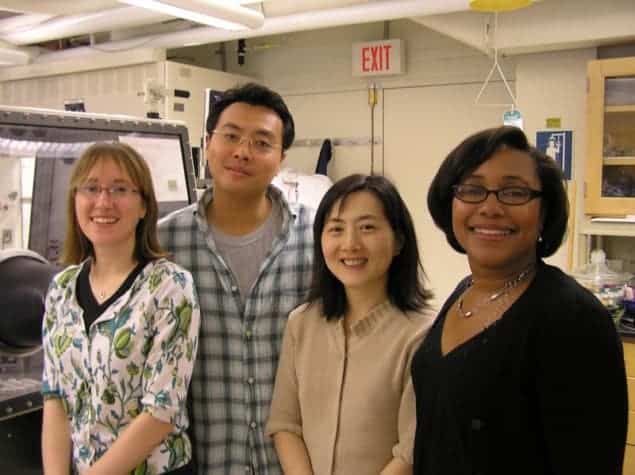
Carbon nanotubes could make ideal electrodes for lithium-ion batteries, boosting their power output by up to ten-fold compared with conventional devices, claim a group of researchers at Massachusetts Institute of Technology who have demonstrated the technique. They say that it will enable manufacturers to shrink batteries for portable applications such as ultra-light mobile phones and wearable electronics. In the longer term it could lead to high-performance batteries for larger applications such as hybrid electric cars and industrial machinery.
Lithium-ion batteries consist of two electrodes, the anode (which is negative) and the cathode (positive), separated by an electrolyte – a conducting material through which charged ions can move easily. During cell discharge, the positively charged lithium ions travel across the electrolyte to the cathode, so producing an electric current. When the batteries are recharged, an external current forces the ions to move in the opposite direction so that they can be stored at the anode.
These batteries are routinely used in portable electronics but their power output and charge-storage capacity still remain far below those of electrochemical capacitors. Batteries, however, have several advantages over capacitors, not least that they can store more charge and have a much lower rate of self-discharge.
A simple swap
Now, Yang Shao-Horn of the Massachusetts Institute of Technology (MIT) and colleagues have discovered a way to increase power output in these devices. They replace one of the electrodes in lithium-ion batteries by one made from multiwalled carbon nanotubes, which are tiny rolled up sheets of carbon atoms. The power output of the improved devices is now on a par with electrochemical capacitors at 100 kW kg–1, but their “gravimetric energy” (the amount of charge they can store) is up to ten-fold higher.
The new CNT electrodes can “grab” and store larger amounts of lithium charge than conventional electrodes, which have been made from many chemicals over the years including iodine and copper sulfide. For example, there are numerous oxygen groups that can undergo redox (oxidation or reduction) reactions on the surface of the CNTs. The CNT electrodes are also very stable. The researchers found that the material performed just as well even after 1000 cycles of charging and discharging.
Shao-Horn’s team made the new electrodes using a layer-by-layer fabrication technique in which a base material, such as ITO glass or metal foil, is dipped into solutions containing carbon nanotubes. The nanotubes are made negatively or positively charged, for the electrodes, by treating, or “functionalizing”, them with simple organic compounds, such as carboxyl (COOH) and amine (NH2) groups. These CNT layers are placed alternately on a surface and bind strongly together because the positively charged tubes attract the negatively charged ones, to make stable and robust films after a simple heat treatment.
Bridging the technology
“We now hope to make thicker electrodes – up to 50 µm across – with the same performance characteristics,” Shao-Horn told physicsworld.com. The electrodes made so far are only a few microns in size, which limits their use to small, portable, applications.
Yury Gogotsi of Drexel University, also in the US, who was not involved in the work, believes that there are many potential applications for these high performing batteries. “Bridging the performance gap between batteries and electrochemical capacitors is an important task, and the MIT group has made an important step in this direction,” he says.
“There is still much work to do though. The data presented in this new work may only be valid for relatively thin films and individual electrodes with no packaging and it may be completely different for a real-world battery with its multiple parts and outer container”, he adds.
The results were published in Nature Nanotechnology.