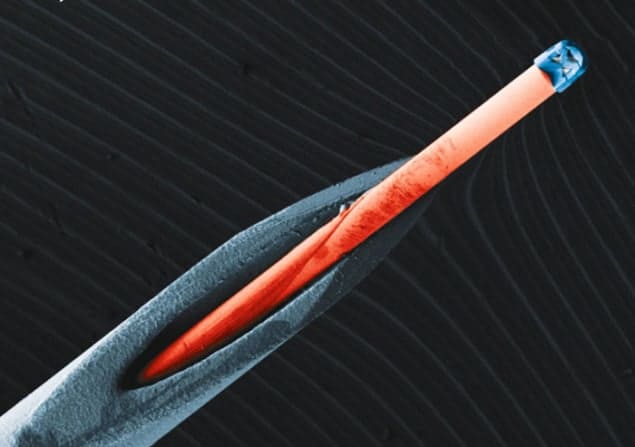
A new method for 3D-printing micro-sized, high-quality compound lenses directly onto image sensors or optical fibres has been developed by researchers at the University of Stuttgart in Germany. The technique could be used to create tiny lenses for a variety of applications, including endoscopes for medical imaging and cameras for tiny drone aircraft.
Existing methods for creating sub-millimetre-sized lenses involve injection moulding or diamond grinding. However, both techniques are limited in the size and shapes of the lenses they are capable of manufacturing. Conventional techniques are also unable to combine multiple lens elements. Together, these limitations make it very difficult to create multi-lens systems with non-spherical lens shapes, which are needed for high-performance applications.
Laser writing
Now, Timo Gissibl and colleagues have devised a new lens-manufacturing technique called two-photon direct laser writing. This uses a pulsed red femtosecond laser – with 780 nm wavelength and pulses shorter than 100 fs – focused onto a surface that is immersed in a liquid photoresist. The simultaneous absorption of two photons of the laser light at the focal point exposes the photoresist, causing polymers to crosslink and solidify to build up a transparent element on the surface.
By scanning the laser, multi-lens optical systems – composed of single lenses in a supporting shell – of any shape, configuration and size can be rapidly produced according to a previously designed computer model. When the exposure process is complete, the unexposed photoresist can be washed away with a solvent, leaving the optical element behind.
This is a giant leap forward for optics, which allows for accurate and reliable manufacturing at sizes about one order of magnitude smaller than before
Timo Gissibl, University of Stuttgart
“This is a giant leap forward for optics, which allows for accurate and reliable manufacturing at sizes about one order of magnitude smaller than before,” says Gissibl, explaining that while the micro-lens systems are only 125 μm wide – barely larger than the width of a human hair – and 200 μm long, their optical performance is similar to conventional microscope objectives, or compound photographic lenses.
The researchers have created a variety of demonstration lenses, which display some of the potential applications for the technique. In one example, the team fabricated an array of lens systems, with four refractive interfaces, which they printed directly onto five-megapixel CMOS image sensors of the kind used in digital cameras.
The technique could also be used to create extremely thin endoscopes, suitable for inserting into the smallest bodily openings, or even the innards of machinery. The team created a prototype optical system for this that involved printing three lenses onto the end of an optical fibre so thin that it could pass through a typical syringe needle. The researchers were able to show that objects 3 mm from the lens could be observed at the other end of the fibre, which was 1.7 m long.
Bee-sized robots
Other possible applications include surround-cameras for mobile phones, compact image sensors for self-driving cars and robots, and even tiny video cameras for bee-sized robot drones.
“We believe that 3D printing of optics is going to open an entire new era of optics manufacturing,” says Gissibl, highlighting the rapid nature of the optics printing process, which can go from the drawing board to a computer model and finally to a finished, printed lens in less than a day. “We are going to open potentials just like computer-aided design and computer-integrated manufacturing did in mechanical engineering a few years ago,” he adds.
“Ultrafast laser 3D lithography once again shows itself to be a unique tool for the practical realization of intelligent dreams,” says Mangirdas Malinauskas, a physicist from the Vilnius University in Lithuania, who was not involved in this study. Commending the work for up-scaling the application to produce lenses of outstanding quality, he adds: “It is obvious now that [the research] will attract the attention of both scientific groups and industrial manufacturers.”
The technique is described in Nature Photonics.