Coatings is big business, contributing £383 billion pounds to the UK economy alone. nanotechweb.org speaks to coatings businesses large and small about economies of scale versus the agility to change course, as well as handling market and regulatory pressures as they bring their state-of-the-art coating technology to consumers.
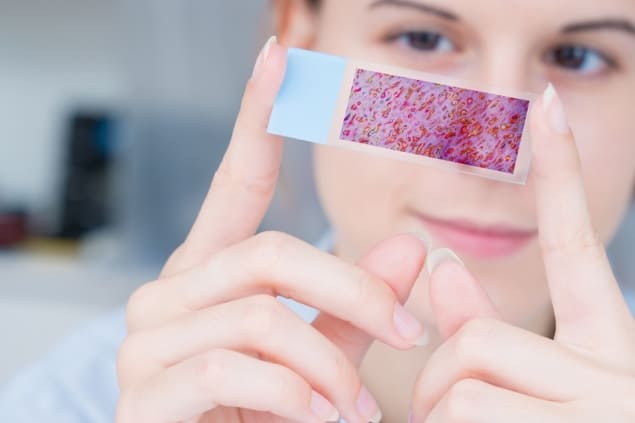
There are close to a billion passenger cars on the road worldwide – a quarter of them use glass made by NSG. Yet while the company seems to specialize in glass – glass that allows heat in but not out; glass that inhibits condensation for display fridges; and even glass that can oxidize organic dirt to form CO2 – as Su Varma, the company’s incubation portfolio manager, told attendees at the Materials Research Exchange 2018 in the UK, they are really selling products that have functional nanoscale coatings on a glass substrate. With the exception of products based on low-iron or ultrathin glass, the real value add is in the coating.
Fabrication matters
NSG’s coatings are largely oxides, such as titanium oxide to catalyse oxidization of organic compounds or doped tin oxide for transparent conductive coatings in which NSG have a leading global position. Key to the company’s success is their fabrication procedures, which include chemical vapour deposition (CVD), physical deposition and sol gel processes. Printing and atomic layer deposition are some of the possible future processes to deposit transparent thin functional films. “The same material but a different process gives a different functionality,” Varma explains.
Forty years of development have gone into the company’s CVD processes. The technique exposes a substrate to different vaporized chemicals that react or decompose forming high quality deposits. Real-time monitoring is in place at NSG to check that the thickness meets the desired specifications. Even just a couple of nanometres out of spec can change the functionality from transparent to reflective, and ultimately customer dissatisfaction. The tight adherence to specifications are met at a formidable fabrication rate with coatings that are around 80 nm thick in total, combining as many as 12 functional layers, produced at rates of 6m × 3.3m in just 45 seconds. “If it’s not on that scale it’s not economic,” says Varma.
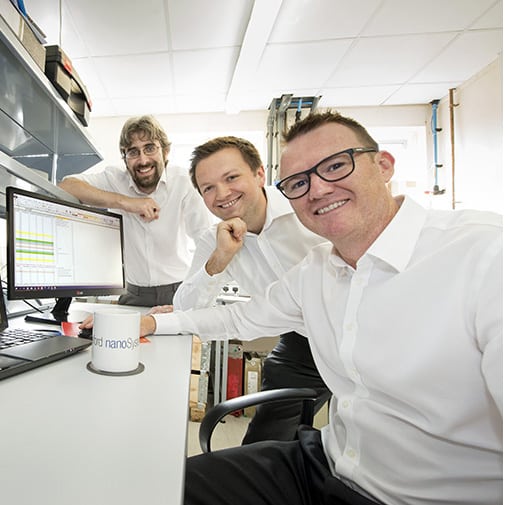
Starting up
While large companies may rely on a £40 million fabrication plant that can churn out square metres of coatings in seconds, the initial stages of a company’s life cycle will likely have more modest requirements. Current CEO Alex Reip joined Oxford nanoSystems in 2012 at the invitation of an academic acquaintance who alongside an entrepreneur had come up with the idea of setting up a coatings company focused on heat transfer. Bringing Alex on board as science specialist doubled the employee head count to a grand total of two.
The Oxford nanoSystems heat-transfer coating has a dendritic texture to increase the number of bubbles that form thereby increasing heat transfer in liquids by 524%. The company had an unusual beginning, as they won over the support of an Angel investor in the audience at an Oxford business School competition at the outset. As a result, they have been developing the technology and commercializing it simultaneously, as opposed to a lot of start-ups who develop the technology and must then leap “the valley of death” to achieve commercialization. With subsequent funding from innovate UK and others the total investment now exceeds £1,400 000. They plan to double their employee base again to a total of eight in the next 12 months, and they have just applied for further funding to take the company through the next few years after which they hope to be self-sustaining.
When he joined the company, Reip had just finished a PhD on nanophosphors for fingerprint detection. Although some of the basic chemistry was similar, moving into a new field of research meant there was a lot of knowledge to pick up. “The heat transfer field of research is vast,” says Reip. But Reip suggests in some ways this was the easy part. “Moving from research to commercializing something was the bigger leap.”
