Fusion doesn’t need billions of euros – at least that is what venture capitalists claim. Jon Cartwright takes a look
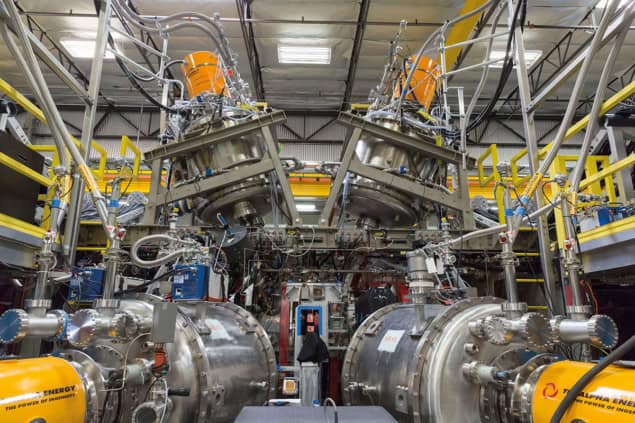
Fusion is just 20 years away, and always will be. Those who work on publicly funded fusion must be tired of hearing this well-worn joke, but it is not without an element of truth. After all, 2016 is the year in which ITER – the world’s first “more energy out than in” fusion reactor that is currently being built in France – was originally scheduled to begin operations, by confining its first plasma. ITER’s current schedule predicts that operations will actually begin in the mid-2020s – nearly 20 years after the facility was officially given the go-ahead – but that could yet be further delayed. The estimated cost, too, has tripled from around ¤5bn ($5.5bn) to ¤15bn.
ITER will be big because physics says it must be big: as a reactor grows, you get more output power from a given input power. At least, that is the conventional view. In January last year, however, physicist Alan Costly and others at the company Tokamak Energy in Abingdon, UK, published a paper claiming that the fusion-power gain depends only weakly on reactor size (Nucl. Fusion 55 033001). The paper, which has been downloaded more than 12,000 times, implies that gargantuan projects such as ITER are not the only route to fusion power. “The basic message is that smaller, lower-cost pilot plants and reactors may be feasible,” says Tokamak Energy’s chief executive, David Kingham.
Indeed, smaller and cheaper fusion plants are on the rise, but not in the public sphere. Tokamak Energy is one of several privately funded companies that have sprung up in recent years, each hoping to demonstrate that fusion does not need billions of euros and thousands of tonnes of metal. It was formed in 2009 by Mikhail Gryaznevich and Alan Sykes, who previously worked down the road from Abingdon at the Culham Centre for Fusion Energy (CCFE) – home to the Joint European Torus (JET), which is currently the world’s largest and most powerful fusion tokamak.
The principal workhorse of fusion research since its invention in the 1950s, the tokamak is a doughnut-shaped enclosure that confines a plasma – that is, the fusion reactants – in a magnetic field. As its name implies, Tokamak Energy is also developing tokamaks, but is focusing on those small enough to fit in rooms rather than aircraft hangers, and using more of a spherical (“cored apple”) shape rather than a doughnut design, like ITER.
A smaller footprint means the magnetic confinement is more important than ever, and for this reason Tokamak Energy is employing the latest high-temperature superconductors for its magnets. ITER, in contrast, is destined to rely on conventional superconducting magnets. Tokamak Energy’s current model, the 50 cm-wide ST25 HTC, ran its high-temperature superconducting magnets for 29 hours non-stop in July last year – a world first, according to Kingham.
The company has 14 permanent members of staff and, to date, $14m of private investment from sponsors including the manufacturers Oxford Instruments (also based in Abingdon) and the UK’s Institution of Mechanical Engineers. With such modest support, competing with the likes of ITER seems a challenge, yet Kingham says that the firm is not competing at all: where ITER and other publicly funded fusion hopes to proceed via rigorous scientific methodology, Tokamak Energy is proceeding by trial-and-error engineering.
“Build a device, see how it works, measure what you can, build the next device,” Kingham explains. “The outputs are proof-of-principle patents in some cases, rather than primarily scientific papers. We may sacrifice a depth of understanding about the science, but we hope to gain a whole lot of knowledge about how to engineer tokamaks and high-temperature superconducting magnets.”
