Madison Maxey is the founder and technical lead of LOOMIA, a New York and California-based start-up that designs and manufactures e-textiles for use in wearable technologies, outdoor gear and automotive interiors. She spoke to Margaret Harris about the materials-science challenges of e-textiles and where the industry is heading
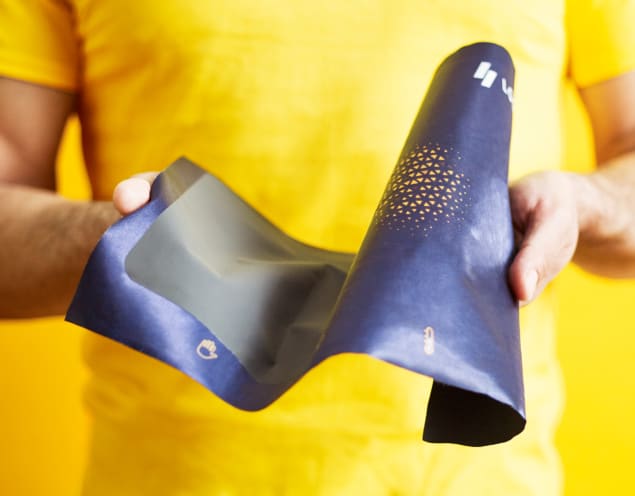
Let’s start with the basics. What are e-textiles?
The term “e-textiles” can refer to either electronic textiles or electrically integrated textiles, but generally they’re a combination of electronics that are meant to be integrated into a textile substrate. The language can be confusing because there are lots of different ways to do it. You can print conductive traces onto a plastic, laminate it to a textile and call that an e-textile, but in that case the circuit itself is not a textile at all. You can also take a conductive thread and knit it into a fabric with conductive traces and call that an e-textile, but that is more textile than it is traditional circuitry. So while the main definition is “electronic textile”, there are lots of different ways to make them, ranging from printed electronics to traditional textile-making techniques.
What are some applications for the types of e-textiles that interest you?
There are quite a few markets that you can apply e-textiles to, but one of the best ways to think about it is that e-textiles are a kind of circuitry that has unique mechanical properties. When you need circuitry that can function in an environment that is flexing around multiple axes; or that can exist on a substrate that can be creased and draped over an object such as a human body; or you need a circuit that spans a large surface area (which can sometimes be hard to achieve with traditional electronics), then an e-textile can be very useful. The applications that interest us are all driven by these mechanical properties.
When it comes to specific industries and use cases, e-textiles can be very useful for garment-based wearables in the medical sector. An example might be devices that are collecting electrocardiography (EKG) or electromyography (EMG) data. One of the big issues for those applications is that if you need to do long-term health monitoring, especially of your heart, you generally have to stick all these electrodes to yourself every day under your clothes, and that encourages people to avoid doing the monitoring. But if you can make those data-collecting devices comfortable and easier for people to wear, then they are more likely to wear them. That’s the general school of thought.
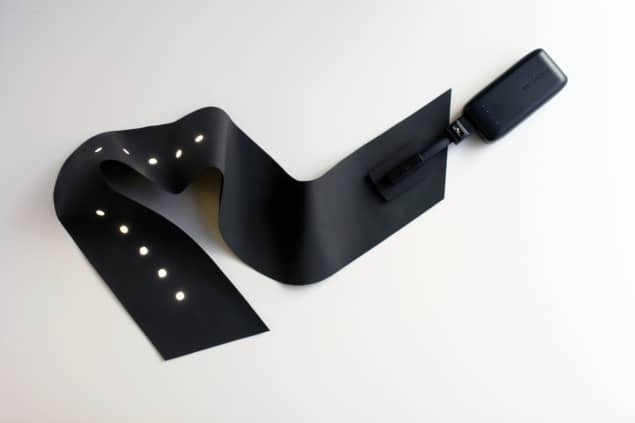
We’re also interested in e-textiles for outdoor gear applications. Here, the guiding principles are heating for comfort, lighting for safety (see photo) and being able to do both of those things in materials that are flat and flexible. An example might be a bicycling uniform, which you’d want to be well-lit for safety, or a tent, where you might want to have heating as well as lighting. A final application that sometimes surprises people is the automotive industry. Some cars already have heated seats, which are wired applications of e-textiles, but you can also have textile-based user interfaces to the car or controls on the dashboard.
