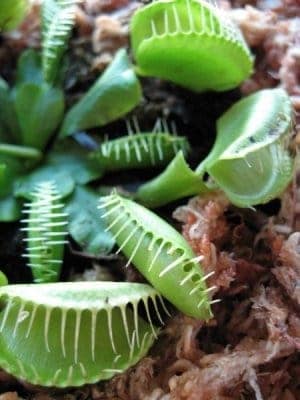
It may be best known for ensnaring flies, but now the Venus flytrap has also captured the attention of some materials physicists in the US. Alfred Crosby and colleagues at the University of Massachusetts at Amherst have been inspired by the carnivorous plant’s unusual jaw structure to create a new material that can rapidly change its shape when stimulated by pressure, heat or electrical current. The team claims that the material could be used to create surfaces that change their reflectivity or lenses that switch between focal lengths.
The movement of the Venus flytrap relies on a “snap-buckling instability”, a common phenomenon that can be demonstrated for any rubbery hemisphere. Slice a tennis ball in half, for example, and then hold one of the halves by the edges so that it is convex, or dome-shaped. Applying pressure with your thumbs will deform the ball — up to a certain critical point when it flips to the concave, or bowl-shaped, state.
In a Venus flytrap this lethal flipping from convex to concave occurs when a fly crawls between the open jaws and touches one of many tiny hairs located inside, although botanists are divided on exactly how the hair triggers the signal. “This plant can change the shape of its lobes from concave to convex at very high speeds — around 100 ms,” Crosby told optics.org, sister website of physicsworld.com.
Crosby’s group sought to create a structure that could exhibit this behaviour on small scales throughout. They began by moulding an array of circular protrusions onto a 1-mm-thick silicone layer. They then stretched the layer, and bonded another layer of unmoulded silicone underneath to create pockets or air. It is these air pockets combined with the rubbery nature of the material that gives way to the snap-buckling instability, so that all the protrusions can be triggered between the convex or concave state (Adv. Mater. 19 3589).
Many triggers
Unlike the jaws of the Venus flytrap, the Massachusetts group’s material can be triggered by pressure, heat or an electrical current. When the individual protrusions — which are like tiny lenses — change from convex to concave, the entire surface is modified in its reflectivity and focal length. This means that the material could be used in outdoor signs where the reflectivity of the surface keeps changing, or as an adaptive lens that can focus by itself.
Each protrusion in the surface can be fabricated in pretty much any shape or size. In this work, the Crosby’s group built them with diameters ranging from 50 µm to 500 µm and spaced them 10 to 50 µm apart. At these sizes the transition speeds are 30 ms or faster, and as the lenses get smaller, the speeds go up.
“[The material] could potentially be applied in arrays of on/off operating devices, such as optical switches and as actuators that control other components.” said Hongrui Jiang of the University of Wisconsin, who last year produced a liquid lens that mimics the human eye. Jiang added that the fabrication process must now be improved to produce lenses with highly uniform shapes and smoother textures.
This article originally appeared on optics.org