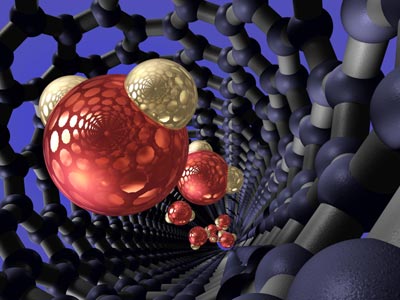
A UK researcher is calling into question the capability of the nanotech industry to turn fundamental research into robust technologies that can be produced on a large scale. Mike Kelly at the University of Cambridge argues that manufacturing constraints will prevent structures smaller than 3 nm in size from being mass-produced using “top-down” processes.
“There are many billions of dollars being spent on one-offs while the bull in the china shop is the ultimate challenge of manufacturability,” Kelly told physicsworld.com.
Kelly is making these claims after carrying out a case study of the production of vertical nanopillars, which have been touted for uses in sensors and displays. These components can be produced at present by two different top-down approaches: using a metal particle catalyst to grow the pillars; or by infilling holes in a resist layer that can be defined using lithography.
Intolerable variations
Kelly considered the variability in the properties of nanopillars created using these two production methods and found that a large standard deviation in size and shape started to creep in once the scale reached below 3 nm. This, he says, would lead to intolerable variations in their electronic, optical and other properties if the nanopillars were to be used in applications.
On the back of his findings, Kelly believes that, given specific tools for fabrication, some nanostructures are intrinsically unmanufacturable. “The statistics of small numbers means that currently used methods will simply produce artefacts with too big a variation between adjacent features to be useful for anything,” he said. “If I am wrong, and a counter-example to my theorem is provided, many scientists would be more secure in their continued working, and that is good for science.”
‘Perfect’ structures
Rod Ruoff, a materials scientist at the University of Texas at Austin, agrees that some nanostructures below certain sizes will not be sufficiently stable in their structures and chemistries for all applications. “It is thus valuable to raise questions about what length scales are realistic, for each technology, for each application,” he said.
But Ruoff disagrees that bottom-up processes cannot be used to produce consistent specifications in bulk, and he highlights carbon as a promising material. “One of the attractive features of carbon nanotubes and graphene is their relative chemical stability, and the fact that such nanostructures can in fact be ‘perfect’ in structure even at the Angstrom length scales.”
Order from disorder
This is a view shared by Philip Moriarty a nanomaterials researcher at the University of Nottingham in the UK, who says that the limitations of top-down fabrication are already well-recognized by academics and industrial scientists. “This has prompted an intense research effort focussed on exploiting so-called bottom-up techniques such as self-assembly and, in particular, directed self-assembly.”
By this, Moriarty is referring to processes in which disordered systems of components form organized structures as a consequence of specific, local interactions among the components. This directed self-assembly is described by some as a hybrid of top-down and bottom-up fabrication techniques.
Moriarty believes that Kelly has presented the “effective error bars” associated with nanofabrication, rather than a general theory. He also said that he disagrees fundamentally with the assertion that scientific research should be focused on what can be manufactured now. “Fundamental nano scientific research should not be constrained by our current understanding of the limits of nanomanufacturability.”
This research is described in the journal Nanotechnology.