Why has plasma processing captured the imagination of bioscientists so strongly and what triggered its rapid rise in popularity? James Tyrrell catches up with Uroš Cvelbar of the Jožef Stefan Institute in Ljubljana, Slovenia, for the answers
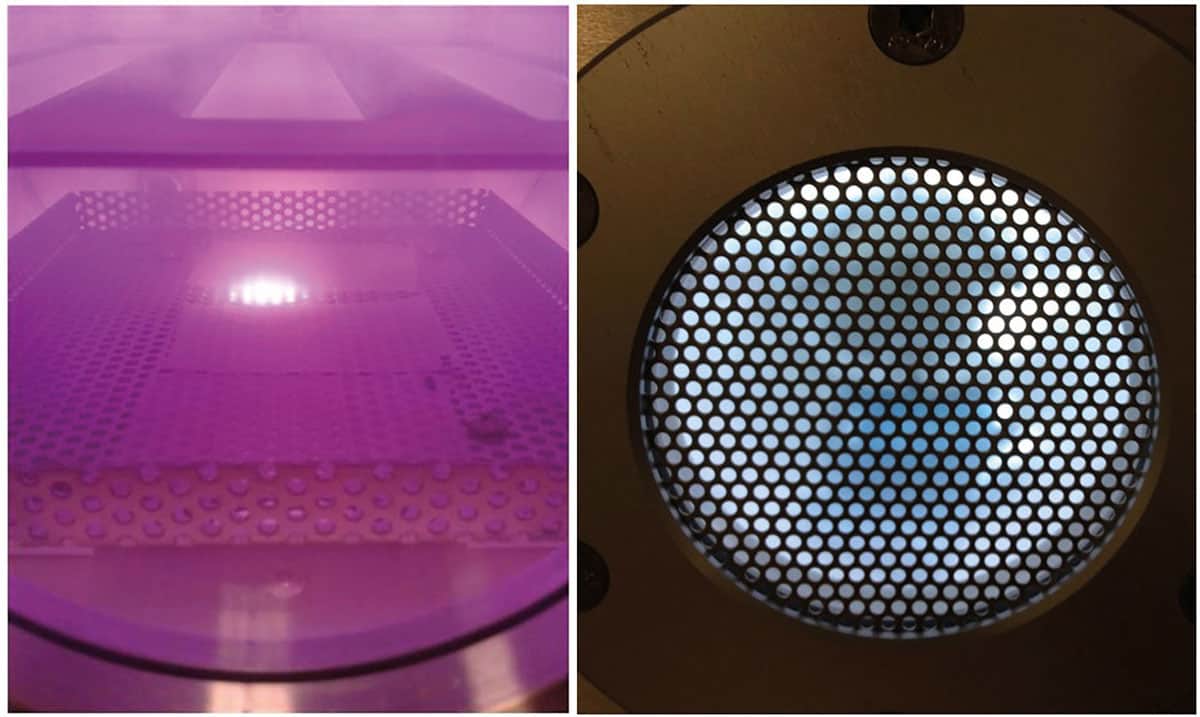
Plasmas – ionized gases – generated in vacuum have long played an important role in the surface processing of wafers in the electronics industry. Device makers rely on plasma methods to clean, etch and coat the various layers of a material that will form the computer chips driving our smartphones, laptops and other electronic goods. The popularity of plasma processing in the semiconductor industry has led to a boom in tools and equipment, but it is not just the electronics industry that benefits.
“Over the past 20 years, the success of plasma techniques in the semiconductor sector has given a tremendous boost to other fields, especially in the area of low-pressure systems,” says Uroš Cvelbar of the surface-engineering team at the Jožef Stefan Institute in Ljubljana, Slovenia. Researchers are now applying these methods across a wide range of emerging applications, with one of the fastest growing areas being the use of plasma processing in medical applications and in the development of biomaterials.
Versatile technology
“It has become a very broad field as there are just so many things that you can do with plasma and biomaterials,” says Cvelbar. “Here at the institute, we can deposit films, we can modify existing surfaces and add functionality – it’s a versatile technology.”
Cvelbar first became interested in the area through his background in plasma physics and materials science, and enjoys the interdisciplinary environment needed to take ideas forward. “Today, my group includes chemists, microbiologists, biotechnologists, as well as physicists,” he explains. “The team also collaborates with medical researchers and doctors through different institutes and clinical centres, as they are the end-users of the materials we’re developing.”
