Monitoring metals in liquids in real time, rather than via laboratory analysis, is the mission of Sensmet, a Finland-based instrumentation start-up. Co-founder and chief technology officer Kalle Blomberg spoke to Physics World about the company’s origins and the role that Avantes spectrometers play in its technology
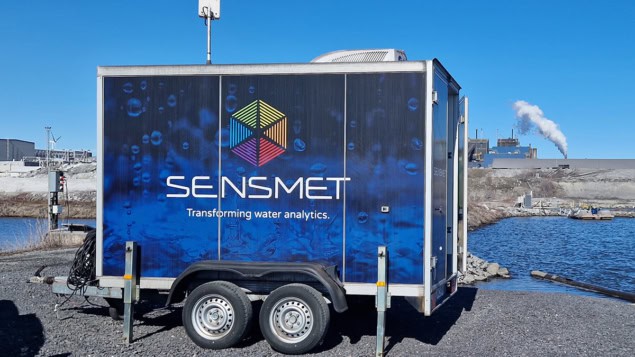
How did Sensmet get started?
The initial idea to build an online system that uses a micro-plasma to analyse metals in liquids came from Toni Laurila, who is now Sensmet’s co-founder and CEO. He got the idea during his post-doctoral studies at the University of Cambridge, UK, and after he returned to Finland, we started to develop an online instrument for industrial process and environmental applications.
Typically, if you need to measure metals in liquid – whether it’s wastewater, industrial process water or natural bodies like rivers and lakes – you collect a sample and send it to a laboratory for analysis. Depending on the lab, it might take up to several days to get the results. If you need to control a process based on such outdated data, it’s like trying to drive your car while solely relying on a rearview mirror where the image is 4‒10 hours old. By the time you see what’s happening, you’ve already veered off the road.
We saw that we can do for liquid monitoring what other companies did for online gas monitoring around 30 years ago, when the regulations started changing in a way that meant practically all gaseous emissions needed to be monitored in real time. We believe this will also be the future for liquids.
What kinds of liquids are you analysing?
Regulations on real-time monitoring of liquids are going to come at some point, and we believe that our technology will make that possible, but it has not happened yet. This means that for now, we are focusing on analysing liquids involved in industrial processes, because that is an area where we can give customers a return on their investment.
A good example is the battery industry, which is growing rapidly due to the popularity of electric cars. This is driving huge demand for lithium and other metals. If we want to produce enough electric cars to reduce emissions from petrol and diesel vehicles, we can’t do it just by mining new metals. The recycling rate for old batteries also needs to rise.
How does battery recycling work, and how do Sensmet’s analysers help?
Typically, you take the end-of-life battery from an electric car and shred it into very fine particles to create what’s known as the black mass. Separating the valuable metals from the black mass then involves a hydrometallurgical process, where the metals are converted into a liquid form, typically by dissolving or leaching them in acids. Once the valuable metals are dissolved, they are extracted from the black mass one by one through processes such as solvent extraction or ion exchange.
What makes our analyser particularly well-suited for monitoring this battery recycling process is that we can measure multiple metals simultaneously. This includes light elements such as lithium and sodium that cannot be measured using X-ray fluorescence, a commonly used technique for metals analysis.
Real-time measurement is essential for optimizing the battery metal recycling process. By continuously monitoring the concentrations of key metals such as lithium, manganese, cobalt, nickel, copper, aluminium and calcium, process operators can quickly detect anomalies, enhancing both quality and efficiency. The speed of the processes used to separate elements from the black mass is another critical factor. If you’re having to wait around for a laboratory analysis, you cannot optimize them very well. You’re not getting the rapid, real-time measurements you need to improve your yield, and that can mean increased waste.

A clear example is ion exchange columns, which require periodic regeneration as they become saturated. Our analyser monitors the solution from these columns, and when it detects a rise in, say, nickel concentration, the customer knows it’s time to regenerate the column. In these situations, the speed of analysis is crucial for optimizing the production efficiency.
What challenges did you encounter in developing your analyser?
While proving a technology’s effectiveness in the lab is relatively straightforward, developing a product that performs reliably in real-world conditions is much more challenging. Our customers require an analyser that is both robust and reliable in demanding industrial environments, consistently delivering accurate results day after day, year after year.
We also conduct environmental online monitoring of industrial wastewater, which is challenging in Finland, where winter temperatures can drop to –35 °C. To address this, we can house our analyser in a container and use heated measurement lines to transfer the liquid samples, for example from a settling pond.
These harsh conditions and customer requirements are some of the reasons we chose to use a spectrometer from Avantes in our analyser. The way Avantes builds their spectrometers, they are quite robust. If you accidentally hit them a little bit, they maintain their calibration.
What are some other advantages of Avantes spectrometers?
We bought our first spectrometer from them before we spun out of the university in 2017. It was a high-resolution system for plasma research, and it allowed us to do very fast measurements and collect multiple spectra at high speeds. After that, it was easy to choose the next spectrometer from the same manufacturer because we’d already built the programs and controls for our prototype analyser based on it. And we’ve always had very good service from Avantes. When we have faced a problem, they’ve always helped us quickly. That’s very important, especially at the university stage when we were using the spectrometer beyond its regular scope.
What do you know now that you wish you’d known when Sensmet got started?
When we started building our analyser and realized what it could do, we felt like kids in a candy shop surrounded by a million treats. There is water everywhere, so we believed our technology had universal appeal and expected everyone to adopt it immediately.
As a start-up, focus is everything. You need to concentrate on a specific market and convince those customers that your product is the right fit for them. Only then can you expand to the next market. However, we were young with limited experience, so it took us some time to realize this.
What are you working on now?
Our first product is ready, so our focus is on pushing it to the market. We are working with multiple battery manufacturing companies and mining companies to make ourselves known as a reliable provider of analysers that can really bring significant added value to customer processes.
Kalle Blomberg is the chief technology officer at Sensmet