Physicists in Sweden have teamed up with leading paper and packaging manufacturers to develop a new breed of electronic devices made from paper and conducting inks.
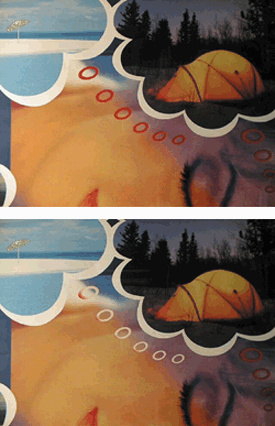
Packaging materials that display animated adverts and containers that sound an alarm if their contents go mouldy are just two possibilities that could result from a new area of technology called “paper electronics”. The substitution of paper for semiconductors in electronic components might sound bizarre, but Swedish physicists are currently developing devices that can be printed onto paper using conventional industrial-scale printing methods.
Many electronic devices rapidly become obsolete as technology continues to improve. There is also a growing trend towards adding electronics to items that were previously difficult to make electronically active, such as plastic and paper. Both factors are motivating the electronics industry to find cheaper ways to manufacture products. Some 50 years after the first transistor was developed, circuit boards are still being manufactured from a large substrate that undergoes about 50 different processing steps before being cut into smaller circuit boards. A substrate that can be manufactured cheaply and quickly is needed to satisfy the industry’s demands.
Paper seems an obvious replacement: it is flexible and we have produced more of it, in terms of surface area, than any other material. These days paper is manufactured in an environmentally friendly way and can be printed on in a fast “reel-to-reel” process. Indeed, a diverse range of printing, coating and lamination processes is used to convert paper into products.
An industrial revolution unfolds
Our group at the Swedish electronics and optoelectronics company, Acreo, has teamed up with physicists at Linköping University to investigate how electronic functions can be added to paper using conducting molecular materials and polymers (both organic displays and plastic electronics were featured in the March 1999 issue of Physics World). We are also working with paper and packaging manufacturers, including Modo Paper and Tetrapak, to ensure that we use standard industrial processes in order to be able to produce low-cost products in high volume.
Many materials have undergone an industrial revolution as high-speed manufacturing processes have usurped slow and expensive production methods. Paper used to be made one sheet at a time and cut into smaller pieces. Now newspaper is produced in mills on 10-metre wide rolls at a rate of about 100 kilometres per hour. In addition, the printing and conversion of paper into other packaging products is done at very high speeds in continuous-flow processes.
But we have to fulfil some fundamental conditions before electronics can undergo the same revolution. First, the substrate has to be flexible so that it can be transferred easily from reel to reel. Second, the electronic materials have to be in the form of a solution so that they can be printed or coated onto the substrate. Third, we must be able to print features that have the right thickness and width so that they can function as electronic devices. Finally, we need a technology that ensures the devices can be distributed onto the surface to form different electronic systems.
Our approach – which uses paper as a substrate and relies on existing printing and lamination techniques – meets these demands and allows devices to be manufactured with low environmental impact. We have chosen organic molecules and polymers as the active electronic materials because they can be processed from solution. Moreover, the various techniques for converting paper into a printed product are well suited to producing the layer thickness and linewidths required for electronic devices. For example, the offset printers that are typically used to print magazines can reproduce features 10 µm wide and with a well defined thickness as small as 1 µm. Based on these techniques, we have created electronic materials with the dimensions necessary to manufacture proper devices.
We carry out the fundamental development work on paper electronics in our lab at Linköping, while the actual manufacturing process for such devices is being developed at Acreo within the framework of the PAELLA project.
Posters, pigments and parcels
The first application we have targeted is existing paper products, such as packages and advertising billboards. Indeed, we have developed a simple paper display some 70 x 100 cm2 based on electronically active pigments, which updates information and images. An electrical signal controls the colour of the pigment in much the same way that a chameleon alters the tone of its skin. Currently the inks can turn from one colour to another, but we are also developing pigments that can change into any colour state.
The choice of pigment material and the device architecture depend on the application. Pigments that can switch rapidly from one colour to another are known as dynamic and require power to remain in each of the states. Dynamic inks have been successfully demonstrated in large billboards to introduce animated areas to an otherwise static image (see figure).
Meanwhile, pigments that stay in the same state and only need power to change them from one colour to the next are known as bistable. The prime focus for bistable display technology is for tags and stickers, as well as large paper billboards. Indeed, with bistable technology it becomes possible to produce price tags that can be updated electronically and address labels for parcels that can be changed.
Printed sensors are another potentially huge application. A simple communication circuit together with a sensor printed onto a package could be used to remotely test the condition of the stored goods. Imagine, for example, being able to detect a carton of sour milk in a warehouse from the electronic signal it emits. Supermarkets, which increasingly rely on haulage companies to transport perishable produce from the warehouse to the store, would benefit enormously from such devices. Any items that had deteriorated could be removed long before they reached their final destination, thus saving on transport costs.
A crucial part of any electronic device is the power source. Energy can be transferred to paper devices by connecting the electronic pigment cells to coil antennas and transmitting signals from a remote antenna. Alternatively, physical contacts or battery tags can be added to the product. The power demands of the devices we have tested are very low, as we have focused on devices that only consume power when they are updated and read out.
So far we have looked at introducing paper electronics into traditional paper items to extend the existing use of paper – “electronic paper”. As the technology develops we plan to make paper an integral part of traditional electronic products.