One of the most popular methods for processing biomaterials and polymer surfaces is to use low-temperature plasmas generated either by a radio frequency, microwave or DC source or by applying very fast pulses of electricity. “High voltages are normally used to create the cold plasma in the presence of a carrier gas at atmospheric pressures, whereas a vacuum has been applied mostly to clean and deposit materials,” says Cvelbar. “For cold plasma processing in a vacuum environment, the use of sources operated at microwave or radio frequencies is typical.”
Plasma processing offers a very clean environment and even the means for sterile processing, which makes it well suited to many medical uses. Another benefit is that the feedstock is typically made up of only a few substances, which helps to minimize – and even avoid altogether – residues that could otherwise cause problems later on in the application. What is more, ionized gas and plasma radicals – loose ions, neutral atoms and excited atoms or molecules – can kill, inactivate or completely destroy microbiological organisms, such as bacteria, viruses and fungi, after prolonged exposures.
You can perform in vivo treatment of wounds with plasmas generated at atmospheric pressure
For Cvelbar and other researchers, plasma-processing technology gives them lots of different avenues to explore. “With plasma, you are working with ions or other reactive species that modify or functionalize a surface in such a way to obtain better attachment of molecules for cell growth, or to enable biosensing of different chemical species,” he says. “You can also perform in vivo treatment of wounds with plasmas generated at atmospheric pressure.”
Medical efforts
Two strategies are currently being pursued. “One approach is to use the plasma to decontaminate the wound and kill unwanted bacteria on the surface [but] at the same time adding radicals that boost cell growth to accelerate the healing process,” Cvelbar explains. “The second strategy involves depositing activated collagen to coat the wound, which again could speed up the patient’s recovery compared with simply exposing the wound to the open air.”
In both cases, treating a wound would require a device that can be placed over the patient, which means that smaller, more portable atmospheric systems are set to play an increasingly important role as the technology matures.
So where are the sweet spots for vacuum? “Low-pressure systems are used mostly to treat and prepare materials that can be processed away from the body, such as artificial hips,” Cvelbar says. “Examples include coating implants with a bio-compatible material to encourage cells to grow around them by providing a scaffold, which helps to keep the devices in place once inside the body.”
Being bigger in size, low-pressure processing set-ups can be well suited for larger operations but there is a downside too: the construction of bigger chambers, the requirement for vacuum pumps, and the need for a range of measurement systems make such schemes more expensive. “Price is a factor, but if you want to do atom-by-atom manipulation where you need extremely high levels of process control, then low-pressure systems offer considerable value,” says Cvelbar.
There are other issues to think about too before deciding on which system is needed for a particular application. “If you are working on tissues or soft biological matter subject to potential evaporation, these cannot subsist in a low-pressure environment, and this needs to be managed,” Cvelbar adds.
Atmospheric challenges
Atmospheric systems present challenges as well – humidity, for example, can influence the treatment and add to the number of parameters that need to be controlled. Under ambient conditions, plasma species react with the surrounding air as well as with the target sample, which can make the desired outcome more complicated to achieve. “The advantage of a vacuum system is that it provides a very clean and well-known environment, which helps in controlling your process and delivering consistent results,” says Cvelbar. “With atmospheric systems you can have more unknowns and may have to rely more on post-processing analysis.”
As for Cvelbar’s own work, his team’s projects fall into several different categories. One is the plasma deposition of antibacterial coatings where the group – together with Anton Nikiforov and Christophe Leys at Gent University in Belgium – is using the technique to add polymers to the surface of target materials. The researchers then go down two routes. One is to apply classical wet-chemical processing to add nanomaterial, followed by a further coating to sandwich the tiny structures between the substrate and this top layer. The other is to dope the plasma with nanoparticles so that the additives become secured within the matrix upon impact with the substrate.
The team is also carrying out plasma processing of surfaces for improved drug loading, which allows more of the active substance to be adsorbed onto the sample – in this case, a textile material. “We are using this method to develop medical dressings and patches with more controlled and longer lasting drug-release characteristics,” says Cvelbar. “The drug is much more tightly bonded to the surface in the case of plasma-processed material.”
