Frazer-Nash Manufacturing is a trusted partner for industry and scientific customers seeking precision engineering services and low-volume production of specialist parts
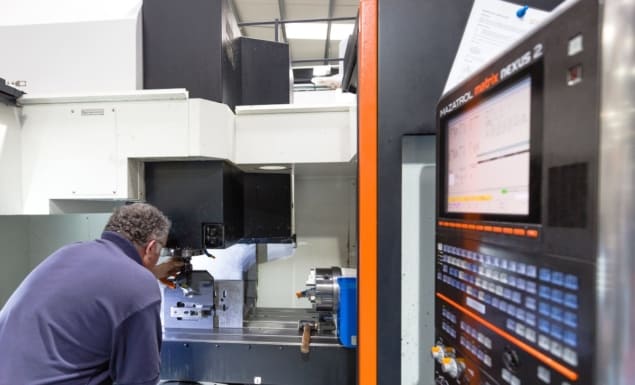
Frazer-Nash Manufacturing is a company that’s always been intent on playing to its strengths. In this way, the specialist UK-based workshop has carved out a niche by providing design, precision engineering and low-volume manufacturing services to a range of international customers – most notably in the food processing and space industries. Now, diversification is on the agenda and Frazer-Nash is eyeing long-term growth opportunities as a supplier of custom engineering and manufacturing services to the scientific research community – whether that’s “big science” facilities, academic research groups or technology start-up ventures.
Put simply, Frazer-Nash is putting itself out there, supporting researchers in the physical sciences with custom parts requirements that cannot be sourced off-the-shelf or from a standard product range. The Hampshire-based outfit offers a broad portfolio of precision manufacturing capabilities – traditional milling, turning, grinding as well as wire electrical-discharge machining (EDM), surface treatments and 3D printing of custom metal parts – and, as such, is able to deliver one-off projects, prototype development and small-volume production runs.
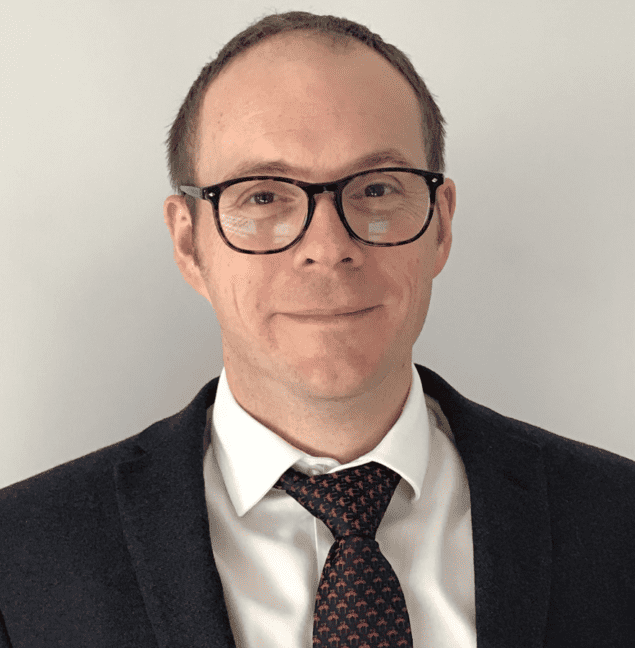
“We specialize in low-volume manufacturing for customers with high-quality expectations,” explains Paul Mortlock, managing director of Frazer-Nash. Whether it’s a complex metal part or something more straightforward, the formula remains the same: a rigorous approach to materials traceability (from raw material to finished part), work-in-progress product inspection, and delivery versus customer specifications and tolerances.
“We handle everything in-house,” Mortlock adds, “and that gives us 100% control over our production process and the quality of our final output.” Underpinning that operational model, the company is fully certified to the ISO9001:2015 and AS9100 Rev D quality-assurance standards as well as the ISO14001 standard for environmental management.
Pivoting for growth
Beyond the day-to-day operation, the strategic priorities are clear. Frazer-Nash’s manufacturing capabilities are characterized by a relentless focus on continuous improvement that spans materials quality, digital inventory management and ongoing investment in new machines, control software and staff training. “The whole ethos here is based on long-term capital investment and year-on-year improvement across our processes, our people and our workflows,” says Mortlock.
