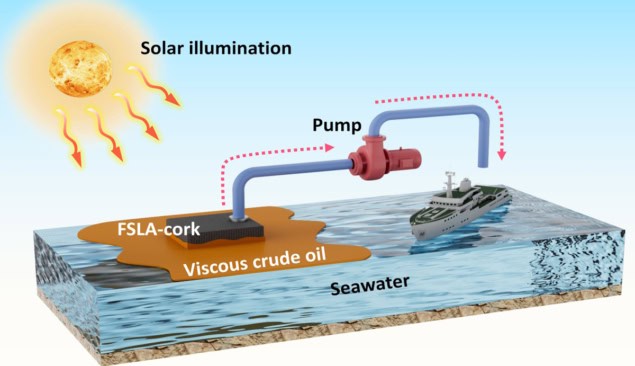
New research suggests that laser-treated cork could be used to tackle crude oil spills. In a study published in Applied Physics Letters, researchers from China and Israel found that femtosecond laser processing alters the surface structure of cork so that it heats rapidly in sunlight and absorbs oil.
Oil spills are ecological disasters that wreak havoc on marine ecosystems, with devastating, long lasting effects on marine animals and their habitats. Oil spill cleanup also presents a major technical challenge.
There’s a lack of effective strategies for clearing water contaminated with high-viscosity oil. Various techniques are employed, such as physically skimming the crude oil off the surface, use of chemical dispersants and even setting the oil alight, but these are often expensive with low efficacy and can cause secondary pollution. Alternative, environmentally friendly solutions are needed.
The authors of the latest research stumbled upon cork as a possible material for cleaning up oil spills by accident.
“In a different laser experiment, we accidentally found that the wettability of the cork processed using a laser changed significantly, gaining superhydrophobic (water-repelling) and superoleophilic (oil-attracting) properties,” says first author Yuchun He, a physicist at Central South University, China, in a press statement.
Following this discovery, the researchers wondered whether, as a porous material, cork could be used to suck up oil. They also found that after femtosecond laser processing, the surface of the cork became very dark, “which made us realize that it might be an excellent material for photothermal conversion,” He explains.
By absorbing energy from sunlight and heating the crude oil, the scientists hypothesized that the black cork would lower the oil’s viscosity, making it easier to absorb.
To characterize the properties of the femtosecond laser-processed cork, the team used scanning electron and confocal laser scanning microscopy. Their analysis showed that while untreated cork had an uneven honeycomb-like surface structure, the laser-processed cork was covered in a regular, striped arrangement of micro-scale grooves, scattered with nanoparticles.
The microscopy studies also showed that the laser-processed cork contained a higher proportion of carbon than untreated cork. This carbonization process occurs when heat from the laser breaks down long-chain cellulose molecules and releases carbon oxides as gas, reducing the cork’s relative oxygen content.
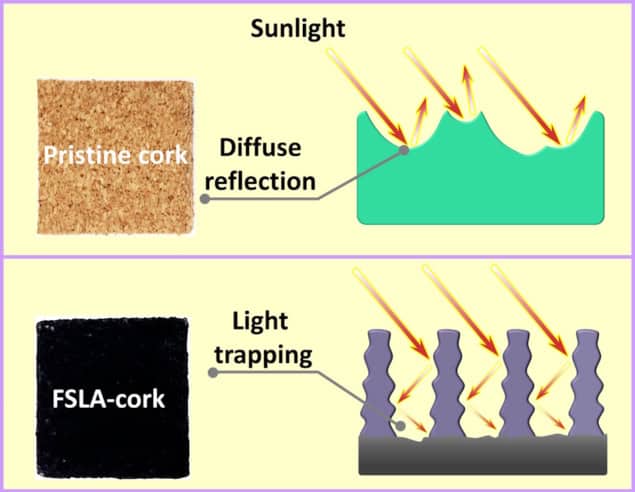
Tests showed that the laser-treated cork had an extremely high solar absorption rate, absorbing more than 90% of light and reflecting less than 10%. Under simulated sunlight, the processed cork hit temperatures of 63°C after 120 s, while untreated cork rose to only 50°C. The laser-treated cork was also found to heat rapidly, reaching 50°C within 15–30 s.
When the researchers tested how well cork absorbed oil, they found that in the dark, the performance of laser-processed and untreated cork was similar, with crude oil gradually infiltrating over 45 min. Under light exposure, however, similar samples of laser-treated cork became saturated with oil within 2 min, while 10 min was needed for complete infiltration of unprocessed cork.
The team says that the nanoscale grooves and an increased surface area on the carbonized, laser-treated cork trap light. This causes the cork to rapidly heat in sunlight and heat nearby oil, reducing its high viscosity. The processed cork’s superoleophilic properties, linked to the changed surface structure and carbonization, then come into play, enabling the cork to suck up the more fluid oil while repelling water.
Cork comes from the bark of cork oak trees. As it is a renewable material that the trees can replace after harvesting, the researchers say it would be a sustainable, inexpensive and environmentally friendly material to use for cleaning up oil spills.
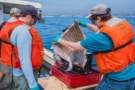
‘Oleo Sponge’ mops up oil spills
They propose that a pump connected to an oil tanker could be used to suck the crude oil out of cork as it is absorbed from the seawater. In laboratory experiments, the team demonstrated that a small-scale version of this setup could successfully extract oil from seawater in a Petri dish.
“Oil recovery is a complex and systematic task, and participating in oil recovery throughout its entire life cycle is our goal,” He says. “The next step is to prepare electrothermal materials using polyurethane foam as the skeleton for oil adsorption, combining photothermal and electrothermal techniques to form an all-weather oil recovery system.”