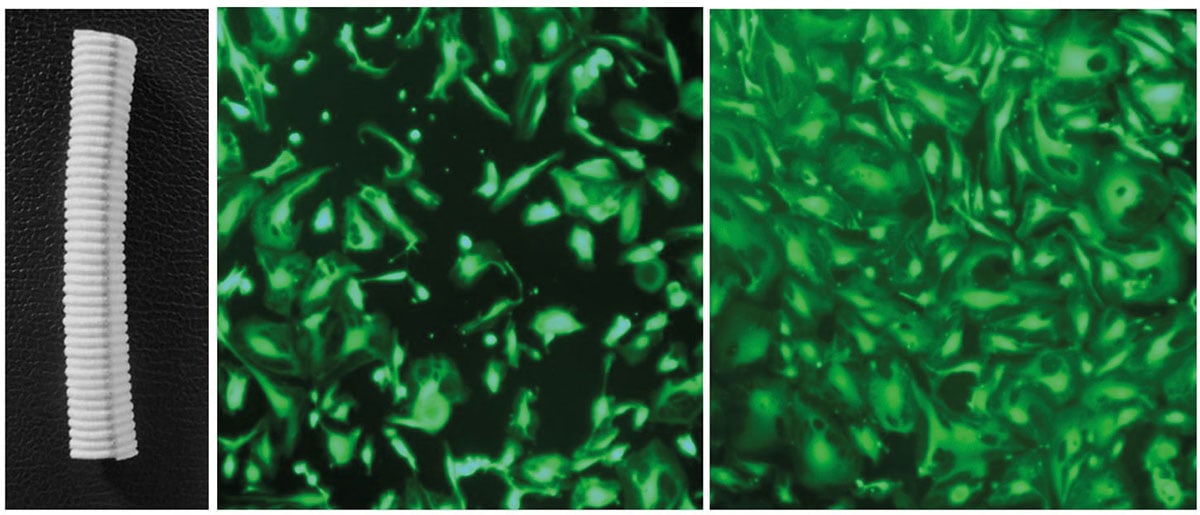
The effect can be dramatic. As Cvelbar explains, when you take conventional oral antibiotics, the drug reaches peak concentration in the body relatively quickly, so that after barely eight hours you often need to take a new dose. A plasma-engineered patch or bone implant, however, not only requires patients to take fewer drugs orally, which can otherwise overload the body, but also releases the drugs much more slowly and directly at an infected area, thereby reducing the burden for the patient.
Other projects include the use of plasma-grown nanomaterials as a building block for sensors, which warn against the presence of carcinogenic or toxic molecules in the surrounding environment. Thanks to the plasma treatment, the researchers can engineer nanostructures that enable sensing devices with much faster response rates than existing solutions. Typically, the sensor consists of an array of active sites, each of which may be tailored to respond to a different molecular species. Comparing the signal response of these structures against a reference provides the team with the inner workings of a device.
“Medicine is major driver for the application of biomaterials and for research into this scientific field,” says Cvelbar, who advises anyone thinking of moving into this field to attend relevant meetings, which this year include the International Conference on Plasma Medicine (ICPM) being held in Bratislava, Slovakia, in September. Another relevant conference this year is the American Vacuum Society meeting in Tennesse, US, in November, while further ahead is the World Biomaterials Congress scheduled to take place in Glasgow, UK, in 2020.
From bench to bedside
For researchers targeting medical applications, one advantage of working with biomaterials is that this can often be the most straightforward way of introducing plasma medicine into clinical practice. Examples include modified materials that are implanted within the body or are used as surface patches. Gaining approval for the plasma processing of wounds and related treatments or applying plasma methods to kill cancer is – in contrast – typically a much longer journey.
“When you are dealing with living bodies, approval of a new therapy needs time to be evaluated,” Cvelbar warns. “However, for biomaterials, you will often have some standard cases and references that can be included to help with the evaluation process.”
Special issue
To highlight the latest developments in plasma-inspired biomaterials, Uroš Cvelbar has teamed up with Cristina Canal from the Technical University of Catalonia, Barcelona, Spain, and Masaru Hori of the University of Nagoya, Japan, to guest-edit a special issue of Journal of Physics D: Applied Physics from IOP Publishing, which also publishes Physics World. The article collection, which is now open for submission, covers all aspects of research connecting plasma and biomaterials – ranging from plasma preparation of biomaterials for different applications (including both soft and hard tissue, such as teeth and bone), as well as drug-delivery applications and antibacterial coatings. The special issue also focuses on biological interactions of the novel plasma-prepared surfaces with bacteria, cells and tissues. Novel developments for diagnostics and sensing will be showcased too.
More information on the special issue of Journal of Physics D on plasma-inspired biomaterials is available at this link, guest-edited by Uroš Cvelbar (e-mail uros.cvelbar@ijs.si)