That mindset is mandatory given the exacting requirements of Frazer-Nash customers. A case in point is the food processing industry, for which Frazer-Nash produces a range of proprietary equipment – extruder heads, cutting systems, filling systems and the like. “Our food-industry solutions conform to the latest international food-safety specifications with open-access structures, sloping surfaces and crevice-free design,” explains Mortlock. “We also ensure that the correct grades of stainless steel or other approved materials are used for our EU and US customers.”
Yet while the food industry will remain a core revenue stream, Mortlock and his colleagues are increasingly pivoting their business-development efforts towards the scientific research market and the space industry. There’s plenty of momentum already, with Frazer-Nash routinely providing specialist metal parts to satellite manufacturers and rocket-engine developers – the likes of Skyrora and Reaction Engines in the UK, for example – while also making significant inroads with research customers across the physical sciences. The latter include big-science facilities like CERN, the particle physics laboratory in Geneva, and ITER, the next-generation fusion research facility in southern France, as well as smaller academic groups at the University of Southampton and the University of Surrey in the UK.
“They all need a reliable, trusted partner to make their system parts,” explains Mortlock. “We’re providing vacuum chambers, waveguide ports, beam targets and pressure vessels – typically metal parts and systems with demanding requirements for cleanliness, dimensional tolerances and high- or ultrahigh-vacuum capabilities.”
It’s all about dialogue
While every project is unique, Frazer-Nash’s research customers invariably kick off with a variation on the same theme: “This is what we want – can you help us make it?” From that staring point, the requirements-gathering evolves into a granular dialogue between supplier and customer, covering off key metrics like manufacturability, cost, performance, reliability, even materials.
To a large extent, it’s then about prioritizing tolerances against those metrics – which ones matter the most. The same goes for materials specifications, with the choice of US or EU-grade steels, for example, often making a big difference to product lead-times. “Generally we’ll offer advice on manufacturing,” notes Mortlock, “but we don’t tend to be involved with design of the customer’s parts. They are the design authority.”
Even so, all customers get to tap a deep seam of accumulated and learned experience – a result of Frazer-Nash successfully tackling all sorts of complex manufacturing challenges across the food and aerospace industries over the years. This “assimilated savvy“ could be as fundamental as the metallurgy – whether a generic stock material or a proprietary grade of stainless steel will deliver the required performance – or something more specific – such as the finishing and surface treatment needed if a part is destined for an abrasive environment.
“In a lot of cases,” says Mortlock, “customers are coming to us with a v1.0 prototype and they want an enhanced version that’s built to last. Our task is to make that part more reliable, more robust and more readily manufacturable.”
The answers, inevitably, lie in the technical capability and domain-knowledge of the Frazer-Nash engineering team. With this in mind, the company’s long-term investment programme doesn’t just cover plant and machinery, it prioritizes training, development, staff progression and, crucially, retention. The Frazer-Nash wellness programme is a case in point, with even a consultant dietician on hand to advise staff on all aspects of their nutrition, sleep and exercise.
“This is a high-performing team of engineers, technicians and support staff and we take a holistic approach to their personal development and welfare,” Mortlock concludes. “After all, they’re why we don’t just promise high-dependability in low-volume manufacturing – we deliver.”
Frazer-Nash Manufacturing: built to last
While its commercial focus today is realigning towards customers in scientific research and the space industry, Frazer-Nash Manufacturing can trace a diverse legacy of engineering innovation that stretches back more than a century.
- In 1910, English mechanical engineer and designer Archibald Frazer-Nash jointly developed a lightweight automobile, the GN Cycle Car.
- Some 12 years later, the British inventor set up the Frazer-Nash sports car company to develop a successor to the GN.
- Various Frazer-Nash models were introduced over the following decades, creating a classic sports car marque that’s still admired around the world.
- In 1929, Frazer-Nash turned his attention to other areas of engineering, setting up a separate company to service the needs of the emerging commercial and military aerospace industry.
- Further diversification followed in the second half of the 20th century, with Frazer-Nash businesses expanding into a wide range of sectors, including postal machines, special-purpose equipment and consultancy services.
- In 1990, the wider Frazer-Nash group was rationalized into several smaller specialist companies, with Frazer-Nash Manufacturing comprising a significant portion of the manufacturing and design departments of the former group.
- In 2011, Frazer-Nash Manufacturing moved to its current production facility in Petersfield, Hampshire.
- The company’s workshop plant includes CNC milling machines (five-axis, four-axis and three-axis); CNC turning and mill turn machines; wire EDM systems; and an additive manufacturing system.