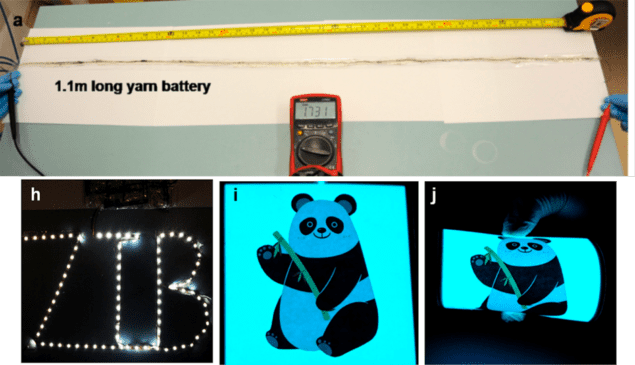
Researchers have produced fine, thread-like “yarn” batteries using a scalable carbon nanotube (CNT) based roll manufacturing processes. The batteries have specific capacities competitive with Li-ion technology, can be knitted into fabric, folded, stretched and washed, offering promising power storage for low-profile applications.
Lithium-ion batteries offer power densities far in excess of previous rechargeable battery types, like nickel-metal hydride and nickel-cadmium, allowing portable electronics to become ever more sophisticated and power-hungry. Their power density however comes at the cost of manufacturing ease and safety, so they are not appropriate for all applications. The development of new battery types is accelerating with the aim of diversifying the power storage options available for technological applications with different needs.
For a long time primary (non-rechargeable) batteries have relied on the electrochemistry of Zn anodes and MnO2 cathodes, but experts had considered it impossible to recharge these cells. However, through studies of the cathode structure and choice of electrolyte researchers have recently achieved high reversible capacities with Zn and MnO2. Using these recent developments researchers in Hong Kong have developed a scalable method to produce highly durable, waterproof, high-capacity cells in the form of knittable yarn, which may have extensive applications in flexible, transparent, or wearable electronics.
Spinning an electric yarn
The process begins with CNT fibres for high strength current collectors. On these the Hong Kong research team deposits cathode and anode materials using roll-dipping and electrodeposition processes respectively: The active cathode material consists of MnO2 nanorods precipitated onto the surfaces of the multiwalled CNTs, and Zn metal is electroplated onto the anode. They then wound the ~100 μm diameter cathode and anode fibres around an elastic thread and coated them with a polymer hydrogel electrolyte – a highly porous cross-linked polyacrylamide impregnated with an aqueous ZnSO4 and MnSO4 solution. They then encapsulate the assembly in a silicone sheath to keep it all together and watertight.
In their report Chunyi Zhi and co-authors demonstrated the scalability of their process by manufacturing a 1.1 m long cell. They were able to demonstrate stable electrochemical cycling while bending, knotting, and stretching the cells. In addition, under rapid cycling conditions (10 min dis/charge) the cells retained 98.5% of their specific capacity after 500 cycles.
The physical robustness and pliability of these cells makes them suited to unique niche applications, such as medical implants, and flexible electronic devices. Their low toxicity, low cost and good safety characteristics may also make them excellent candidates for power sources for ubiquitous wearable electronic devices.
Full details are available at ACS Nano 10.1021/acsnano.7b09003.