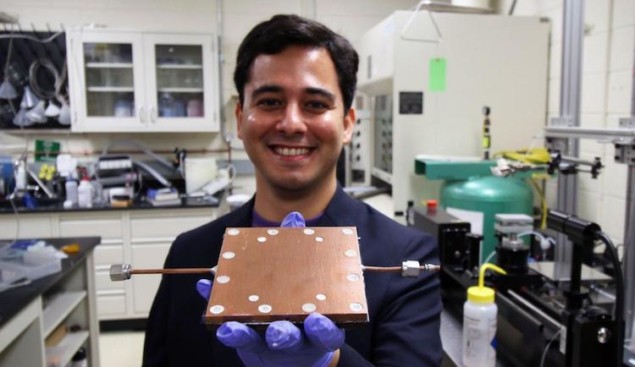
Electronic devices are hard to keep cool. Mechanical fans suck up energy. Heat sinks add unwanted bulk and mass. And thermal diodes – devices that allow heat to flow more easily in one direction than the other – are fragile, inefficient and require gravity to operate. Now, however, a new type of thermal diode looks set to overcome some of these drawbacks, with developers at Virginia Tech in the US suggesting that a future commercialized version could help manage heat in computer chips and aircraft components.
The directional thermal effect was first observed in the 1930s, when physicist Chauncey Starr of the Rensselaer Polytechnic Institute in New York developed a thermal diode based on a copper-cuprous oxide interface. The new device, dubbed a “bridging-droplet” diode, consists of two opposing copper plates separated by an insulating micron-thick gasket.
The surface of the first plate has a wick-like structure consisting of micropillars that hold and conduct water. The second plate, meanwhile, is coated with a water-repelling layer. In the diode’s forward operation mode, water on the wicking plate absorbs heat from its surroundings and evaporates into steam. The steam propagates across the narrow gap between the plate and condenses into dew-like droplets on the hydrophobic plate. When the droplets grow large enough to bridge the gap, they get sucked back into the wick structure, starting the process anew.
A “diodicity” as high as 85
During the device’s reverse mode of operation, the situation is different. In this case, the heat source is now on the hydrophobic plate, but no steam can be produced because the water remains in the wicking structure on the other plate. This transfer of water, explains team leader Jonathan Boreyko, is what allows the device to conduct heat unidirectionally. The new device can also be used upright, sideways or even upside-down and would thus work just as well in space.
The researchers measured the ratio of heat transferred from the wick side to the hydrophobic side – a quantity known as “diodicity” – to be as high as 85. While assymmetric heat pipes offer an even larger diodicity of around 100, their 1D heat transfer is ineffective for large 3D systems, Boreyko says. Placing an array of directional heat pipes into a wall panel solves this problem, but this is both complex and decreases the effective diodicity by more than a factor of 10, he explains.
Boreyko notes that the water-repellent coating he and his colleagues used to create their test device (a mixture of 1-hexadecanethiol in ethanol) is not suitable for practical applications. However, he says this coating could be replaced with more durable alternatives such as graphene or grafted polymers. This gives the Virginia Tech device a potential advantage over a conceptually similar device known as a “jumping-droplet” thermal diode, which requires a fragile superhydrophobic nanostructure to operate.
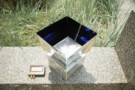
Electricity-free cooling material system shows potential
Members of the team, who report their work in Advanced Functional Materials, have filed a provisional patent for their diode and are now looking to collaborate with industry partners to continue the research. One of the items on their to-do list is to boost the diodicity of their device to 100. This could be achieved, for example, by decreasing the height of the micropillars so that smaller droplets could bridge the insulating gap between the two copper plates. The researchers would also like to test more durable hydrophobic coatings.