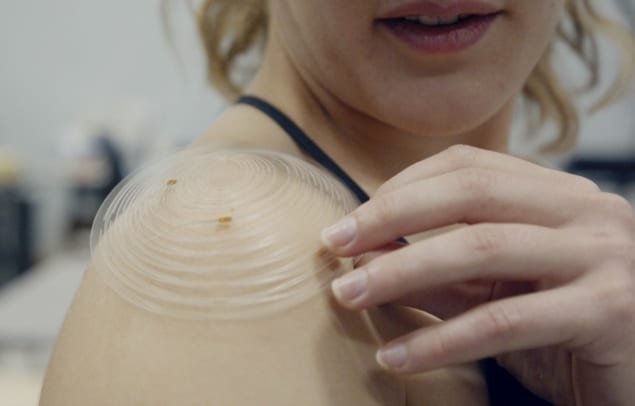
A low-cost sensor that can track shoulder movements has been unveiled by scientists in the US. The simple device is assembled in a flat configuration from a laser-cut sheet of plastic and two strain sensors. The principles of kirigami — the Japanese art of paper folding cutting – allow the device to adopt the 3D shape of a user’s shoulder.
After breaking his collarbone in a bike crash, material scientist and engineer Max Shtein was surprised when his physical therapist used a protractor to measure the range of motion in his shoulder. When he returned to his lab at the University of Michigan, he was determined to create a better solution.
Shoulder movement can be measured more accurately using motion-tracking camera systems, but Shtein felt that a wearable system would be better because it could monitor patients at home. “The shoulder, in particular, moves in a very complex way. It is one of the most well-articulated joints in the body,” Shtein explains. “Nobody has really been able to track it properly with anything wearable, and yet it is key to so many activities in sports and daily life.”
Unfolds like a spring
To accommodate this movement, his team turned to kirigami. This is a variation of origami that involves cutting and folding paper to create decorative shapes such as snowflakes. They used a laser to cut a pattern of rotationally symmetrical, concentric circles into a thin sheet of plastic, creating a device that unfolds like a spring into an interconnected network of alternating saddles. In use, the device opens over the shoulder, and flexes and strains as the shoulder moves.
Team member Erin Evke explains the benefits of kirigami: “If you take a sheet of paper and try to wrap it around a sphere, it’s impossible to do so without folding or wrinkling the paper. This would significantly stress the sensors before your measurement even began. Our cut pattern avoids this problem.”
The team measured the stress and strain across the kirigami device and also calculated its mechanical properties using finite-element analysis. Once they understood the response of the device, they added two strain gauges that allow the device to detect complex shoulder motions. A gauge at the top of the arm captures the raising and lowering of the limb, a gauge at the back of the shoulder to measure arm movement across the body.
Shoulder shrugs
When tested against a 19-camera motion tracking system, the kirigami shoulder sensor was found to accurately measure the raising, lowering, and circling of the arm. It was also able to detect movements such as running, shoulder shrugs and rotations of the wrist.
The team says that sensors could be mass produced for less than $10 each using existing technologies. Sensors could be incorporated into wearable devices and used by physical therapy patients to log exercises and progress outside of medical settings. Ultimately, Shtein and colleagues see kirigami sheets as a versatile sensing platform that could be used with different sensors to create a range of multifunctional health and movement monitoring devices.
Evke says that the sensors could be beneficial to athletes: “Since you can tune the cut design to match the curvatures of all different parts of your body, you can generate a lot of data that can be used to track your form – for instance while lifting – as well as the amount of strain applied on your joints. The user could be alerted of improper form in real-time and therefore prevent injuries.”
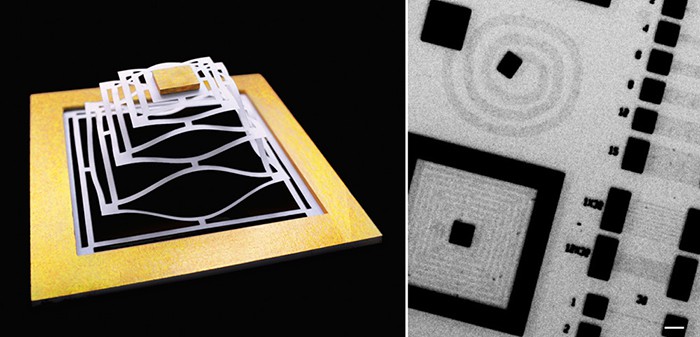
Stretchable graphene transistors inspired by kirigami
Electrical engineer and physicist Jamal Deen, of McMaster University in Canada, who was not involved in the research, recently produced a review of joint monitoring methods. He told Physics World that inertial measurement units (IMU) based on micro-electromechanical systems have the most potential for developing wearable joint tracking systems, as they are compact, inexpensive and low-power. An IMU measures the motion of an object by measuring its linear and rotational accelerations. He adds, however, that to the best of his knowledge, “clinically accepted IMU-based joint monitoring systems are not available in the market”.
Deen believes that strain sensors are very suitable for joint monitoring systems, adding that integrating them with rotationally symmetric kirigami is a novel idea that needs further work. In particular, the current system is wired and the plastic sheets could hinder joint movement. “The developed system needs proper validation with respect to a clinically accepted system to prove its accuracy and efficacy,” he explains. “Finally, it is essential to include a wireless communication module and an independent power source to make the system completely wearable.”