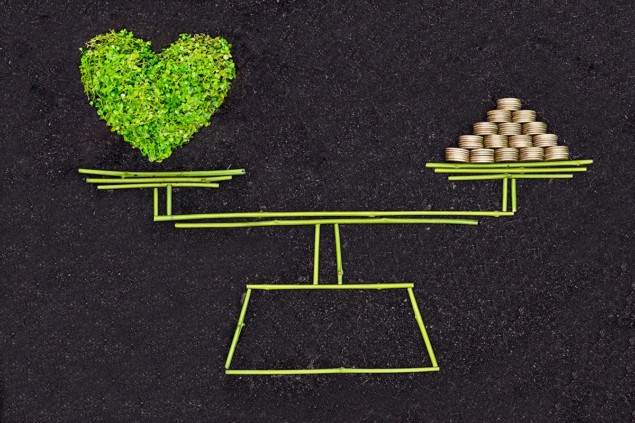
“We need to get better at doing more with less,” Ed Lester, a professor at Nottingham University and technical director of the spin-out company Promethean Particles told attendees at the Advanced Material Show at Telford International Centre in the UK last week. Promethean Particles opened up the world’s largest nanoparticle plant in 2016, its vast production capacity enabled by continuous online liquid product formulation, which has efficiency advantages over the synthesis of dry nanoparticles mostly for later dispersion in a liquid. As the self-styled “McDonald’s of manufacture” for fast nanoparticle synthesis Promethean Particles may not be the first place you would look for an advocate of an abstemious approach in the materials industry, but Lester was far from alone in voicing concerns over sustainability.
Waste less
Less waste often means lower costs so that environmental interests aside, efficiency savings have an inherent attraction. In terms of less waste in production of materials, and nanomaterials in particular, real-time monitoring can make a real difference. In the past manufacturers have sent samples from batches away for product-control sizing measurements, but finding out at the end of a batch that the sizing is off can write off large quantities of product already made.
Xoptix described how laser-diffraction particle sizing can help. “Laser measuring is simple,” he told Physics World, adding that although these sizing measurements have traditionally used a whole benchful of optics, the set-up can be much more compact. The Xoptix equipment can fit in a large brief case, and installed alongside the production system it can steer samples of the product away for testing and back into the production apparatus to take measurements in real-time and flag up any problems. Other companies at the show including as Malvern Panalytical are also now promoting inline and in situ measurements.
Sam Barton, a service engineer fromThin advantages
Nanomaterials may also contribute to minimizing the toll on the planet’s material resources on account of their enhanced properties, which often allow product designers to make layers thinner while still matching or improving on the performance offered by incumbent materials. While thin layers with electronic and optoelectronic functionality are making waves in potential flexible devices and roll to roll printing for low-cost manufacture, applications exploiting mechanical properties can benefit too.
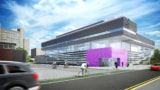
Taking graphene from wonder material to real-world technologies
The Graphene Engineering and Innovation Centre (GEIC) in Manchester plans to pilot a graphene-enhanced road near the centre. “The road isn’t ours to lay,” GEIC Chief Executive James Baker told Physics World, emphasising that the project is in its infancy at present. However conversations with the council are promising and the project also now benefits from six months of data for analysis from a graphene-enhanced road laid side by side a conventional road in Rome. The hope is that incorporating graphene could help towards thinner more durable layers of materials. “The big benefit comes if you can de-ice it,” added Baker, highlighting the challenge of rapid fluctuations between warm and freezing temperatures from day to day in the UK that leads to water freezing and expanding in cracks to form potholes.
This is not carbon
While environmental benefits may feel good for the manufacturer, it’s the attraction they hold for the consumer that makes or breaks the business case. “People won’t pay for green,” Christian Fischer CEO and co-founder of Bcomp told attendees. Bcomp produces automobile materials based on flax, a plant commonly grown anyway as a rotation crop in agriculture. The flax-based material now has a strong offering in the world of motor-racing, where traditionally 50% of the car volume is plastic. However convincing people that there was a place for these alternative more sustainable materials in the sector was far from simple. “Guys my customers just aren’t ready for this brown chalet chic Swiss kind of look – they want carbon,” was the initial response. However, by focusing on light-weighting, a goal shared by any other high-performance automobile manufacturer, Bcomp were able to present a product that could sufficiently outperform incumbent materials to grab notice, with the added bonus of great green credentials.
Re-use, recycle
Bcomp offers alternative to plastics for some applications, but the permanence and prevalence of plastic pollution is an issue all industries need to tackle. As Sally Beken from the Knowledge Transfer Network, who heads the recently established UK Circular Plastics Network told attendees, “It’s not a bad material, the problem is our poor husbandry of it.” Part of the challenge in retrieving and recycling plastic has been the lack of standardization and a proliferation of different plastics each requiring different treatments. For certain plastics established recycling schemes and infrastructure are helping to reposition the material among the more environmentally benign. Government incentives encouraging the use of recycled plastics mean that recycled PET, for example, commands a higher purchase price than the originally produced material. In contrast “biodegradable” plastics can still cause problems if they end up in the ocean, as degradation takes significantly longer at the colder temperatures there.
Design for manufacturing; design for recyclability - Fernando Castro, National Physical Laboratory
Ambitions for recycling have even risen to the lofty heights of space projects, the most braggadocious being the reusable rocket aspirations of SpaceX. A lot can go wrong when sending a rocket into space so again monitoring and real-time measurements are key. Nanmac supplies SpaceX and various other clients with thermocouples for temperature monitoring. The key materials challenge for thermocouples monitoring the extremely high temperatures of rocket launch is the sheath, which needs to protect the instrument from degradation while still letting the temperature through. As a company that span out from Nasa 65 years ago, Nanmac has ample experience in handling the extremes of space missions, but for SpaceX they have now mastered the additional requirement allowing the thermocouples to be re-used.
“Design for manufacture; design for recyclability,” urged Fernando Castro, Head of Materials Science and Engineering at the UK’s National Physical Laboratory, during a session on nanoelectronic materials – design and development. “Because further down the road it becomes much more costly.” The advice highlights a theme that pervaded the conference, that sustainability practicalities merit equal consideration with a material’s production, and that ultimately the long-term interests of materials companies and the long-term interests of the planet are unequivocally entangled.