Materials scientist Judith Driscoll of the University of Cambridge, UK, discusses the benefits of collaborating with industrial partners and the trials and attractions of working with complex oxides
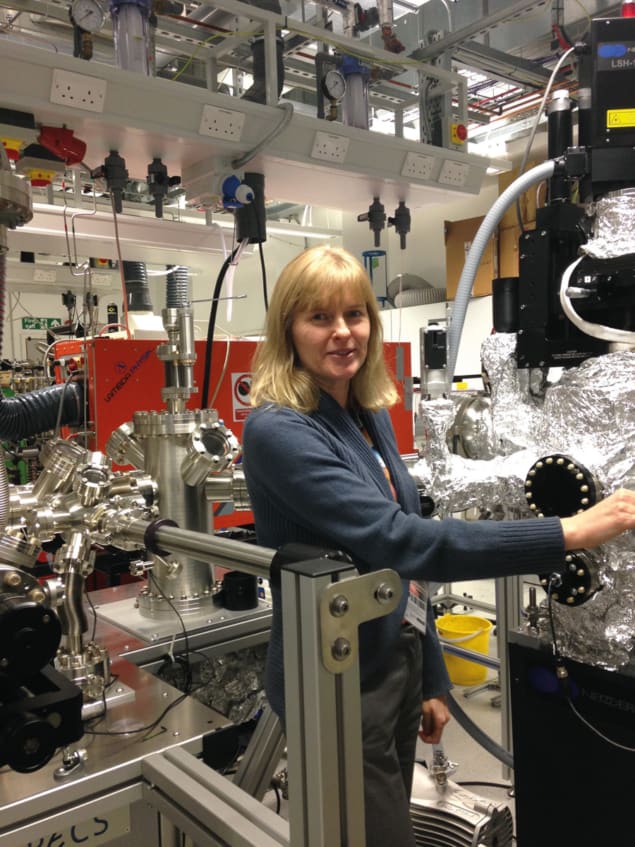
You have collaborated with different companies during your career. How did those relationships develop?
The relationships have developed around my knowledge and expertise in thin-film electronic oxide materials. The longest-standing collaboration arose from my time as a postdoctoral fellow at Stanford University/IBM Almaden in the US. One of my research assistants, Connie Wang, ended up working at Applied Materials, which is a big semiconductor firm, after she got her PhD. I was still vaguely in contact with her when the company started getting interested in superconductors. It identified a market within the electrical grid for superconducting fault current limiters, which are very useful as more renewable energy sources become connected to the grid. It needed some technical help, and since I’d already been working on superconductors for many years and my former student knew that, she contacted me. Applied Materials funded a postdoctoral fellowship for three years and we did some really interesting new science together.
I’ve also worked with several smaller companies and start-ups. For example, there’s a company in Oxford called Tokamak Energy that is trying to make fusion magnets out of high-temperature superconductors, and I have a PhD student who is helping it understand how good its conductors are and how to benchmark them. I’ve also worked with a small company in Wales called Deregallera, which was started by a mechanical engineer with an interest in electric vehicles. Deregallera is building prototypes and is interested in energy-storage materials. It funded a postdoc for a couple of years, and we are now trying to translate a superior new dielectric material that we demonstrated in thin-film form in my lab into a large-volume material in Deregallera’s lab. I also have a long-term collaboration with a Cambridge firm, PragmatIC, that makes flexible electronics for Internet of Things devices. I’m working with PragmatIC to develop p-type oxides that are suitable for CMOS technology in flexible electronics. And I have a more informal connection with Murata, a Japanese corporation that makes electronic components. It is trialling some experiments on a new ferroelectric material in its labs, trying to mimic what we’ve done in my research group, but using a slightly different, more scalable process.
Finally, I work with a South Korean company called SuNAM, which makes superconducting wires based on a process that I demonstrated in 1995. It’s doing really well, and it sponsors a couple of students in my group. I see SuNAM’s researchers three times a year and we have a good relationship – they’re fantastic scientists, very knowledgeable, and they’ve developed all the technology themselves, in-house. We very much appreciate each other’s complementary skills.
Can you say a bit more about the process you developed and how SuNAM adapted it?