What are the technical challenges in making these materials? Presumably they need to be washable…
Oh, definitely. Especially for the garment-based applications. The challenge here is that a washing machine is really, really hard on any material, not just e-textiles. You’re basically submerging something in water and whipping it around at high speeds and agitating it in the presence of a detergent. So when you’re trying to make a circuit washable, you’re trying to make it extremely robust and mechanically stable so that it’s not impacted by the force of the machine – but an e-textile also needs to be flexible and soft, or it won’t work well in a garment. Those two things are fighting against each other, because the more mechanically stable a material is, often the less soft it is. You’re trying to find a balance.
Dry cleaning is also an interesting challenge. Sometimes people think it’s less aggressive, but in fact dry cleaning uses perchloroethylene, which is a chemical that wants to eat away at lots of materials, and especially at lots of materials used for electronic textiles. So it’s not really a good option either.
Producing e-textiles is also a hard challenge. They require a lot of manual labour right now, and there’s not really a super well-known or fool-proof way of making them, like there is for making printed circuit boards (PCBs). If you want a PCB, it’s a lithography process, everybody does pretty much the same thing, and it comes out working every time. But that doesn’t exist for the e-textiles space yet.
What approaches have you used at LOOMIA to try to solve these problems?
One of the main things was to decide which properties we were going to sacrifice. For example, our e-textile is not stretchable. The reason for that is that when a circuit stretches, it often impacts the electrical resistance, and we wanted a textile that was highly conductive, with consistent electrical properties. That meant we had to choose a material that wasn’t stretchable. We tried to refine the list of features down to the ones that mattered most.
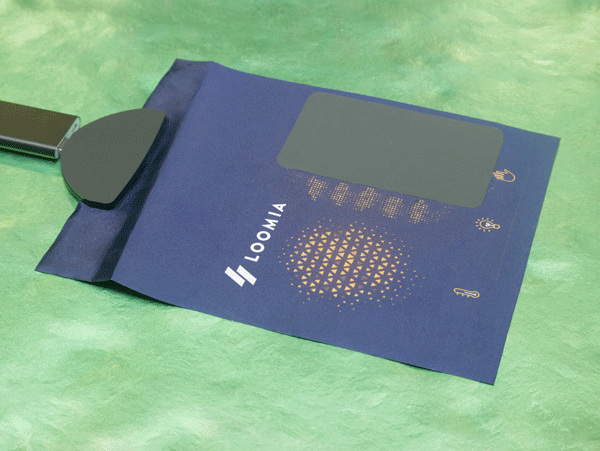
We’ve also developed a manufacturing process that easily translates from prototyping to production. Machines for automated knitting are very expensive, and they require a lot of training to use. They’re incredible if you have that training and money, but we wanted to opt for something that didn’t require as much of either, so that it would be easy to go from prototype to production and back whenever we’re customizing our circuit.
How did you get interested in this field?
My background’s actually in fashion, and I was always really interested in how garments were put together. Then I needed a website to show off my work, so I started taking programming classes, and I discovered that it’s a similar process: you have these pieces of code that you put together to make a website, just like you have pattern pieces that you put together to make a garment. That got me interested in software and the tech world, and I started doing artist residencies that involved a lot of hardware projects.
This was at the beginning of the 2010s, and a lot of the things I ended up doing were, in essence, really early applications of electronic textiles. I saw that there was a need for a material that would enable wearable electronic textiles to be scaled up, so that they became real products rather than prototypes or proofs-of-concept. That was how I started down the research track to our main product, the LOOMIA Electronic Layer, which I developed in collaboration with our chief technology officer, Ezgi Ucar (see photo below). I was doing an artist residency for a software company, Autodesk, at the time, looking particularly at digital fabrication techniques for electronic textiles, which involve mixing up conductive inks. And when I learned there were some companies interested in these inks, I thought, wow, maybe there’s potential here.
