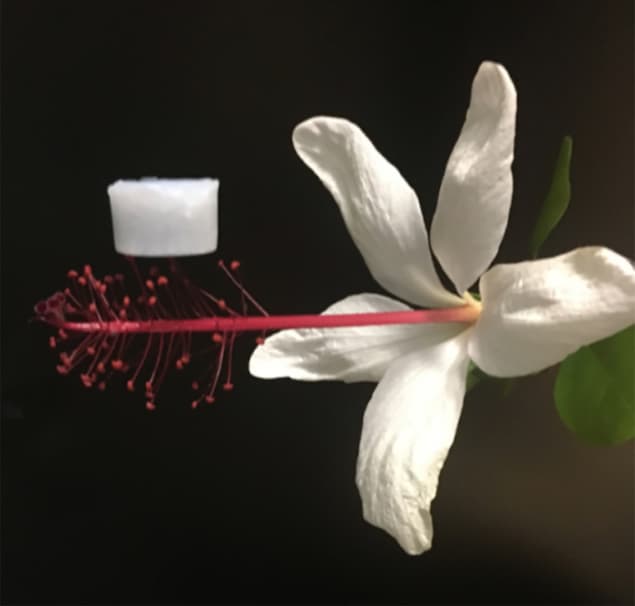
A new mechanically strong, double-pane ceramic aerogel made from hexagonal boron nitride that is resistant to high temperatures could be used in aerospace and industrial applications. The material, which boasts both a negative Poisson’s ratio and a negative thermal expansion coefficient, is very different to typical ceramic aerogels that are brittle and structurally degrade under thermal shocks.
Aerogels are exceptionally lightweight, composite materials containing more than 99% air. They can withstand high temperatures and are resistant to many chemicals. Most aerogels studied so far, however, are made from ceramic materials, such as silica, alumina and silicon carbide, and are thus very brittle.
Researchers recently made aerogels from graphene (a sheet of carbon just one atom thick). Here, the nanosheets of carbon stack up against each other, which makes the material incredibly strong. The nanosheets also divide the aerogel into nanosized cells through which air cannot pass. This means that the material has a thermal conductivity that is lower than that of air.
Sacrificial template
A team led by Xiangfeng Duan of the University of California, Los Angeles, has made a structurally similar aerogel from another 2D material, hexagonal boron nitride (hBN) by using a porous graphene aerogel as a sacrificial template. The researchers grew their aerogel using modified hydrothermal reduction and non-contact freeze-drying techniques. They used borazine as the hBN precursor and then grew hBN layers on top of the graphene structure using chemical vapour deposition.
Since hBN resists oxidation better than graphene and has a higher thermal stability as well, they are easily able to remove the graphene using a thermal etching process to leave behind the pure hBN aerogel.
The resulting material has a density as low as 0.1 mg/cm3 thanks to its highly porous structure with atomically thin cell walls (made of highly crystalline hBN), is superelastic (it can be compressed to 5% of its original length without breaking and fully recovers), and has an ultralow thermal conductivity (of around 2.4 mW/m∙K in vacuum and 20 mW/m∙K in air). It can also withstand sharp temperature shocks in that it can be heated to 900°C and then rapidly cooled to -198°C at a rate of 275°C per second over several hundred cycles while hardly losing any of its strength.
Careful microstructure engineering
The material’s superior properties come from the fact that it has both a negative Poisson’s ratio (it contracts inwards when compressed) and a negative thermal expansion coefficient (it contracts when heated). Duan and colleagues were able to confer both these properties (which are the opposite to conventional materials) onto their aerogel by carefully engineering its microstructure through hierarchical structuring and produce a material with hyperbolic frameworks. These have saddle shapes with negative curvature.
“The sub-cell wall features in our aerogel also have a double-pane architecture that reduces wall thickness without compromising the mechanical strength of the material and facilitates out-of-plane vibration modes for the negative thermal expansion coefficient effect,” Duan tells Physics World. “Such walls also retard heat transfer by gas molecules to ensure very low thermal conductivity.”
According to the researchers, the new ceramic aerogels could be used as thermal insulation in applications that require extreme temperatures, such as spacecraft and automobile components. Since the material also has a high surface area of more than 1080 m2/g, a value that is higher than those reported for other ultra-light materials (around 800 m2/g for silica or carbon aerogels), it might also be used in applications that call for high surface-to-volume ratios, like gas catalysis and thermal energy storage.
The team, reporting its work in Science, says that it is now busy making ceramic aerogels with even better flexibility and robustness, higher working temperatures and lower thermal conductivity.