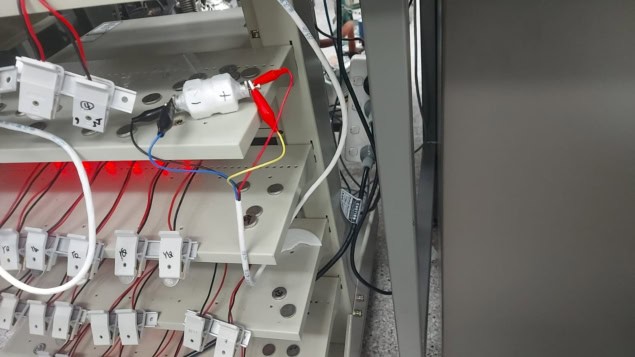
Imagine a smartphone that charges faster, lasts longer and is more eco-friendly – all at a lower cost. Aluminium-ion batteries (AIBs) could make this dream a reality, and scientists are working to unlock their potential as a more abundant, affordable and sustainable alternative to the lithium-ion batteries currently used in mobile devices, electric cars and large-scale energy storage. As part of this effort, Dmitrii A Rakov and colleagues at the University of Queensland, Australia recently overcame a technical hurdle with an AIB component called the solid-electrolyte interphase. Their insights could help AIBs match, or even surpass, the performance of their lithium-ion counterparts.
Like lithium-ion batteries, AIBs contain an anode, a cathode and an electrolyte. This electrolyte carries aluminium ions, which flow between the positively-charged anode and the negatively-charged cathode. During discharge, these ions move from the anode to the cathode, generating energy. Charging the battery reverses the process, with ions returning to the anode to store energy.
The promise and the problem
Sounds simple, right? But when it comes to making AIBs work effectively, this process is far from straightforward.
Aluminium is a promising anode material – it is lightweight and stores a lot of energy for its size, giving it a high energy density. The problem is that AIBs are prone to instabilities as they cycle between charging and discharging. During this cycling, aluminium can deposit unevenly on the anode, forming tree-like structures called dendrites that cause short circuits, leading to battery failure or even safety risks.
Researchers have been tackling these issues for years, trying to figure out how to get aluminium to deposit more evenly and stop dendrites from forming. An emerging focus of this work is something called the solid-electrolyte interphase (SEI). This thin layer of organic and inorganic components forms on the anode as the battery charges, and like the protective seal on a jar of jam, it keeps everything inside fresh and functioning well.
In AIBs, though, the SEI sometimes forms unevenly or breaks, like a seal on a jar that doesn’t close properly. When that happens, the aluminium inside can misbehave, leading to performance issues. To complicate things further, the type of “jam” in the jar – different electrolytes, like chloroaluminate ionic liquids – affects how well this seal forms. Some electrolytes help create a better seal, while others make it harder to keep the aluminium deposits stable.
Cracking the code of aluminium deposition
In their study, which is published in ACS Nano, the Queensland scientists, together with colleagues at the University of Southern Queensland and Oak Ridge National Laboratory in the US, focused on how the aluminium anode interacts with the liquid electrolyte. They found that the formation of the SEI layer is highly dependent on the current running through the battery and the type of counter electrode (the “partner” to the aluminium anode). Some currents and conditions allow the battery to work well for more cycles. But under other conditions, aluminium can build up in uneven, dendritic structures that ultimately cause the battery to fail.
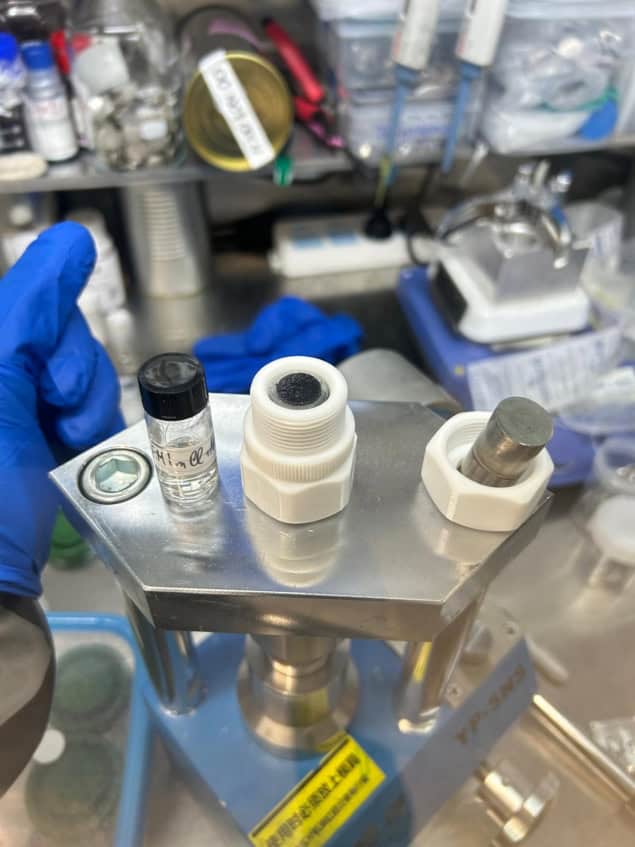
To understand how this happens, the researchers investigated how different electrolytes and cycling conditions affect the SEI layer. They discovered that in some cases, when the SEI isn’t forming evenly, aluminium oxide (Al2O3) – which is normally a protective layer – can actually aggravate the problem by causing the aluminium to deposit unevenly. They also found that low currents can deplete some materials in the electrolyte, leading to parasitic reactions that further reduce the battery’s efficiency.
To solve these issues, the scientists recommend exploring different aluminium-alloy chemistries. They also suggest that specific conditioning protocols could smooth out the SEI layer and improve the cycling performance. One example of such a conditioning protocol is pre-cycling, which is a process where the battery is charged and discharged in a controlled way before regular use to condition it for better long-term performance.
“Our research demonstrates that, like in lithium-ion batteries, aluminium-ion batteries also need pre-cycling to maximize their lifetime,” Rakov tells Physics World. “This is important knowledge for aluminium-ion battery developers, who are rapidly emerging as start-ups around the world.”
By understanding the unique pre-cycling needs of aluminium-ion batteries, developers can work to design batteries that last longer and perform more reliably, bringing them closer to real-world applications.
How far are we from having an aluminium-ion battery in our mobile phones?
As for when those applications might become a reality, Rakov highlights that AIBs are still in the early stages of development, and many studies test them under conditions that aren’t realistic for everyday use. Often, these tests use very small amounts of active materials and extra electrolyte, which can make the batteries seem more durable than they might be in real life.
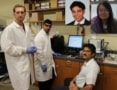
Designing highly reversible aluminum-ion batteries with graphene
In this study, Rakov and colleagues focused on understanding how aluminium-ion batteries might degrade when handling higher energy loads and stronger currents, similar to what they would face in practical use. “We found that different types of positive electrode materials lead to different types of battery failure, but by using special pre-cycling steps, we were able to reduce these issues,” Rakov says.