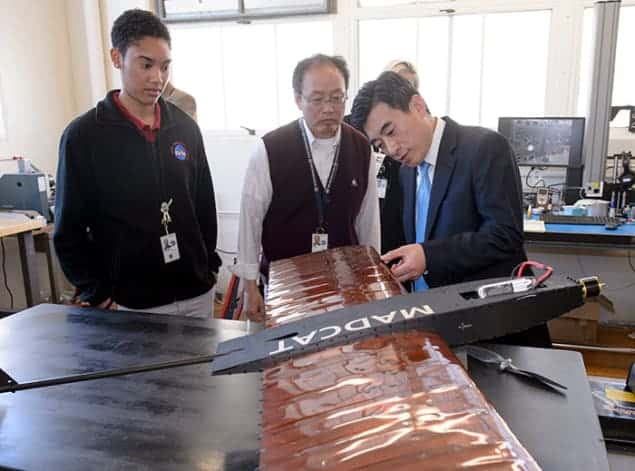
A new type of composite wing that can change its shape according to flight conditions has been made from a lattice of small, lightweight components. This morphing ability could allow for more aerodynamic, manoeuvrable and fuel-efficient aircraft that are also simple to construct. Described as a “digital-material” approach to aeronautical design, the technology was developed by a collaboration involving NASA and several US universities, and could be applied to a variety of other structures from bridges to wind turbines.
Most aeroplanes have fixed wings that are fitted with ailerons, which are hinged control surfaces used to manage the lift and roll throughout the flight. The shape of fixed wings, however, is always a compromise in efficiency with different wing configurations being more suitable for different speeds and flight paths. Because of this, the concept of a wing that could change shape during flight has always been something of a holy grail for aircraft engineers – not the least because this could lead to much greater fuel efficiency.
Attempts to achieve this, however, have been unsuccessful. This is largely because the typical approach to wing deformation relies on the use of mechanical control structures that are simply too heavy to improve the overall efficiency of the wing. This new morphing design takes a different approach in which the entire wing becomes the deformation mechanism. Motors in the aircraft fuselage apply a pressure to each wing, which then twists uniformly along its length.
Lightweight lattice
The morphing wing is made from a lattice of lightweight, flexible, centimetre-scale, carbon-fibre-reinforced polymer components. These are assembled, like a child’s construction set, into larger structures. While each component is strong and stiff, the overall flexibility of the structure can be tuned by varying its overall shape, as well as the shape and exact composition of its individual components. The wing is completed with an outer skin of overlapping, flexible polyimide pieces that cover the lattice structure – much like scales on a fish.
The digital-materials approach “presents a general strategy for increasing the performance of highly compliant – that is, ‘soft’ – robots and mechanisms,” says team-member Kenneth Cheung, who is an engineer at NASA’s Ames Research Center in California.
Testing the wing design in a wind tunnel, the researchers found that the new wings can both match the aerodynamic properties of a conventional, fixed wing and deform in such a way that replaces the need for trailing-edge ailerons – but with only a tenth of the weight of a fixed wing. Following these tests, the researchers developed a small, unmanned aircraft, which has demonstrated excellent manoeuvrability (see image above). While such craft could pave the way for enhanced drones, the wing designs could also be scaled up for larger aircraft, Cheung says.
Made by robots
While the wings used in the studies so far have been assembled by hand, the team is also collaborating on the design of miniature robots that could assemble – and even examine and repair – such structures automatically. The wing’s composite nature should allow for simpler construction and repair processes – and could even allow the wing to be broken down into its component parts and re-used for some other purpose.
“Digital materials and fabrication are a fundamentally new way to make things and enable the conventionally impossible,” says Gonzalo Rey, chief technology officer for the aerospace-engineering company Moog, who collaborates with the researchers. The concept, he adds, has far broader potential, and could extend to such structures as flexible robots, bridges and skyscrapers, “providing not only improved performance and survivability, but also a more sustainable approach by achieving the same strength while using, and reusing, substantially less raw material”.
Other potential applications for digital materials include the in-situ fabrication of wind-turbine blades and space structures – both of which are expensive and logistically complicated to transport in their completed form to their place of operation.
New concept
Jianguo Zhao – a mechanical engineer at the Colorado State University, who was not involved in this study – says that the idea of using lightweight, tuneable cellular solids is a new concept in this area. He adds: “I am looking forward to see if the group can [use] this technology to fabricate airplanes with morphing wings that can fly freely, which might transform the traditional way to design and manufacture aircraft.”
The researchers are now working to better understand the failure modes of their digital materials, with a mind to optimizing their robustness. They are hoping to develop and test a complete aircraft that is designed from the top down with their new construction strategy – along with exploring the potential to develop various other modular structures and integrated robotics.
The research is described in Soft Robotics.