A prototype 3D-printed myoelectric prosthetic hand developed in Japan successfully passed a test by an upper-arm amputee, performing a series of intricate finger motions with more than 90% accuracy. The success of this test is an important step forward in the development of more user-friendly, easier to train and less expensive hand prosthetics (Sci. Robot. 10.1126/scirobotics.aaw6339).
Myoelectric hands are externally powered prostheses designed to take advantage of the natural signals generated by muscle contractions. They incorporate electrodes that measure and amplify these muscle signals. The myoelectric signals are then used to activate various functions of the prosthesis that are trained to respond to them.
Hundreds of thousands of upper-arm amputees worldwide could benefit from prosthetic hands with independently operating fingers that can perform a range of motions. Commercially available prosthetic hands with this advanced functionality are expensive to purchase and maintain, and require large training datasets with their user to classify hand and finger movement.
The researchers – from the Graduate School of Engineering of Hiroshima University, the Robot Rehabilitation Center in the Hyogo Institute of Assistive Technology and Kinki Gishi Corporation – have developed a 3D-printed hand with independently operating fingers. The prosthetic hand uses a control system powered by muscle synergy, in which the combined activation of one muscle group – “muscle synergy” – drives one single finger motion, while combined motions are driven by combinations of different muscle synergies.
A microcomputer in the prosthetic hand converts electromyogram (EMG) signals to extract features, classify motion and control movement. Operator motion is predicted from the history of the muscle synergies, and the motion-generation model for the hand’s five fingers is based on an event-driven model. Motion motors operate on information given by forces on the prosthetic, with operational motion estimated by EMG signal processing and biometric control.
Performance testing
One upper-arm amputee who had used a myoelectric prosthesis for 17 years and six able-bodied 23-year old male volunteers participated in performance tests of the new device. The six volunteers were divided into two groups, one that could see how the prosthetic hand responded to their commands and the other blocked from this feedback.
Sitting with their right arms positioned on a table and flexed at a 90° angle, the volunteers performed single motions that included flexing each finger and grasping an object. They also performed five complex motions, which included pinching objects with two and three fingers, making a peace sign, holding up an index finger and giving a thumbs-up sign. All motions were repeated five times for a duration of 10 s each.
The researchers developed a custom-configured forearm socket with embedded EMG electrodes for the amputee participant. Sitting in the same position at a table, he performed four single motions and one combined motion, with each motion task performed twice for 10 s. This participant also used the prosthetic hand to pick up a notebook, a plastic bottle and blocks, for 60 s each.
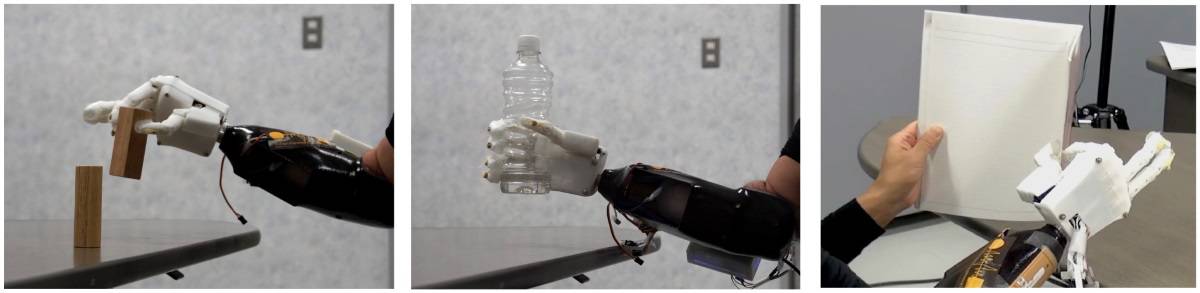
Lead author Akira Furui and colleagues reported that every able-bodied participant performed all finger motions with greater than 90% accuracy. Those who could see the hand motion achieved an average accuracy of 97.3%, compared with 91.7% for the blinded group. The amputee participant achieved a classification accuracy of greater than 89% for both single and combined motions, with an average accuracy of about 92%. “These results indicate that the proposed system can be applied to situations in which actual use of prosthetic hands is likely to occur,” wrote the authors.
The researchers need to refine this prototype so that it can be operated easily over long durations without muscle fatigue, with posture changes and to ensure that classification accuracy of EMG patterns will not decrease. A research priority is to improve the robustness of the EMG pattern classification.
Next, the researchers hope to test the prosthetic hand on multiple amputee participants and develop a formal training programme. They also aim to introduce sensory feedback mechanisms to provide better movement execution and force regulation, ultimately resulting in a practical and intuitively controllable prosthetic hand.