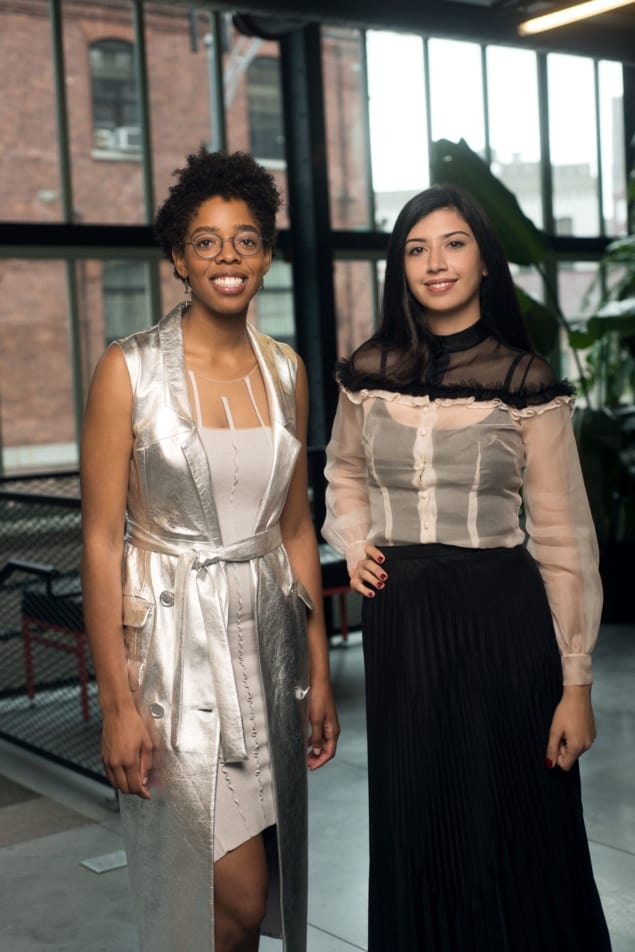
What made you decide to start your own company?
I am very interested in materials as enabling technologies, and it just seemed like the most interesting thing I could do was to try and make an enabling technology of my own. It helped that e-textiles is an emerging industry where a unique perspective can be an asset – it’s not like the software industry, for example, where you really need to be an expert to do anything useful. I’d also worked a little bit in fashion, and I wasn’t excited about continuing down that path – I enjoy working in the tech industry and on tech-related projects much more. So being able to work at the intersection of textiles, materials and technologies was a good fit for my interests.
How did you get funding?
In 2013, I did a Thiel Fellowship, which is a programme that gives young people money to build new things instead of going to university to study. By the time my fellowship ended, I had worked on wearable technologies for some pretty big-name companies, and that background, plus doing a fellowship that venture capitalists recognize as a good source of talent, meant that people were willing to take meetings with me when I started asking for funding. It also helped that I started LOOMIA (which was originally a studio called The Crated – we changed the name when we got investors) at pretty much the peak of the “hype cycle” for wearable tech, so people were really interested in making investments. We didn’t raise a tonne of money, but it was definitely something I couldn’t have funded on my own.
Sometimes, having too many networking opportunities can be distracting.
Madison Maxey
Speaking of the hype cycle, what do you think is coming up next for e-textiles as an industry?
I’ve seen reports suggesting that e-textiles are heading towards the “plateau of productivity” part of the hype cycle, and I personally think that’s true. The applications we’re seeing now are much more functional. They have good ideas behind them. The people doing them seem like they have a plan. One of the things we always ask is, why do you need e-textiles? Why can’t you use a standard circuit on a PCB? And the use cases we’re looking at now really do benefit from having an electronic textile inside the system, so I feel we’re getting to that productive plateau. At least, I’m hoping we are, because I’ve kind of made my bet on this space!
Looking back to when you started the business, what do you know now that you wish you’d known then?
I wish I would have known more about how to manage a start-up, how to hire the right people and how to make good financial decisions. Sometimes, the things you’re encouraged to do by the investment community aren’t the most important things to be doing in the early days of a start-up, and I wish I would have known that earlier.
One example is that people tell you to network – go to lots of events, meet lots of people. And yes, when you’re actively raising money, it does help to meet people and be at the top of their minds. But in general, you should focus on the product or technology you’re developing, because that’s the way the work gets done. Sometimes, having too many networking opportunities can be distracting.
The other example is that sometimes you’ll be encouraged to hire the most senior people you can find. The problem with that is that working on a team of three or four people really isn’t for everyone. Someone who’s very senior and very experienced may be used to working with a lot of infrastructure, and in a start-up they won’t have that. So I think you should look for people who are very motivated and self-directed as well as talented. It’s very easy to go for the vanity factor of saying, “Oh, this person used to work at Google, and now they’re here.” That’s the kind of thing investors want you to have. But I don’t think it’s necessarily an indicator that that person is the best for your team.
As an artist and textile designer, what’s on your materials wish list? What properties would be really amazing for the work you do?
Silicone and thermoplastic polyurethanes (TPUs) are some of the best materials for insulating electronic textiles, and TPUs in particular might help with making e-textiles washable. A TPU with a really strong adhesive that helps hold things in place mechanically during a washing process would be helpful for us. In addition, we’re always looking for good epoxies and conductive glues that combine elasticity with mechanical strength. Finally, we’ve recently been looking for piezoelectric sheets of material, which so far we’ve only been able to find in one place. So we’d be pretty interested in hearing about that if any materials people have something they’re working on.