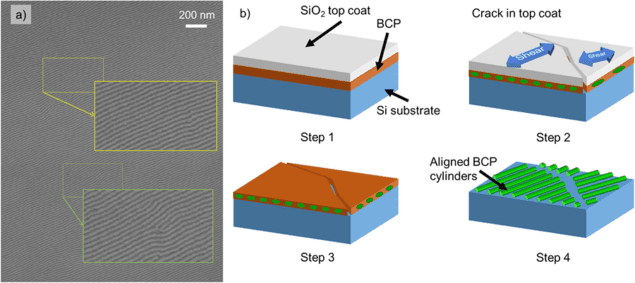
The design of block copolymers that self-assemble into various shapes has proved an attractive approach for nanoscale periodic patterning that can cover large areas. However, various approaches that aim to control the alignment of these patterns often require several hours of annealing and can introduce defects, as well as limiting the block copolymer materials that can be used. Now, researchers have shown that a mismatch in the coefficient of thermal expansion in the block copolymer substrate and an applied top coat can provide a shear stress that aligns patterns over large areas with few defects after mere minutes of annealing.
Order means little without control. When Sam Nicaise – now a postdoctoral researcher at the University of Pennsylvania – and colleagues led by Karl Berggren at MIT in the US started looking at ways to control block-copolymer self-assembly, they joined a throng of researchers who had tried working with viscous flow, electromagnetic fields and gradient annealing with similar aims.
Block copolymers combine two or more different types of organic string molecules. In a way that resembles the phase separation of immiscible oil and water, block copolymers can microphase separate, leading to the self-assembly of nanostructures.
“We had a hunch – we thought maybe we could provide shear stress with a top coat,” says Nicaise. Conventional block-copolymer films are bare but research was starting to suggest that adding a top layer might make it possible to make the self-assembled patterns align. Nicaise and his colleagues thought they might be able to take the approach further, not just asserting alignment but controlling the direction of alignment as well.
Other groups had added oils and organic top coatings to the block copolymers. “If you come from a chemical engineering and rheological perspective that looks at the flows as a function of time and temperature, soft top coats are the first step,” suggests Nicaise. “We come from electrical engineering – so we come from a different perspective.”
Instead he and his colleagues opted for inorganic silicon dioxide, which brought two advantages. Silicon dioxide can tolerate higher temperatures, so by going to higher temperatures they could increase whatever shear stress is caused by a mismatch in the coefficient of thermal expansion between the layers. It also makes the structures compatible with industry processes, which generally use high temperatures.
The hunch paid off. The top coat cracked, but the researchers found that shear stresses exerted on the block copolymer followed the cracks and the alignment followed the direction of the stress. As a result, cracks could be artificially scribed on the surface to control the direction of alignment.
The stresses generated exceeded 100 kPa – orders of magnitude larger than those required for the shear alignment of block copolymers. In addition, the MIT researchers only annealed their films for 10 minutes. Other approaches to aligning block copolymer self-assembly require hours of annealing – timescales that can cool industry interest. As Nicaise puts it, “To see it ordered after annealing in just a few minutes – that’s really exciting.”
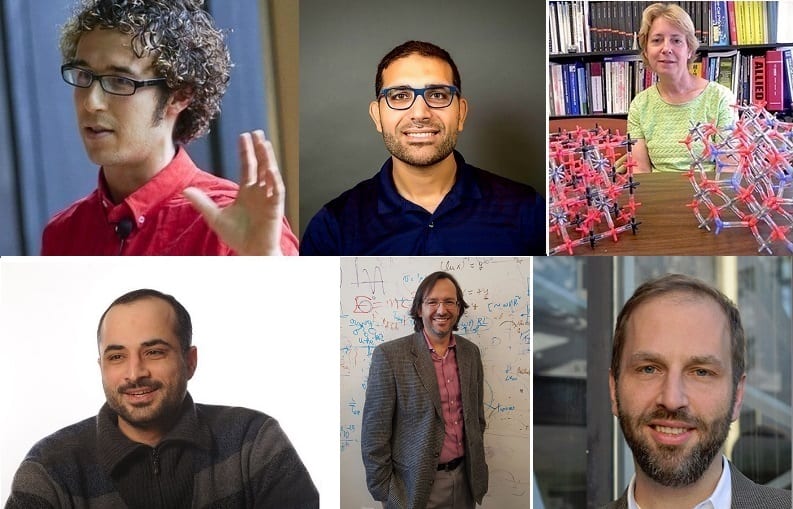
Cheap models
The most common theoretical models for block-copolymer systems are either field-based or particle-based, which can be computationally expensive and time-consuming to calculate. Instead, the MIT researchers used a larger numerical approach based on finite elements, and this is able to capture the stresses inside the system.
Nicaise emphasises how useful the simplicity of their viscoelastic analysis is. His co-worker from the Alexander-Katz Group at MIT, Karim Gadelrab, who worked on the modelling side of the project, is enthusiastic about how much more quickly it can run simulations to capture the temperature-dependent mechanical properties of the block copolymer film and inorganic layers. “It gives an example of how researchers can use a less expensive technique to look at what patterns they can get with the block copolymers,” says Nicaise.
Opportunities for further development
As someone who has been looking at array fabrication and these kinds of films for nearly a decade, Nicaise sees a lot of room for improving the technique so that the alignment covers larger areas. At present, the alignment is best close to the cracks and the film remains well aligned within around 100 micrometres of the crack. In this respect it has potential for being a useful local patterning approach. “I am hoping some researchers can pair it with other techniques for shear alignment such as laser annealing for local annealing,” adds Nicaise.
That said, there are other advantages. While viscous flow and electromagnetic field approaches to impose alignment on block copolymer self-assembly are based on the properties of the polymers themselves – such as the dielectric coefficient or magnetic permeability – the shear stress from the top coat stems from the materials of the top coat and substrate, allowing more freedom in the polymers that can be used.
Nicaise suggests that fabricating chips with features below 10 nm is a possible application of the approach. In addition, by leaving the top coat on, it may be possible to stack several layers of scribed films and anneal them in one go, providing an approach to accompany other methods to produce 3D structures. There is also the possibility of working with how the block copolymer self-assembly interacts with nanolithographically patterned topographical templates.
Full details are reported in Nano Futures.