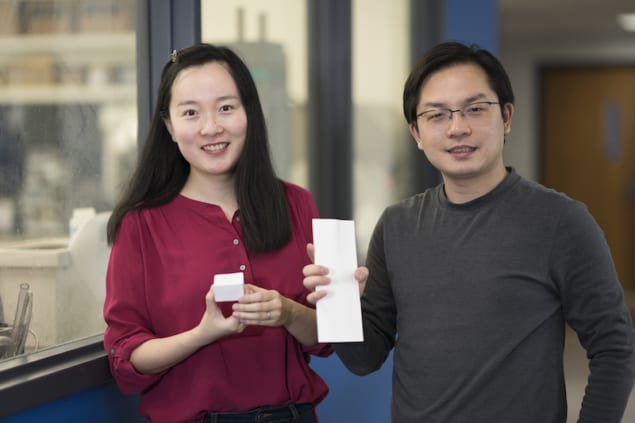
A new material dubbed nanowood made from aligned nanocellulose fibres could be used to thermally insulate buildings – both residential and commercial – to make them more energy efficient. The material, which is also lightweight and mechanically strong, is easy to fabricate using a simple chemical treatment. It contains naturally aligned cellulose nanofibrils, which makes it anisotropic – that is, it conducts heat more efficiently along the direction of the fibres, which reduces local heat build-up in the structure.
“Our wood-based material boasts a desirable mix of super thermal insulation, good mechanical strength, low mass density and cost-effectiveness,” explains team leader Liangbing Hu of the University of Maryland in the US. “Such a combination has never been realized before.”
The researchers made their nanowood using a chemical process to remove inter-lignin and hemicellulose to preserve only the cellulose component of their wood sample. The lignin removal step is compatible with processes used in the paper-making industry, stresses Hu, which means that it could easily be adapted to existing industry infrastructures.
Naturally anisotropic
Since it is derived from wood (which has a naturally anisotropic structure), the nanowood is anisotropic too. The nanocellulose fibrils in the material line up in one direction during the chemical treatment, allowing heat to travel more efficiently along the nanofibril direction. Indeed, Hu and colleagues measured a thermal conductivity of 0.03 W/mK in the transverse direction (perpendicular to the nanofibrils) and a roughly two times higher thermal conductivity of 0.06 W/mk in the axial direction. This prevents local overheating from accumulated thermal energy, something that is not possible in isotropic thermal insulators, say the researchers.
The mechanical strength of the nanowood is 50 times higher than cellulose foam and more than 30 times higher than the most commonly employed thermal insulation materials, such as silica and polymer aerogels, Styrofoam and wool. This high strength comes thanks to effective bonding between the aligned cellulose nanofibrils, which have a compressive strength of 13 MPa in the axial direction and 20 MPa in the transverse direction at 75% strain.
Towards commercialization
It is also very light, with an overall mass density as low as 0.13 g/cm3, says Hu, and is breathable, which means that it can be used indoors.
“Finally, the nanowood can effectively reject solar thermal energy (it reflects 95% of all solar spectrum wavelengths),” he tells nanotechweb.org.
As well as being used to thermally insulate buildings, it might also find use in a variety of other heat management contexts, such as in electrical, optical and space applications in which heat transfer and waste heat transfer needs to be tightly regulated, he adds.
The researchers, reporting their work in Science Advances DOI: 10.1126/sciadv.aar3724, say that a UMD spinoff company, Inventwood LLC, is now commercializing the technology.