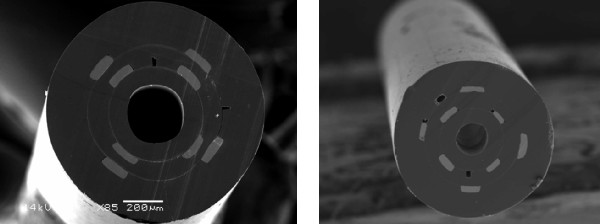
It may sound like something from a highly stylized science-fiction film but imagine a soldier who could detect threats by seeing in all directions at once. A group of researchers at the Massachusetts Institute of Technology (MIT) have taken the first step to turning this futuristic vision into reality with a new imaging technique that involves light-detecting fibres that could be woven into a flexible web or even a soldier’s uniform.
The individual fibres created by the MIT team consist of two separate sheets of semiconducting glasses — just 100 nm thick — folded up like a Swiss roll. Electrodes are worked into the fibres and the resulting cylinder, which is 35 cm long, is covered in an insulating cladding. The fibres can detect light because photons interacting with a semiconductor material can ionize the component atoms, thus triggering a current in the presence of a potential difference.
Picking the colour
Long-wavelength photons arriving at the fibre with relatively low energy can only trigger a significant current in the outer semiconductor. Shorter-wavelength photons, in contrast, have higher energies and so can trigger currents in both the inner and outer semiconductors. So by comparing the relative currents in the two semiconductors, the researchers can determine the colour of the incoming light.
The biggest challenge when manufacturing these fibres was integrating the electrodes: “We needed to choose a metal that had very different electronic properties but similar thermal properties to the semiconductor,” says Fabien Sorin, one of the MIT researchers. Tin was chosen because it is highly malleable, which means that it can be deformed plastically without fracturing.
Sorin and his team merged the separate layers by carefully heating them in a furnace and then drawing them into fibres that retain the original orientation of the various layers. “The trick was to encapsulate the metal within the semiconductor, rather than melting the different layers into one,” says Sorin. The researchers then combined a series of fibres into a 32 × 32 mesh.
Smiles all round
To demonstrate the imaging capability of their material, the researchers placed it in front of a “smiley face” with a diameter of 800 µm painted in chrome on a glass substrate. This generated a distinct pattern on the fabric mesh that was then fed into a computer. An algorithm then assimilated the data to create an image of the object on the computer screen. The face’s features were successfully resolved with colour differentiation determined to a resolution of 5 nm.
Changhui Yang, an electrical engineer at the California Institute of Technology, is impressed by the research. “Imagine a soldier wearing a uniform made with this technology. The uniform will be able to alert the solider if an enemy tags them with a laser beam,” he says.
This research was published in Nano Letters.