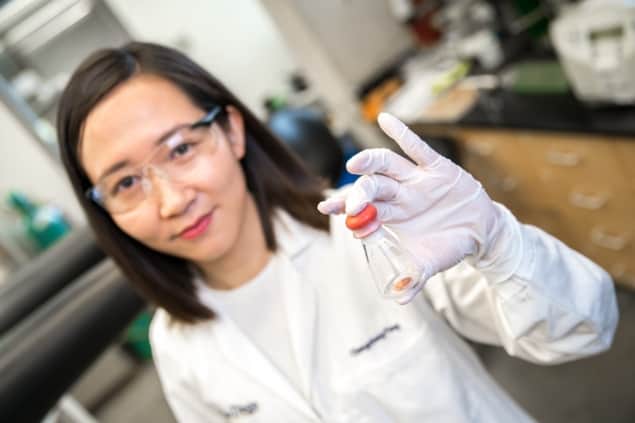
Powering devices as small as smartphones to those as large as electric vehicles, the rechargeable battery is a familiar technology to consumers. Work in the field of battery research continues, however, as researchers struggle to improve the efficiency and longevity of rechargeable batteries. State-of-the art Li-ion batteries offer fast charging but suffer from low power density. Research has therefore focused on optimization of battery anodes, cathodes, electrolytes, and even on replacement of lithium itself with other metals like sodium.
Of these alternatives, lithium metal batteries, have been studied since the 1960s and 1970s. Lithium metal batteries intrinsically offer higher energy density than Li-ion batteries, but according to Shirley Meng, a professor at UC San Diego Jacobs School of Engineering, a lot of technical challenges have prevented its commercialization.
One challenge is the presence of inactive lithium at the solid electrolyte interface (SEI) that forms each time a lithium metal battery discharges. Over several cycles, the battery forms such a significant amount of inactive lithium that it loses the ability to recharge. For years, researchers have thought that both lithium metal blocked from the conductive pathways by the SEI and lithium ion compounds formed in the SEI contributed to inactive lithium.
Chengcheng Fang, a recent graduate from Meng’s group, has shown that the real culprit is the metallic lithium. To do so, Fang developed a tool based on gas chromatography that, for the first time, allows researchers to measure just how much inactive lithium metal forms versus the formation of lithium ion compounds. The researchers found a linear relationship between the amount of metallic lithium present and loss of Coloumbic efficiency.
“Prior to [our work], the entire field had no idea [of] the quantitative contribution of capacity loss from SEI. The claims in literature were hypothesis only,” Fang said. “Since SEI has high surface area and is easy to detect, researchers turned to blame the capacity loss on SEI formation.”
Their findings, however, dispute this hypothesis, and show that metallic lithium is the main component of inactive lithium.
Identifying the right culprit
The researchers’ novel tool combines titration and gas chromatography to study battery systems. They leveraged the fact that the main difference between SEI lithium-ion compounds and metallic lithium is their chemical reactivity. Knowing that only metallic lithium reacts with water to generate hydrogen gas, they added H2O to a sample to measure the generation of hydrogen via gas chromatography.
Once the amount of unreacted metallic lithium had been determined, they calculated the amount of lithium ions present at the SEI as the difference between the total inactive lithium present (given by the capacity loss between the plating and stripping processes) and this calculated quantity of unreacted metallic lithium. Across tests on various electrolyte systems, they found much more lithium metal is present than other components containing lithium ions.
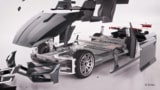
Beyond the lithium-ion battery
“This is a reliable method to quantify the two components of inactive lithium with ultrahigh accuracy, which no other characterization tool has been capable of doing,” Fang said in a press release from the University of California San Diego.
The researchers replicated the relationship between metallic lithium and efficiency loss across different systems. The type of electrolyte used, however, did affect the value of the Coulombic efficiency they measured, as it influenced the morphology of the inactive lithium.
Next steps
With their findings, the authors have begun exploring alternative electrolytes and other new avenues that would mitigate the issues raised by inactive lithium. They aim to use these improvements to allow for the safe use of lithium metal batteries for longer lifetimes than currently attainable.
In the future, researchers hope that their work will motivate the commercialization of lithium metal batteries.
“The goal is that if you enable lithium metal to cycle as current state-of-the art, then you can double the driving range for an electric vehicle,” Meng said.
In a separate interview with electrochem.org, she said, “There is no reason why we should be burning all this fossil fuel with millions of cars.”
Full details are reported in Nature.