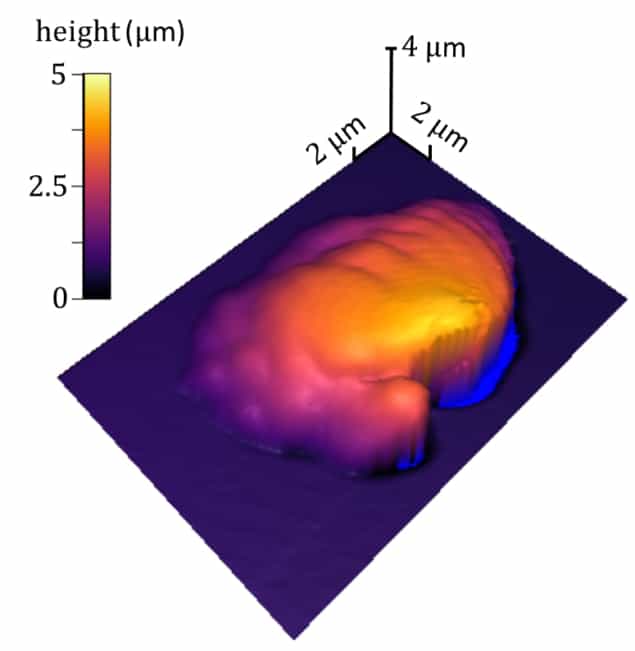
Materials that polymerize when exposed to light can be used in additive manufacturing (3D printing), an up and coming technique to fabricate structures for use in applications as diverse as low-cost rapid prototyping and tissue engineering. The problem is that it is difficult to measure how the mechanical and rheological properties of these materials change during polymerization, especially at the extremely short time- and length scales at which they take place. These changes affect the properties of the finished printed structure. A team of researchers at the National Institute of Standards and Technology (NIST) in the US has now developed a new atomic force microscope technique dubbed sample-coupled-resonance photorheology (SCRPR) that could do just this.
“We can sense rapid, local changes in material properties at length scales of 10 nm over time scales less than 100 microseconds, which were previously impossible to study in situ,” explains lead author of this study Callie Fiedler-Higgins of the Applied Chemicals and Materials Division at NIST. “Our technique allows us to investigate fundamental processes that require this kind of spatiotemporal resolution to accurately probe.”
Micro-heterogeneities
To build a structure using additive manufacturing (AM), 2D “slices” of the final desired 3D structure are sequentially built up using software. During fabrication the layered process introduces microscale anisotropic heterogeneities in the chemical, thermal and mechanical properties of the material. These changes are inherent to the printing process and can even result in the catastrophic failure of an as-printed material, says Fiedler-Higgins.
The techniques usually employed to characterize as-printed AM objects, such as tensile and compressive stress testing, are not ideal since they inaccurately assume that the 3D structure has uniform properties throughout, she explains. What is more, techniques such as oscillating rheometry work on timescales of seconds, whereas polymerization during AM takes place in just milliseconds or less.
SCRPR senses local changes at process-relevant length and time-scales
The new SCRPR technique overcomes these problems since it can measure rheological changes during photopolymerization with millisecond temporal resolution and at subvoxel length scales, where a voxel is the smallest AM printing unit. This is thousands of times smaller-scale and faster than bulk measurement techniques.
“SCRPR is the first technique of its kind to truly sense the local changes at process-relevant length and time scales,” Fiedler-Higgins tells Physics World. “Other techniques must sacrifice either spatial or temporal resolution to maximize their sensing capabilities.”
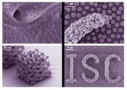
3D printing goes micro
Atomic force microscopy is a routinely-used ultrahigh-resolution technique that can image extremely small objects, even down to single atoms. It works by sensing the topography of a sample as it scans across it thanks to a sharp-tipped probe (the cantilever) that touches the surface of the sample.
Fiedler-Higgins and colleagues adapted a commercial AFM so that they could use its exciting (UV) laser to initiate photopolymerization at or near the contact between the tip and sample. This built-in laser also allows them to precisely synchronize when polymerization starts and when AFM read out begins. They combined AFM with stereolithography, which is the use of light to pattern photoreactive materials.
The researchers measured two values, the resonance frequency (the frequency of maximum vibration amplitude) and quality factor (an indicator of energy dissipation) of the AFM probe at one location in space during a fixed time period. They tracked changes in these values throughout the polymerization process and then analysed this data with mathematical models to determine material properties such as stiffness and damping.
They tested their technique first on a sequential cure polymer (SCP) that goes from being a rubber to a glass when irradiated with 405 nm light. This material was used as a proof-of-concept since it does not undergo a liquid-to-solid transition, but its rheological properties still change quickly. They then measured the photopolymerization response for the SCP by applying four different laser exposure powers during different times. The response time of the cantilever is faster than 50 microseconds during all measurements.
The team then tested the technique on a commercial SLA resin and found that it could successfully characterize the photorheology of the liquid-to-solid cure of this polymer, which takes place in just 12 milliseconds.
Towards commercial collaborations
“We hope our technique will help resin manufacturers to develop new classes of fast polymerizing resins and help 3D printer manufactures to design optimized print patterns for improved part performance,” says project leader and co-author Jason Killgore also of the Applied Chemicals and Materials Division at NIST. “After presenting our research at both technical and industry focused conferences, we’ve come to realize the utility of SCRPR to study a variety of fast-polymerizing materials ranging from those for dentistry to those for large-scale manufacturing.”
The researchers, reporting their work in Small Methods 10.1002/smtd.201800275, say that they would now like to develop a new system in which they have more control over exposure patterns, and employ light sources that better mimic typical stereolithography printing. “There is also a huge modelling component that we need to address to ensure we can measure accurate and precise materials properties, such as viscosity and storage modulus, within the dynamically changing material,” adds Killgore.