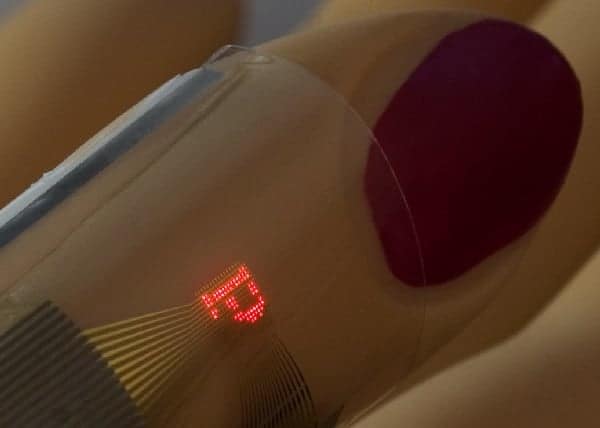
A team of researchers in the US has developed a new technique to shrink the size of inorganic LEDs so they can be used as pixels in display screens. The novel process could allow these tiny light sources to be easily mounted on a range of materials – such as glass, plastic and rubber substrates – for the first time. This breakthrough could lead to affordable and eco-friendly applications, including computer screens and flexible displays, claim the researchers.
LEDs emit light across a narrow band of frequencies when their electrons combine with holes to form “excitons”. Conventional LEDs are made using inorganic materials and are usually created from a stack of thin semiconductor layers that are grown onto circular substrates that are diced up to form thousands of small chips. Blue and green LEDs are made from gallium nitride (GaN) and indium gallium nitride (InGaN) layers, and red equivalents are based on aluminum indium gallium phosphide (AlInGaP).
The bottom layers of these LEDs contain intentional impurities that create an abundance of electrons in this region. Positively charged holes are formed in the top layers by including a dopant and when an appropriate voltage is applied across the device these two carriers are drawn together so that they recombine to emit a photon.
Pros and cons
Inorganic LEDs are bright, reliable and last a long time, which is why they are used as back-lights in a range of applications from watches to advertising boards. The production of inorganic LEDs, however, is laborious because manufacturers must saw up wafers, remove the diodes and then relocate the diodes into specific applications. What is more, the lateral dimensions of LED chips at present can be no smaller than 200 μm, which is too large for many displays.
Organic LEDs, in contrast, are made by sandwiching carbon-based molecules between an indium tin oxide-coated substrate and a metal contact. Applying a voltage across this structure brings electrons from one side of the device together with holes from the other, and the recombination of these carriers generates a photon. In recent years, this process has been used to create arrays of parallel organic LEDs for use in display panels.
Producing displays that feature small inorganic LEDs arranged in parallel is a tougher challenge, but the US team led by John Rogers at the University of Illinois, Urbana-Champaign, has managed to do just that. The hope is that these tiny lights could eventually be produced en mass in parallel to act as the pixels of a display screen, rather than just forming the back-light.
In a small-scale demonstration of the technique, the researchers deposited an aluminium arsenide (AlAs) layer and a red LED onto a gallium arsenide (GaAs) substrate. They then selectively removed parts of the film using photolithography and etching to define square “LED islands” of length 50 μm on this wafer. Subsequent exposure to hydrofluoric acid removes most of the surrounding AlAs layer to leave an array of LEDs that are weakly bound to the substrate.
Printing light
An automated printing tool with a soft stamp picks up an array of these tiny LED chips and deposits them onto a substrate, such as glass, plastic or rubber. A thin metallic mesh on this substrate provides one contact to the LEDs, before a second contact is applied with a lithographic technique to complete the process.
Although the technique can currently be used to make red displays, Rogers now plans to develop full colour displays by working out a way to produce blue and green LEDs as well. “We are preparing a manuscript on that content now,” Rogers told physicsworld.com.
Another potential application is white-light systems for general illumination, which are being developed by a spin-off company, CoolEdge. “We are also exploring flexible and stretchable infra-red and ultra-violet devices for certain applications in biomedicine,” says Rogers.
The researchers reported their work in the latest edition of Science.