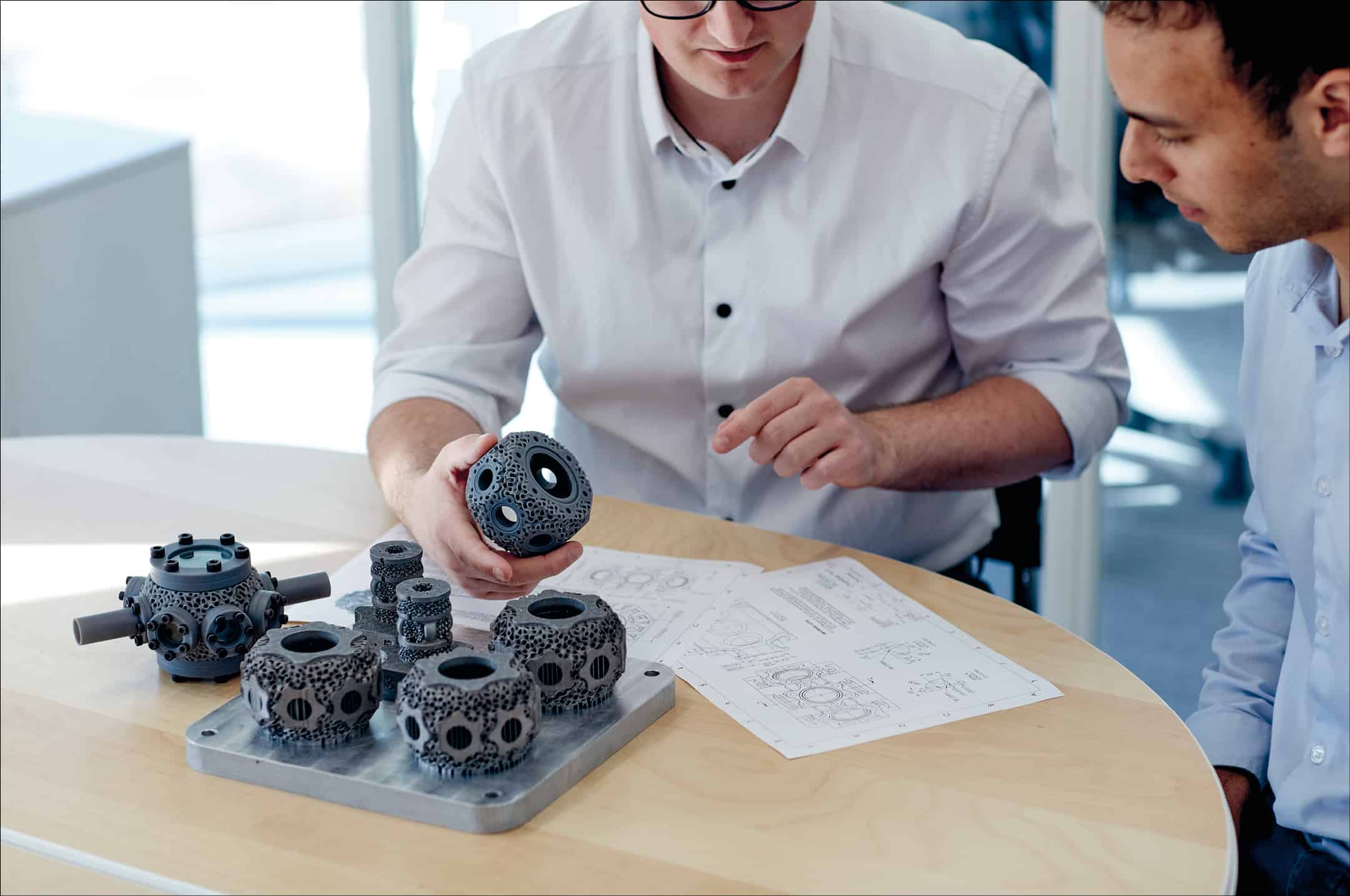
Reasons for success
We chose to build the AM vacuum chamber out of an aluminium alloy, AlSi10Mg, due to its high specific strength and low density. Materials produced by laser powder bed fusion have a characteristic ultrafine grain structure in which the grains grow up through the layers as the component is built. After the build is complete, heat treatments are typically applied to alter the material’s mechanical performance by homogenizing the grain microstructure and controlling the size of the grains, while relieving residual stresses built up due to the AM build process. For our application, we also applied a separate “ageing” heat treatment to promote the growth of precipitates at the grain boundaries. This increased the material’s strength until it was hard enough for us to use the same knife-edge sealing techniques associated with standard vacuum components.
