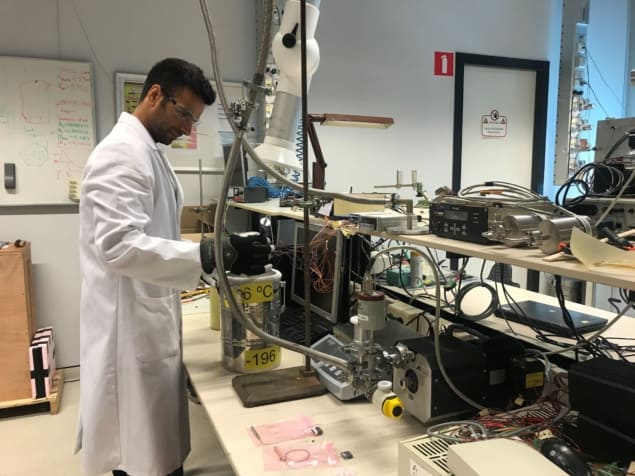
A phenomenological model devised by scientists at the University of Twente in the Netherlands sheds new light on the behaviour of metals cooled by liquid nitrogen – and specifically the somewhat counter-intuitive classical observation that insulated metals cool down faster than their bare counterparts (Cryogenics).
“Our model and the related understanding of the low-temperature physics are novel,” says Srinivas Vanapalli, head of Twente’s Applied Thermal Sciences Laboratory. In addition to the fundamental insights, Vanapalli and his PhD student Sahil Jagga reckon that their findings will make it possible to design faster and more efficient cryogenic cooling systems.
A significant barrier to rapid cool-down in cryogenic systems is the evolution of a vapour film between the liquid-nitrogen coolant and the stainless-steel tubing that connects the cryogen bath to the cryogen storage tank. This phenomenon – known as the Leidenfrost effect – results in a low heat transfer rate and inefficient usage of precious coolant.
Now, Vanapalli and Jagga say they have come up with a workaround that addresses this problem while simultaneously optimizing the associated workflow. Their data-driven model is the result of a systematic set of quenching experiments on copper cylinders coated with different thicknesses of low-conductive epoxy. During these experiments, the researchers evaluated the heat flux (W/m2) and cool-down time of cylinders in both saturated – that is, just about to boil – and subcooled liquid nitrogen.
The researchers found that an early transition between two liquid-nitrogen boiling regimes – from film boiling (as seen with the Leidenfrost effect) to the so-called nucleate boiling regime – is a major driver of enhanced cooling, as it promotes the formation of cold spots between the liquid and insulating layer. “In terms of the underlying physics,” explains Vanapalli, “coating the tube with an insulating material increases the liquid–solid contacts at the surface to yield a more efficient cooling process.”
The utility of the University of Twente model is that it predicts the right coating thickness of the cylinders, since coatings that are too thin or too thick will slow the cooling rate. According to Vanapalli, theirs are the first results to show that the optimum coating thickness depends not just on the thermal properties of the coating material, but also on the thermodynamic state of the liquid nitrogen – in other words, whether it’s saturated or sub-cooled.
Previous studies elsewhere have sought to evaluate the effect of insulating coating thickness at the minimum film-boiling temperature – the point where the vapour film between liquid and solid surface collapses – but the microscale mechanisms in play have proved frustratingly elusive. The Twente researchers also note that, until now, scientists seeking to optimize the thickness of the insulation coating in a way that minimizes cool-down time relied exclusively on empirical investigation – essentially trial and error.
Cold science, hot stuff
More widely, Vanapalli notes that there are commercial drivers in play, since liquid-nitrogen cooling finds diverse applications within research and industry. These applications include cryopreservation of biological samples in “biobank” repositories; studies of high-temperature superconductivity; whole-body cryotherapy in professional sports; and quenching of tool-steels for improved hardness and durability, to name just a few.
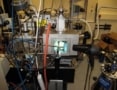
Study of liquid-nitrogen droplets gives new insight into cryogenic spray-cooling
With this in mind, Vanapalli and Jagga plan to scale their new model to cover a range of coating materials, as well as other cryogenic liquids such as argon, hydrogen and helium. Two main inputs will be needed: the thermal properties of the coating material and critical heat flux data for specific pairings of metal surfaces and cryogenic liquids. “As a next step, we will acquire experimental data with argon and hope that the cryogenics community will contribute for other fluid–surface pairings,” Vanapalli says. “Ultimately, the aim is to translate this effort into an open-access web tool to benefit cryogenic system designers.”
The research is sponsored by Dutch funding agency NWO-TTW within the CryoOn project.