Sure. If you make superconducting wires via a thin-film process, it’s very slow. You make a vapour and deposit it inside a vacuum chamber to make a solid film, but you’ve got to get the material perfect and that doesn’t happen quickly. What I showed was that if you put a liquid in the film as well, and you start at a much lower oxygen pressure than you normally would, when you change the oxygen pressure the superconductor will crystallize rapidly. This process is much faster, and during my postdoc at Stanford University/IBM Almaden I demonstrated that in a very simple form, using powders on a silver tape.
After my postdoc, I came back to the UK to take up a faculty position at Imperial College London. However, in parallel with my work, an academic at Stanford, Bob Hammond, started work on the liquid process for thin films, using electron beam evaporation. We kept in close contact over the next 20 years. When I moved to Cambridge, my group used pulsed laser deposition to make the films with liquid in them so as to demonstrate the concept. SuNAM is using the electron beam evaporation process today to make long lengths of commercial, high-temperature superconducting wire.
Most of your work is with oxides, which have applications in many industries. What is it about oxides that makes them so useful?
They have a huge range of electrical properties, all the way from insulating through to superconducting. And they’re stable, which is important; there are lots of interesting, exotic materials out there that show wonderful performance, but they are often not stable over time. The biggest challenge with oxides is their high melting points. For many electronic applications, you need the thin-film form of the material to be perfect, and it’s very hard to make an oxide perfect at a reasonable growth temperature. Typically, thin films are grown at about 700 °C, but that’s way below the melting point of oxides, which can be more than 2000 °C. That means there will be more defects, and the properties of the oxides are sensitive to these defects because the oxides often contain transition metals, which have variable valence states. If you don’t get the oxygen right, you can end up changing the average valence state of the transition-metal ion, which gives the material a whole different performance.
Because of these challenges, the processing must be spot on. This is one reason it took 10 years to develop hafnium dioxide for use in gate dielectrics in transistors.
What are some future applications of more complicated oxides?
Because of their huge variety of properties, they could go almost anywhere, from quantum computing and medical devices to computer memory and data storage. That’s both good and bad. The possibilities are so wide open that it is hard to know which application to focus on. Also, it takes a long time to develop a new material or method before it gets to the point where a company takes it up. This can make patenting things challenging. The university really wants to get an industry partner involved within one or two years of a patent application, and in complex advanced materials that’s always too soon.
What are some other benefits you’ve gained from working with industrial partners?
I think it’s helped to point me in the right direction. One of the things we miss out on in the UK is that we don’t have large industrial research labs that operate between basic science and applications. My first research experience, aged 19, was as a summer student at GEC Hirst Research labs, which was just down the road from my house. I was really impressed by the industrial know-how of the different groups and I loved working there. When you’re an academic working in applied science, but you don’t have labs to connect to that take your research to the next level, you may not know the answers to quite basic questions surrounding the technology being targeted. In some cases, you are working in the dark.
The main focus of university groups is to publish original research, which is as it should be. But it’s much easier to publish nice papers than it is to get something into industry, and if we had some “in-between” research labs, they could test whether the academic results are viable at the next level. It is extremely satisfying to translate science into technology, and I believe this is the ultimate driving force of the research of most applied scientists – or at least, in my opinion, it should be. Having contacts with people in industry research labs helps with that. They know things that you don’t.
Can you give me an example?
Suppose you’re developing a new material for a next-generation memory device. You may have discovered the best material, but you may not know, for example, (a) whether the process you’re using is going to be applicable in industry, (b) what specific performance you need to achieve, or (c) what the timescale will be for refining your process before the next generation of devices comes along. That information isn’t in research papers; your typical academic researchers will put in a nice data plot showing “good performance” without giving details about, say, what temperature the real-world device will be operating at; how large the effect needs to be; or what endurance it needs to have. Or you may be working on a material where the process for making it is so complicated that it’s never going to be practical. In that case, you may have done interesting science and shown a nice effect, but if you keep developing it, no-one is ever going to use it. No-one will care if you keep making marginal improvements. After you’ve done the discovery part and published a few papers, you need to know when it is time to move on to something else. Industry will let you know!
- Enjoy the rest of the 2019 Physics World Focus on Nanotechnology & Nanomaterials in our digital magazine or via the Physics World app for any iOS or Android smartphone or tablet.