Applications of Oxford nanoSystems coatings range from low cost and large quantities in sectors such as air-conditioning, to electronics and space technology where costs are high and the volume is low. “We started on boilers but spreading our scope makes failure much less likely,” says Reip. “Being a small company makes it easier to change tack.”
Yet commercializing for different industries presents its own challenges to meet the different requirements, and Oxford nanoSystems has also had to contend with market inertia in some areas. “The AC market doesn’t change much so you need to prove more for take up,” says Reip. That said new markets are emerging, which may be easier to penetrate, such as the rise in electric vehicles where cooling battery coatings may be crucial.
Regulatory market changes
Changes in regulations can also influence the market for coatings. Indestructible specializes in protective paints, largely for applications in the aerospace industry. So far their products have incorporated nanomaterials, particularly for paints to protect regions exposed to high temperatures, and as Managing Director Brian Norton, whose father founded the company, points out nanomaterials have been used for decades, carbon black being one example.
However the latest evaluation by the International Agency for Research on Cancer (IARC) evaluation is that, “Carbon black is possibly carcinogenic to humans (Group 2B)”. In addition exposure to carbon black can irritate people’s airways. EU regulations for nanomaterials in general are currently under development and although Indestructible is still looking into the possible attractions of exploiting graphene in its paints, pending regulatory restrictions have made the use of nanomaterials less appealing to the company on the whole.
Necessity is the mother of invention
Regulatory inhibitions are already under contention in some fields. Throughout the second half of the twentieth century fluorocarbons, particularly long eight-atom-chain fluorocarbons (C8 PFCs) were the back bone of the non-wetting coatings sector. Until recently, the efficacy of C8 PFCs had drawn attention away from the hazardous emissions they break down into: PFOS and PFOA, which are not only carcinogenic but also persistent and bioaccumulative. “We can detect increased values of these substances in watercourses and even in the breast milk of US mothers,” stated a recent release by the specialists in ultra-thin coatings, Nano-Care Deutschland AG.
Founded in 2000 as a spin-off from the Leibniz Institute for New Materials (INM), Nano-Care produces coatings for textiles, building construction and non-absorbing surfaces. A key achievement recently was the launch of the Nanoflex F-Bond system in February 2018. As legal restrictions have tightened up on the use of C8 PFCs a lot of companies have resorted to using more comparatively less pernicious C6 PFCs. However, use of any PFCs is still cause for concern for organizations like GreenPeace, who are campaigning for their complete elimination, and as C6 PFCs are less effective than their longer chain counterparts, larger quantities are needed.
“The great challenge for us has been to retain existing high standards of oil repellency – whilst eliminating long-chain fluorination,” says Oliver Sonntag, CEO of Nano-Care, and relative of Bernhard Sonntag who founded the company. The company has already developed fluorine-free durable water-repelling coatings in their “Intelligent Hybrid” range, using chemicals that have a silicon dioxide backbone. However as Sonntag points out some applications need a textile coating that repels not just water but alcohol and oil as well. “Our particular focus is on military, work-wear and health sectors, which have to satisfy especially high-performance requirements and currently have only temporary permission to use C8 technologies. Their elimination – particularly outside the European Union – is an important step towards achieving “ecological sustainability” in the textile industry.”
As part of the Intelligent Hybrid range, the Nanoflex F-Bond system reduces to a minimum both the chain length and the quantity of PFCs required to achieve C8 performance with short-chain C6 technology. It combines the silicon dioxide backbone with a modified C6 polymer and process additives, thereby achieving dewetting performance at level 8 on polyester and 7 on cotton according to ISO 14419. It has also been certified with the Eco Passport standard 100 by Oeko-Tex.
The company is currently working towards C4 technology with the ultimate aim of eliminating PFCs altogether. Nano-Care sees a market potential amounting to the hundreds of millions of Euros with their Intelligent Hybrid technology. Based in Saarwellingen with subsidiaries in the UK and Mexico, the company is currently expanding and reorganizing its corporate structure to include a new Textile Effects’ department. It currently has 70 employees and customers in 65 countries.
Keeping the industry in good health
Besides regulating against health hazards, the coatings industry stands to benefit from a general increase in standards and digitization according to the Surface Engineering and Coatings (SEAC) report. As Allan Matthews, from the BP International Centre for Advanced Materials told delegates at Materials Research Exchange 2018, £140 billion of goods in the UK economy alone would not work without coatings. Yet he added that in the view of the Royce Institute – the UK National Centre for Research and Innovation of Advanced Materials – coatings is the one sector where the data falls short. With the main hub at Manchester University, the Royce Institute was set up as part of plans for a “northern power house” in the UK under former UK Chancellor of the Exchequer George Osbourne.
The Royce is currently working with partners to implement findings and recommendations from the SEAC report such as improving process coatings modelling; developing state-of-the-art facilities; driving digitization; and improving characterization, analysis, testing and evaluation. It is hoped that focussing on these areas will ensure that businesses in coatings are not just match fit, but reach their full economic potential on the global stage.