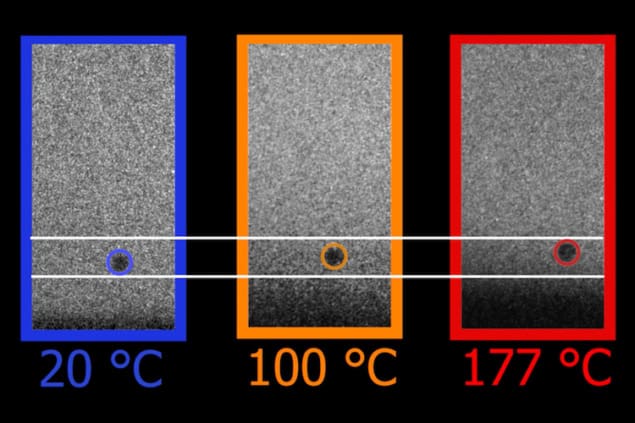
Heating metals usually makes them softer, but new micro-ballistic impact testing experiments show that if they are deformed extremely quickly during heating, they actually become harder. This unexpected discovery, made by researchers in the department of materials science and engineering at the Massachusetts Institute of Technology (MIT) in the US, could be important for developing materials for use in extreme environments.
In the new work, Christopher Schuh and his PhD student Ian Dowding used laser beams to propel tiny particles of sapphire (an extremely hard material) towards flat sheets of pure copper, titanium and gold at velocities as high as a few hundred metres per second. Using high-speed cameras to observe the particles as they hit and bounce off the sheets, they calculated the difference between the particles’ incoming and outgoing velocities. From this, they determined the amount of energy deposited into the target sample, which in turn indicates its surface strength, or hardness.
Schuh and Dowding found that increasing the temperature by 157 °C boosted the strength of the copper sample by about 30%. At 177 °C, the sample’s hardness increased still further, to more than 300 MPa, making it nearly as hard as steel (304 MPa) at this temperature. This result is counterintuitive since pure copper is a soft metal at low strain rates and would normally be expected to soften further at high temperatures. The pair observed similar effects for their titanium and gold samples.
Drag strengthening
Schuh and Dowding say that the anomalous thermal strengthening effect appears to stem from the way the metals’ ordered crystal lattice deforms when the sapphire microparticles strike it. This effect is known as drag strengthening, and it occurs because higher temperatures increase the activity of phonons – vibrations of the crystal lattice – within the metal. These phonons limit the deformation of defects, like dislocations, in the metal, preventing them from slipping as they would do at lower temperatures.
“The effect increases with increased impact speed and temperature,” Dowding explains, “so that the faster the impact, the less the dislocations are able to respond.”
Unlike in previous high-velocity impact experiments, which used centimetre-scale particles, the small particles in this study do not create significant pressure shock waves when they hit the sample. “In our work, the impacted region is smaller than around 100 micrometres,” Schuh tells Physics World. “This small scale lets us perform high-rate deformations without having a large shock wave or high-pressure conditions to contend with. The result is a clean and quantitative set of data that clearly reveals the counterintuitive ‘hotter-is-stronger’ effect.”

Fatigue-generated cracks fuse back together in metals
The behaviour the MIT researchers uncovered could come in handy when designing materials for use in extreme conditions. Possible examples include shields that protect spacecraft from fast-moving meteorites and equipment for high-speed machining processes such as sandblasting. Metal additive manufacturing processes such as cold spraying could also benefit.
The researchers, who report their work in Nature, say they would now like to explore the range of conditions and materials in which this “hotter-is-stronger” behaviour occurs.