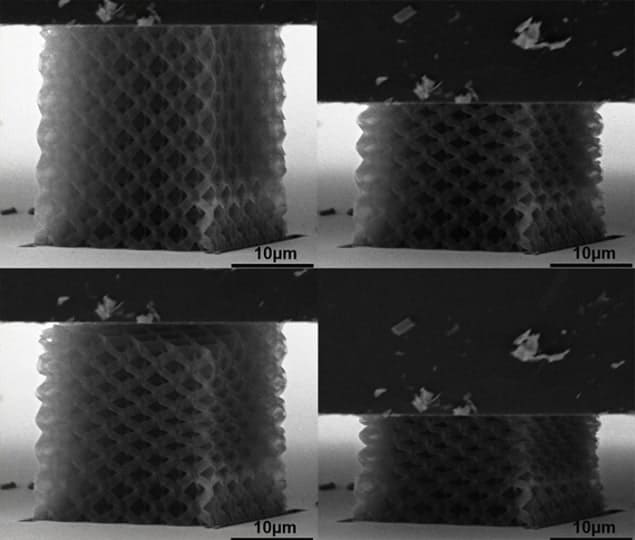
A nanostructured ceramic material that does not break when deformed has been developed by researchers at the California Institute of Technology. The new material incorporates a scaffolding of nanotubes, which gives it ultra-low density and high strength but none of the brittleness that is seen in artificially nanostructured ceramics.
Julia Greer and colleagues created the material by arranging alumina nanotubes with diameters of about one micron into a trussed lattice structure. This familiar arrangement of criss-crossed struts is widely used in buildings and other large structures. “It turns out that there is a critical thickness-to-diameter ratio of the [nanotube] struts, below which it is possible for the nanolattice to deform via shell buckling rather than via fracture,” explains Greer.
Eight triangles bear the load
Trusses are structures comprising five or more triangular units, and Greer and Caltech graduate students Lucas Meza and Satyajit Das chose a structure that exploits eight individual triangles. Greer explains that an octet-truss is one of very few lattice geometries with mechanical behaviour dominated by stretching, rather than bending, in response to applied loads.
“The octet connectivity is maintained under stress, but each layer becomes compressed and collapses upon compression, as shown in our video,” says Greer.
The researchers experimented with structures made from alumina nanotubes with thicknesses ranging from 5 to 60 nm and diameters from 0.45 to 1.38 μm, while the unit-cell width of the nanolattice varied from 5 to 15 μm. Compression experiments, whereby a sample is subject to a cycle of loading and unloading, were performed to determine the Young’s modulus – or stiffness – of the material as well as the yield stress, which is the point at which the sample does not return to its original shape.
The walls of the nanotube structures were relatively thick compared with their diameters. Tubes with thickness–diameter ratios of more than 0.03 demonstrated linear elastic deformation (similar to rubber), with bursts of strain leading to catastrophic brittle failure. However, thinner-walled nanotubes with ratios of less than 0.02 exhibited elastic followed by ductile responses to loading. This behaviour is similar to that of metals such as copper, and does not involve strain or catastrophic failure.
Bizarre behaviour
Were the researchers surprised to find this behaviour in the thinner structures? “Of course,” says Greer. “These structures don’t fail in a brittle fashion like any macro material of the sort would, or even like the 50 nm-thick walled octet in our study.”
Eager to understand their observations, the team developed a model for the critical transition point between fracture and elastic failure. This was able to predict that the thicker alumina tubes would fail because of brittle fracture, while the thinner tubes were more prone to buckling through an elastic failure mode.
Like macro-scale engineering structures, the stress was largely localized at the nodes of the truss structures. “There are several ways to improve nodal strength,” says Greer. “But that’s not really what we are working on. Improving strength is something that engineers do; we are scientists, so we do scientific discovery and leave ‘improvements’ for engineers.”
The structures are described in Science.
- This article first appeared on nanotechweb.org