The James Webb Space Telescope (JWST) is scheduled to launch on 25 December. To mark the event, Physics World is publishing a series of blog posts on the telescope’s technological innovations and scientific missions. This post is the third in the series. Read the first here.

Because the James Webb Space Telescope (JWST) operates in infrared light, stray thermal emissions from the Sun, Earth and even the spacecraft itself could cloud its vision. To keep them out, mission scientists designed an intricate, tennis-court sized sunshield that is quite unlike anything NASA has attempted to deploy in space before.
The sunshield comprises five layers, or membranes, of an aluminium-coated polymer called Kapton that is widely used in space exploration thanks to its stability across a broad range of temperatures. This stability is crucial: the first, Sun-facing layer of the sunshield is expected reach 383 K while temperatures at the inner fifth layer will drop as low as 36 K. Even with the right material, though, designing the sunshield’s layers to perform in deep space has been “a significant concern” says James Cooper, the JWST’s sunshield manager at NASA’s Goddard Space Flight Center.
Part of the problem is that each membrane in the sunshield will expand or contract to a different degree depending on its operating temperature. Accordingly, the membranes sitting in a clean room at Northrop Grumman (the aerospace firm that designed and built the sunshield) are not the same size as they will be in space. “Each membrane is carefully sized for its predicted temperature range,” Cooper explains. “Layer one – the Sun-facing layer – will be the hottest, while layer five will get very cold. So layer five has to be built ‘too big’ on Earth because we know that the material will shrink when it gets cold.”
Under tension
Another challenge is that each layer of the sunshield is gossamer-fine. The first, hottest layer is 0.05 mm thick, while the other four are 0.025 mm; their aluminium coatings are just 100 nm deep. Keeping the membranes thin saves weight, but it could also leave the sunshield susceptible to damage. What happens if it rips?
Cooper’s reply is that the sunshield is designed to cope with some level of damage. He and his colleagues expect it to suffer various wounds from micrometeorite impacts during its working life, and the odd hole here or there will not affect its performance – especially since they built a grid of seams and rip-stops into each layer to prevent tears from growing larger than approximately one by two metres. “We can meet performance requirements with this size tear in any layer,” Cooper tells Physics World.
The greatest risk of damage, though, comes soon after launch. Each of the kite-shaped sunshield’s six corners contains a membrane tensioning system (MTS), and each MTS is attached to 15 cables – three for each of the five membranes, amounting to 90 cables in all. To pull the sunshield’s five layers apart, the MTSs have to reel these cables in. A rip or catch at this unfurling stage could be very damaging indeed, and getting the system to work in rehearsals proved tricky.
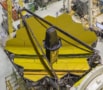
The ten-billion-dollar gamble: The JWST’s magnificent mirrors
“The MTS was relatively straightforward when bench-tested alone, but when we put everything together we found complex interactions with the membrane and cable management systems,” Cooper says. “We had to overcome challenges dealing with alternating tensions and slack in the cables.”
With the sunshield scheduled to begin unfurling three days after the telescope’s launch on 25 December, and taking five days to complete, it’s going to be a nervy New Year for Cooper and his colleagues as they wait to see whether the $9.8 billion telescope deploys successfully. But they won’t be the only ones biting their fingernails about keeping the JWST cool. While the sunshield will keep the telescope’s optics and most of its instruments at a frigid 36 K, some components need to be even colder.
Next: Keeping the JWST cool
- This article was amended on 22 December 2021 to reflect delays to the JWST’s launch date.