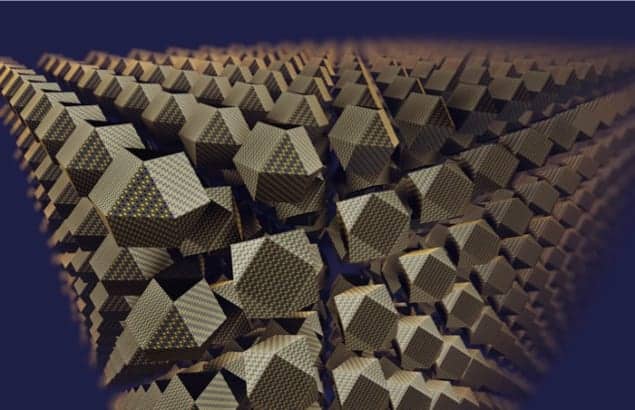
Researchers in the US and Germany have gained important insights into how molecular coatings affect how nanometre-sized particles organize themselves into regular “superlattices”. By combining new X-ray techniques with thermodynamic analysis, the team has worked out why the same nanoparticles can assemble into several distinct structures. The scientists hope that their insights could lead to new designer materials.
Over the past decade or so, man-made metamaterials have been created to have desirable properties not found in natural materials. These include nanoparticle superlattices – regular arrays of nanometre-sized structures – that show promise for a range of technology applications, such as photovoltaics, light-emitting diodes and thermoelectrics. However, before these properties can be exploited commercially, researchers must first gain a better understanding of how the tiny nanoparticles come together via complex nucleation and other processes.
Intricate steps
In the early stages of nucleation, nanoparticles aggregate randomly and form an amorphous structure with limited short-range ordering. The particles then minimize the total free energy in the structure by crystallizing into a long-range ordered superlattice. The nanoparticles appear to behave like hard spheres, packing together to form a fairly simple superlattice phase. However, they also appear to go through various quite intricate nucleation and growth steps that involve multiple nanoparticle interactions with surrounding solvents and surface-capping ligands, which are molecules that attach to the surface of the nanoparticles.
To better understand these mechanisms, the US–Germany team decided to look at how oleic-acid-capped lead-sulphide nanoparticles just 3.5 nm in size assemble in solution under a variety of experimental conditions and different temperatures and pressures. The changes to atomic structure occurring at the nanoparticle cores and at the capped ligands can be followed from the same volume of sample using both high-resolution synchrotron small-angle X-ray scattering (SAXS) and wide-angle X-ray scattering (WAXS) – new techniques developed by the researchers themselves.
Trio of polymorphs
The results show that the nanoparticles nucleate in three main superlattice structural phases or polymorphs. These are amorphous, body-centred-cubic (bcc) and face-centred-cubic (fcc) phases. The type of superlattice formed can be controlled by changing the distance between the nanoparticles without changing their size. For example, when the inter-nanoparticle distance is increased, the particles pack together in a slightly looser but more ordered way while the capping molecules rearrange and change structure, modifying the overall surface energy.
“Our analyses have shown that the nanoparticles appear to either maximize entropy or minimize the enthalpy in the structure to reduce the total free energy through multiple interactions with the surface molecules,” explains team leader Zhongwu Wang. “These findings will hopefully inspire both experimentalists and theorists to consider the importance of surface-capping molecules when modelling these superlattice structures. From an applications point of view, our phase diagrams could offer a guide to material fabrication and help make ‘designer’ solids with specific structures, inter-nanoparticle distances and sizes.”
The researchers now plan to look at binary nanoparticles and other more complex nanostructures. “Using techniques only available in our labs at the Cornell High Energy Synchrotron Source (CHESS), we aim to build a series of structure–property relation diagrams of confined nanoparticles with different sizes and shapes,” Wang told physicsworld.com.
The current work is presented in Nano Letters.