Richard Wood describes how the precise control and measurement of the thermodynamic properties of materials can improve freeze-drying processes
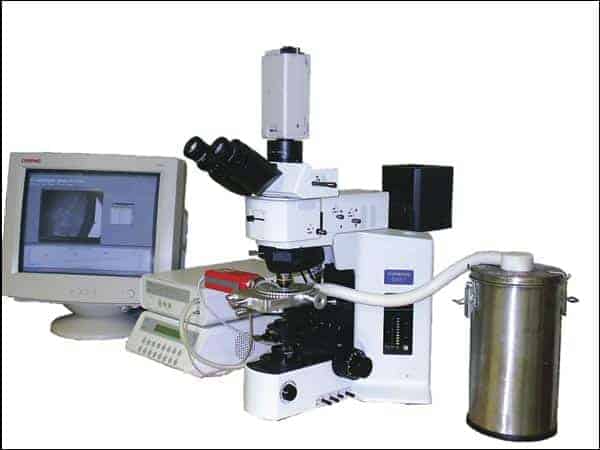
Freeze-drying (lyophilization) is the process of freezing a material under vacuum to remove water. It is used to preserve a range of substances (most famously coffee) and plays an important role in the manufacture of pharmaceutical, biological and diagnostic healthcare products.
While commercial pharmaceutical freeze-drying has been commonplace for more than 60 years, controlling the process remains challenging and research continues into the methodologies involved – often driven by industry regulators. Most freeze-dried products are made by processes developed through trial and error, rather than from empirical data.
A small number of companies, including Biopharma Technology (BTL), are working to change this by developing analytical instruments to determine the temperatures at which materials go through key structural phase transitions. For BTL’s customers alone, this information has been crucial in controlling the quality of 470 different freeze-dried product formulations.
A freeze-dryer consists of a vacuum chamber where the product, often in vials, is placed on a special shelf, the temperature of which is controlled. Water vapour generated during the drying process is removed via a connection to a second vessel called an ice trap, which condenses the vapour into ice. Both vessels are maintained at vacuum levels down to 10–3 mbar. The shelf-temperature range is typically –50 °C to 60 °C and the ice trap is at –75 °C.
The freeze-drying process involves three main phases: freezing; primary drying; and secondary drying. Each involves exposing the material to different thermo-dynamic conditions and success relies on understanding the behaviour of the water during each phase.
In the freezing phase, close attention must be paid to the behaviour of both the solvent (usually water) and the solute(s) in the starting material. The way in which a solution freezes defines the structure and porosity of the final product and must be controlled very carefully. Ice formation is a two-stage process. The first stage is nucleation, which involves water molecules arranging themselves in tiny crystals or gathering around impurities. The second is crystal growth, and in freeze-drying the size and networking of the crystals are of more interest than their shape.
The solutes will freeze into a crystalline, amorphous or multiphase structure depending on the type of material. There are three critical temperatures that affect the process. These correspond to the eutectic (Teu) phase transition for crystalline material, and the glass transition (Tg) and collapse transition (Tc) for amorphous material. These usually define the maximum allowable temperature that the sample can be held at until all of the ice has been removed.
Ice is removed by sublimation during primary drying. However, sublimation cools the material and so energy must be put into the product to compensate for this. Energy is transmitted to the product mainly by gaseous convection and conduction, and transmission is controlled by adjusting the shelf temperature and chamber pressure. The pressure is controlled to within approximately ±5 × 10–3 mbar, typically over a range of pressures between 2 × 10–2 and 50 × 10–2 mbar.
Only the top of the sample is exposed to the vacuum, so drying occurs from the top down. The sublimation interface, which moves down as drying proceeds, should be kept below the critical temperature of the product throughout primary drying to avoid processing defects. In crystalline systems, for example, the entire frozen mass should be maintained below Teu to avoid boiling, which can result in the product being splattered around the container.
Measuring the temperature of the sublimation interface is a significant challenge. Near-infrared thermal imaging has not been particularly successful, so instead the measured rise in vapour pressure can be used to calculate the temperature. Currently, however, the majority of commercial processes do not involve measuring the interface temperature.
Once sublimation is complete, the product will resemble a dried cake or powder, but it will often contain sufficient moisture to reduce shelf stability significantly. This moisture is referred to as “unfrozen water” and may be absorbed, associated or chemically bound to the product. It is removed by secondary drying, whereby higher shelf temperatures and lower chamber pressures are typically employed to encourage desorption of the unfrozen water.
A freeze-drying process can take from a few hours to several days to complete, and the length of each phase can vary significantly, depending on factors such as the product and the type of containers used, and their depth of fill.