
Graphite films can shield electronic devices from electromagnetic (EM) radiation, but current techniques for manufacturing them take several hours and require processing temperatures of around 3000 °C. A team of researchers from the Shenyang National Laboratory for Materials Science at the Chinese Academy of Sciences has now demonstrated an alternative way of making high-quality graphite films in just a few seconds by quenching hot strips of nickel foil in ethanol. The growth rate for these films is more than two orders of magnitude higher than in existing methods, and the films’ electrical conductivity and mechanical strength are on par with those of films made using chemical vapour deposition (CVD).
All electronic devices produce some EM radiation. As devices become ever smaller and operate at higher and higher frequencies, the potential for electromagnetic interference (EMI) grows, and can adversely affect the performance of the device as well as that of nearby electronic systems.
Graphite, an allotrope of carbon built from layers of graphene held together by van der Waals forces, has a number of remarkable electrical, thermal and mechanical properties that make it an effective shield against EMI. However, it needs to be in the form of a very thin film for it to have a high electrical conductivity, which is important for practical EMI applications because it means that the material can reflect and absorb EM waves as they interact with the charge carriers inside it.
At present, the main ways of making graphite film involve either high-temperature pyrolysis of aromatic polymers or stacking up graphene (GO) oxide or graphene nanosheets layer by layer. Both processes require high temperatures of around 3000 °C and processing times of an hour. In CVD, the required temperatures are lower (between 700 to 1300 °C), but it takes a few hours to make nanometre-thick films, even in vacuum.
High-performance films
A team led by Wencai Ren has now produced high-quality graphite film tens of nanometres thick within a few seconds by heating nickel foil to 1200 °C in an argon atmosphere and then rapidly immersing this foil in ethanol at 0 °C. The carbon atoms produced from the decomposition of ethanol diffuse and dissolve into the nickel thanks to the metal’s high carbon solubility (0.4 wt% at 1200 °C). Because this carbon solubility greatly decreases at low temperature, the carbon atoms subsequently segregate and precipitate from the nickel surface during quenching, producing a thick graphite film. The researchers report that the excellent catalytic activity of nickel also aids the formation of highly crystalline graphite.
Using a combination of high-resolution transmission microscopy, X-ray diffraction and Raman spectroscopy, Ren and colleagues found that the graphite they produced was highly crystalline over large areas, well layered and contained no visible defects. The electron conductivity of the film was as high as 2.6 x 105 S/m, similar to films grown by CVD or high-temperature techniques and pressing of GO/graphene films.
To test how well the material could block EM radiation, the team transferred films with a surface area of 600 mm2 onto substrates made of polyethylene terephthalate (PET). They then measured the film’s EMI shielding effectiveness (SE) in the X-band frequency range, between 8.2 and 12.4 GHz. They found an EMI SE of more than 14.92 dB for a film approximately 77 nm thick. This value increases to more than 20 dB (the minimum value required for commercial applications) in the entire X-band when they stacked more films together. Indeed, a film containing five pieces of stacked graphite films (around 385 nm thick in total) has an EMI SE of around 28 dB, which means that the material can block 99.84% of incident radiation. Overall, the team measured an EMI shielding of 481,000 dB/cm2/g across the X-band, outperforming all previously reported synthetic materials.
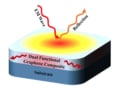
Cool graphene composites block EM radiation
Thinnest among reported shielding materials
The researchers say that to the best of their knowledge, their graphite film is the thinnest among reported shielding materials, with an EMI shielding performance that can satisfy the requirement for commercial applications. Its mechanical properties are also favourable. The material’s fracture strength of roughly 110 MPa (extracted from stress–strain curves of the material placed on a polycarbonate support) is higher than that of graphite films grown by the other methods. The film is flexible, too, and can be bent 1000 times with a bending radius of 5 mm without losing its EMI shielding properties. It is also thermally stable up to 550 °C. The team believes that these and other properties mean that it could be used as an ultrathin, lightweight, flexible and effective EMI shielding material for applications in many areas, including aerospace as well as electronics and optoelectronics.
The work is detailed in ACS Nano.