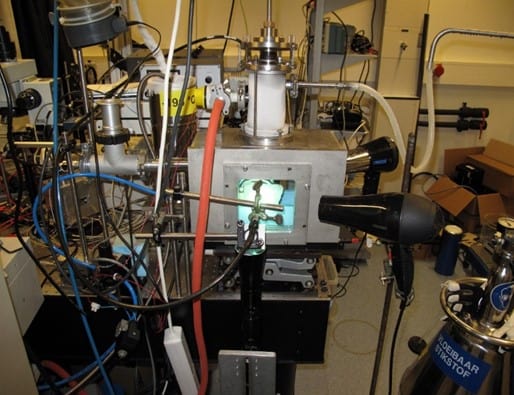
Making hot stuff very cold – and doing so reliably and repeatably – is a tricky business. Now, researchers in the Netherlands have developed a better understanding of a technique called cryogenic spray cooling – which is fast emerging as a commercial cooling method.
Cryogenic spray cooling works by impacting drops of low-temperature fluids (such as liquid nitrogen) on solid surfaces, with the latent heat of the liquid-vapour phase transition delivering the temperature control. The technique has a diverse range of industrial and biomedical applications, among them high-speed materials processing of machine tools and parts, freezing of food products for long-term preservation, and direct-spray cryotherapy of premalignant and cancerous lesions in the oesophagus.
Despite its apparent simplicity, the underlying mechanisms of cryogenic spray-cooling have hitherto remained elusive, with engineers often forced to adopt costly and time-consuming trial-and-error methods to optimize their freezing apparatus and processes. Now, however, a team of scientists at the University of Twente, has gained important insights into the process by studying the fundamental physics of droplet–surface interactions at cryogenic temperatures
“The cooling performance depends on a number of parameters: the size of the droplets, the velocity of the droplets, the angle of impact, as well as the physical properties of the cryogenic fluid and the material to be cooled,” explains Srinivas Vanapalli, who heads up the research in Twente’s Applied Thermal Sciences Laboratory.
Dynamic droplets
Vanapalli and his colleagues Thomas Nes (now at CERN) and Michiel van Limbeek (now at the Max Planck Institute for Dynamics and Self-Organization in Göttingen) looked at an intriguing phenomenon known as the Leidenfrost effect, whereby fluid droplets float above a hot solid surface. The droplets are held up by the vapour they emit– the so-called Leidenfrost boiling regime. The Leidenfrost effect is highly undesirable in spray-cooling systems because the vapour forms an isolating layer that prevents effective heat transfer between the solid and the droplet.
To study the droplet–surface behaviour up close, the researchers dropped a single liquid-nitrogen drop on a smooth sapphire prism and followed its progress from below using high-speed, frustrated total-internal-reflection (TIR) imaging. “In these cryogenic conditions, the prism behaves as a perfect thermal conductor,” says Vanapalli, “while its transparency enables us to study the contact behaviour during the impact and the spreading phase of the drop.”
By varying the drop impact velocity and target temperature, the team was able to map the boiling behaviour in a phase diagram. What is more, by combining single-drop measurements with studies of a continuous stream of liquid-nitrogen droplets, it was possible to correlate the cooling rate with the wetting behaviour of a single drop – revealing good agreement between the phase diagram and the various cooling curves (as well as with the behaviours previously observed for non-cryogenic liquids in spray-cooling applications).
Impact velocity
The team’s studies – using a single droplet as a model system and scaling to a stream of droplets – show that the cooling power is proportional to the impact velocity of the droplets in the Leidenfrost boiling regime. Careful analysis of the spreading behaviour of the liquid-nitrogen droplets also reveals a highly counterintuitive finding.
Specifically, for all surface temperatures in the contact boiling regime (when the droplets make good contact with the solid and bubbles nucleate at the liquid–solid interface), the conductive contribution to cooling exceeds that from evaporation. Since the role of evaporation scales with the latent heat, this behaviour is likely to be more pronounced for polar liquids such as water, in which the latent heat of vaporization is an order of magnitude larger than for liquid nitrogen.
Taken together, these insights have significant implications for understanding the range of heat-transfer mechanisms at play in a cryogenic spray-cooling system. “When we understand the fundamental processes,” Vanapalli concludes, “we can develop a physics-based model to predict the heat-transfer rate, providing application engineers with a toolkit to design and optimize the spray-cooling system for their specific process. That’s pretty cool, if you’ll pardon the pun.”
The research is sponsored by Dutch funding agency NWO-TTW within the CryoOn project and will be described in a upcoming paper in the International Journal of Heat and Mass Transfer.