Traditionally manufactured UHV components have a machined and polished internal surface finish. In contrast, AM metals tend to have rough surfaces. This roughness is usually regarded as a black mark against AM for UHV applications, because the increased surface area was commonly thought to increase the likelihood of outgassing. To determine whether the additively manufactured components would be suitable for UHV, we conducted X-ray photoelectron spectroscopy and a mass spectrometric study on the AM alloy. The results indicated that a protective magnesium-rich oxide layer forms on the surface of the material, and that this layer plays an important role in suppressing the outgassing that might otherwise inhibit the alloy’s performance in vacuum applications. Other than the expected (and unavoidable) atmospheric species seen within the mass spectrometric data, we did not observe any other spectroscopic peaks until the temperature exceeded 400 °C. At this point, magnesium peaks from the layer itself started to appear, but this still gives us a wide range of acceptable operating temperatures, even without optimizing the material and protective layer further.
To assess the vacuum performance of the AM chamber, we mounted off-the-shelf stainless-steel viewports and components to it using standard knife-edge-sealing CF flanges, creating a complete vacuum assembly. We then pumped and baked out (that is, heated) the system at 120 °C for a period of 120 hours. Once baked, the UHV was sustained using a combined ion/non-evaporable getter (NEG) pump, achieving a final pressure of < 10–10 mbar – well within the UHV range. We then tested the system further by transporting it from Nottingham to the National Quantum Technologies Showcase event in London, which meant that it was without external power or active pumping for 48 hours. During this period, with only passive NEG pumping in place, the pressure rose, but only to 10–7 pascals (10–9 mbar) – still plenty low enough for cold rubidium atoms to be captured and retained in a MOT.
The start of something smaller?
This is the first time an AM chamber has been demonstrated to hold UHV, and for quantum technology applications, the advantages are clear. The change in material, together with the lightweight, AM-optimized design, meant that the mass of our prototype MOT chamber is 245 g – 70% less than that of a commercially available stainless-steel equivalent. This represents a considerable saving of precious lab space for research groups, as well as an important step towards portability in future devices. In principle, we could make the chamber even smaller, since the minimum size of a MOT is set by the diameter of the orthogonal laser beams that enter its windows and provide its optical trapping element (approximately 15 mm in diameter for the team’s particular test case). We were prevented from doing so at this stage by the need to integrate the AM chamber with existing, off-the-shelf vacuum components, but if this limitation were removed, and components of the wider vacuum system were included in future design iterations, we should be able to reduce the SWAP parameters further still.
So far, quantum physics is one of the few fields where customers are really pushing for smaller UHV systems. This makes projects like the additively manufactured MOT chamber a perfect testbed for AM within the vacuum industry. The application of these innovative methodologies, within a seemingly stagnant field, is critical to accelerating the evolution and miniaturization of emerging quantum technologies, and onward to moving them out of the laboratory and into everyday life. With the desire for quantum technologies and therefore the associated market maturing rapidly, the development of this capability will significantly support the UK’s National Quantum Technologies Programme and the government’s commitment to developing a quantum technology industry in the UK.
That said, the flexibility that AM provides in terms of design freedom, part consolidation and added functionality suggests that there are now exciting opportunities to make wider and more significant changes in how we approach vacuum system design. AM makes it possible to realize truly bespoke designs that are optimized for system performance, and not limited by traditional manufacturing capabilities. Using lattice structures and other complex geometries (as we did for this prototype) enables designers to further reduce the mass of common components while maintaining their structural integrity and stability. AM also offers the potential to enhance the performance of vacuum components in other ways by making structures such as integrated, conformal fluidic channels, internal coil mounts, diaphragms and so on an integral part of the component, rather than something that needs to be assembled from multiple components. In summary, the introduction of AM techniques to vacuum system development has the potential to impact not only portable quantum technology applications, but also the wider scientific and industrial community.
- This article was amended on 15 August 2019 to include the project’s source of funding.