Different approaches
Tokamak Energy is relatively conventional in opting for tokamak reactors, but this is not true of other private ventures. General Fusion in Burnaby, Canada, was founded in 2002 by plasma physicist and former laser-printer engineer Michel Laberge, and is based on the concept of an enclosed, liquid-metal vortex. Plasma is injected into the centre of the vortex before numerous pistons hammer on the outside of the enclosure, compressing the plasma and – theoretically, at least – sparking a fusion reaction.
It is a bold idea, but one that dates back to the 1970s with a programme called Linus at the US Naval Research Laboratory in Washington, DC. The main problem with Linus, says Laberge, is that the pistons could never strike the enclosure at exactly the same time. With some $100m of private investment, however, he and more than 60 colleagues are trying to solve this timing problem with modern computing systems – as well as demonstrate the various other complex sub-systems required to make this kind of “inertial confinement” fusion work.
Like Kingham, Laberge does not feel in competition with ITER – and, in fact, he believes the scientific approach provides a crucial resource. “All the physics those guys are learning – we want it, we need it,” he says. “Where we don’t quite agree with [ITER], is we don’t believe the standard superconducting tokamak will make a good power plant. In the future, it’s difficult to conceive that this machine will make electricity in a cost-effective way. It’s a fantastic experiment to learn the plasma physics, but as a power plant we think it’s not the way to go.” One of the main problems with ITER, Laberge says, is that the heat and emitted neutrons will melt and deteriorate the tokamak’s walls over time, forcing them to be replaced. “We have a wall that is already liquid,” he points out.
The apparent camaraderie among fusion start-ups even extends to what is considered to be the best-funded private venture: Tri Alpha Energy, based in Orange County, US. With backers including the Microsoft co-founder Paul Allen and Rusnano, a Russian government-owned private-equity company, it is attempting to develop a technology known as a colliding-beam fusion reactor, in which plasma vortices are fired into a cylindrical chamber containing the magnetic field. The geometry is simpler than a tokamak, yet still, in theory, generates closed magnetic-field lines, which are thought to be most effective at confining plasmas and promoting fusion.
There are many approaches to developing fusion-based technology and we can learn from all of them
Michl Binderbauer, Tri Alpha
“There are many approaches to developing fusion-based technology and we can learn from all of them,” says Michl Binderbauer, Tri Alpha’s chief technology officer. “For example, we are benefitting tremendously from the pioneering technology work done by ITER, especially related to the design and fabrication of superconducting magnet systems and its components. There are some advantages to a private company, including speed and flexibility, but we can learn from all approaches.”
In May last year, after 16 years in the business, Tri Alpha reported what it considers a “breakthrough”: a plasma heated to a temperature of 10 million degrees and confined for five milliseconds (Phys. Plasmas 22 056110). But CCFE director Steve Cowley, who is also chief executive officer of the UK Atomic Energy Authority, points out that JET can already reach 250 million degrees for half a second. Moreover, Tri Alpha is aiming to achieve proton–boron fusion – a reaction that is desirable for not generating any damaging neutrons but one that requires temperatures of more than four billion degrees. “I don’t want to pick holes in all of [these private ventures]; you could pick holes in what we’re doing,” says Cowley. “As a scientist, I’m looking for people who have new ideas – ideas we might adopt, or that change the field. And I don’t see any new ideas from these start-ups – yet.”
Cowley repudiates the paper by Costly and colleagues that claims smaller fusion reactors are viable, saying it relies on an empirically derived “confinement enhancement factor”, H. “The broad consensus is that it is difficult to achieve an H above 1,” says Cowley, yet the Tokamak Energy researchers take H to be over 1.5. Cowley is also sceptical of the engineering approach. “The idea that you can do this as Thomas Edison invented the lightbulb is attractive, but not all inventions work that way – especially where every step costs a lot of money,” he says. “Edison would make 50 bulbs, see which worked best, then try again. But if [a prototype] is going to cost millions, or billions, you need science so that you don’t have to build 50, you only need to build a few.”