Engineers could soon have a much better idea of what is going on inside pipelines and industrial reactors thanks to a new flow sensor developed by scientists in Germany. The device is able to distinguish between different substances in a flowing mixture and it could help solve tricky flow problems such as how to move unruly mixtures of oil, gas and water from deep undersea wells to the surface.
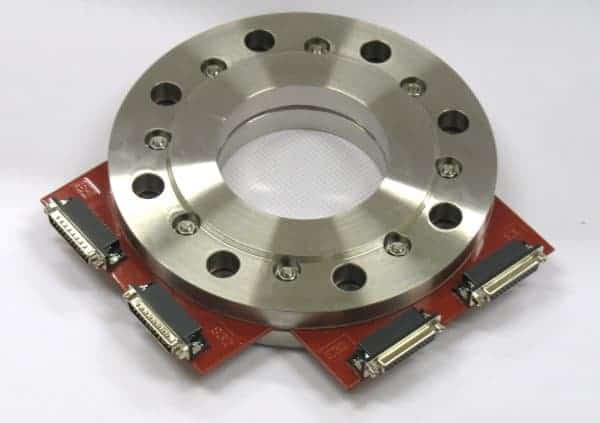
Flowing mixtures of liquids and gases play an important role in the transport and processing of materials as varied as carbonated drinks, pharmaceuticals and petroleum. The complex flow patterns that can occur in such mixtures must be monitored to ensure that, for example, a drug is mixed properly or that oil can flow up through an undersea pipeline.
However, current techniques for measuring such “multiphase” flows have limited efficacy. While a flow can be monitored using high-speed cameras, they provide little quantitative information about the mixture. Probes placed directly in the flow can provide more useful information, but this is limited to the area near to the probe, which is of little use when studying complex multiphase flows. More sophisticated techniques such as gamma-ray tomography can do better, but the added expense and radiation hazards are often not justified by the modest improvement in results.
Now, Uwe Hampel and colleagues at the Forschungszentrum Dresden-Rossendorf (FZD) in Dresden, Germany, have come up with a sensor that promises to change all this. The sensor consists of two planes of parallel wire electrodes stretched across a pipe flange. The planes are perpendicular to each other and separated slightly to form a mesh.
An oscillating voltage is applied to wires in one plane and the resulting electrical fields are detected at the electrodes in the second plane. This allows the sensor to measure the capacitance of materials in the regions where two wires cross.
Different materials have different capacitances, which allow the sensor to differentiate between different phases in the flow. According to Hampel, the measurement can be done very rapidly so that the flow in a typical pipe cross-section can be scanned up to 10,000 times per second at a spatial resolution of 0.5 mm.
“This catches even small bubbles moving at several metres per second through the sensor, giving highly accurate information on the flow structure,” said Hampel. The sensor is similar to an earlier prototype built by the team that measured the electrical conductivity between the wires and therefore could only be used with conducting liquids.
According to multiphase flow expert Barry Azzopardi at the UK’s University of Nottingham, the new sensor shows great promise because it can be used with organic fluids such as petroleum, which are non-conducting.
The sensor will probably never be deployed in a real oil pipeline because it would be destroyed by the solid “pigs” that are sent through the line to clean and inspect the pipe. Instead the sensors could be used on mock pipelines in the lab gain a better understanding of multiphase flow.
The team will be taking the sensor to Nottingham in November, where they will working with Azzopardi to study the flow of gas and oil mixtures in pipelines.
The team now plans to study various complex flows, such as oil-gas transport through pipelines in order to identify a range of applications for the device. “Currently, the sensor exists as a prototype but we hope to think further about commercialization once a broader range of applications have been identified”, said Hampel.