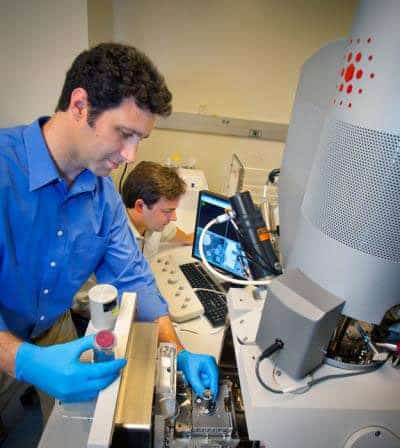
The recent Fukushima disaster has raised renewed concerns about the safety of nuclear power, with many countries calling for stricter checks in nuclear power plants. Now, researchers at the Berkeley Lab, the University of California at Berkeley and the Los Alamos National Laboratory, all in the US, have developed a new nanoscale testing technique for irradiated materials that provides information on the strength of these materials on much larger length scales. The method could greatly reduce the amount of material required in tests and also help in the design of new, improved materials for nuclear applications.
Nuclear power came to the fore in the late 1950s and 1960s, and many nuclear power stations were built around the world at that time. Nuclear power currently generates about 20% of the world’s electricity, including 50% in western Europe and as much as 80% in France. Beyond power generation, many nuclear facilities are also used for research or for producing medical radioisotopes for use in hospitals and clinics.
The structural materials used in these facilities are regularly tested to ensure safe operation but engineers are always on the lookout for simpler, less invasive tests that cause minimal disruption. The new technique, devised by Andrew Minor and Alex Zettl’s teams in California, can be performed on samples as small as 400 nm and yields real mechanical strength data on the macroscale for the material being tested. This is a first because, previously, nanoscale mechanical tests always seemed to give higher strengths than the macroscale bulk values, explains Minor.
Deforming atomic planes
The researchers obtained their results by performing compression tests (using a flat diamond punch) on copper samples that had been irradiated with high-energy protons at 1.1 MeV. These are the sorts of energies experienced by real working materials employed in nuclear power plants. The tests were designed to model how damage from radiation affects the mechanical properties of the metal. Using an in situ mechanical testing device in a transmission electroscope, the team was able to observe the material deforming on the nanoscale, and found that the deformation was limited to just a few atomic planes.
Before the compression tests, the samples contain a high density of small 3D defects. This is typical of irradiated samples. After compression, the researchers saw short 1D dislocation segments as well as some of the original 3D defects.
The 3D defects in the copper can block the motion of the 1D dislocations, something that makes the material more brittle and susceptible to fracture at lower loads. The team confirmed this by performing load tests on irradiated and non-irradiated samples and comparing the two.
Translating to the bulk
Peter Hosemann of UC Berkeley says that, by translating the nanoscale strength values obtained into bulk properties, the technique could help reactor designers find better materials for use as engineering components in nuclear plants. “And by using a smaller specimen for the tests, we limit any safety issues related to the handling of the test material,” he said. “We could potentially measure the exact properties of a material used in, say, a 40-year-old nuclear facility to make sure this structure lasts well into the future.”
Understanding the role of defects on the mechanical properties of nuclear-reactor materials will be crucial for designing materials that are more resistant to radiation damage, and lead to more advanced and safer nuclear technologies, added Minor.
The work was reported in Nature Materials doi:10.1038/nmat3055.